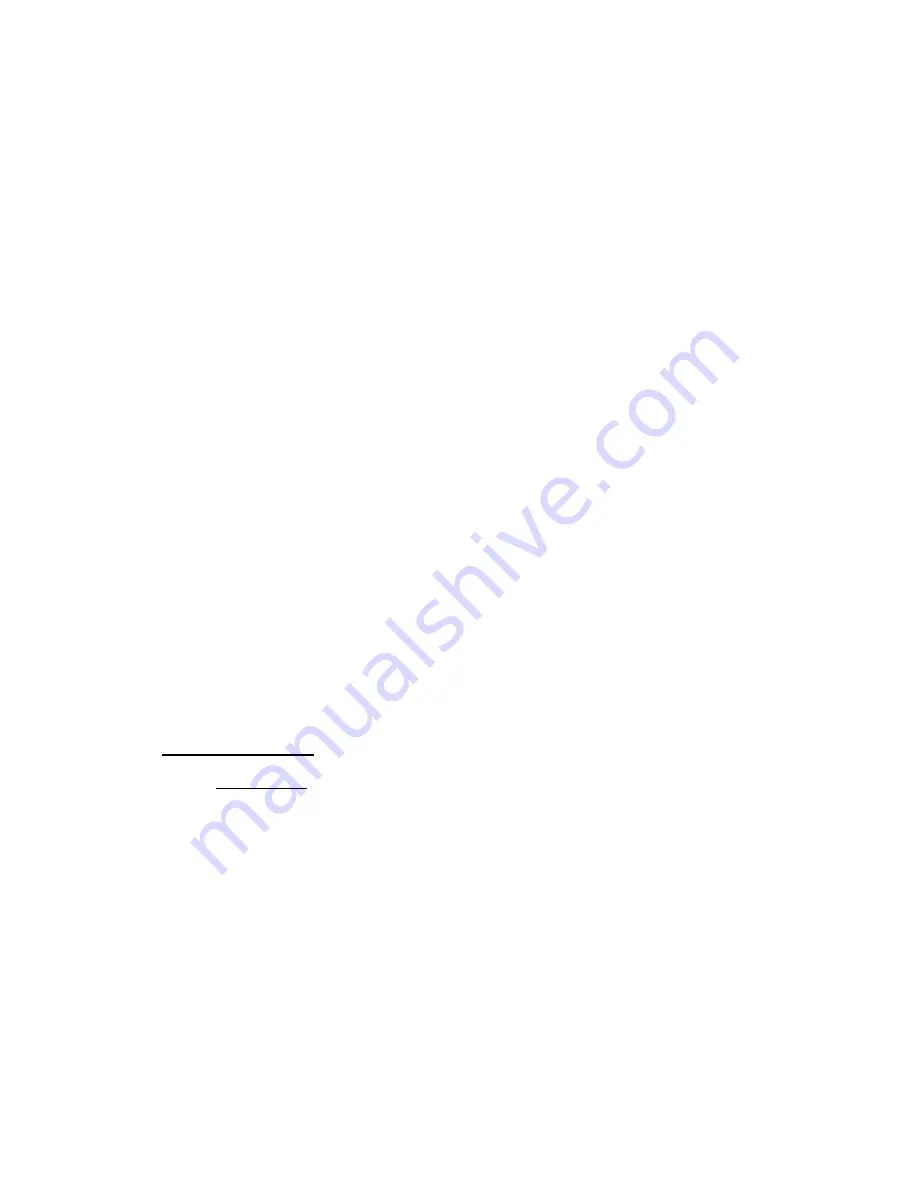
Bettis P/N 127073E
Revision “A”
Page 21 of 37
3.6.7
Install two split ring halves (7-30) into the outboard groove in piston rod (7-20) and retain
by installing retainer ring (7-40) onto the split ring halves.
3.6.8
Install Polypak seal (8-60) into outer diameter seal groove of piston (7-50). NOTE: The lip
of Polypak seal (8-60) will face toward the hydraulic override outer end cap (7-70) when
installed in the hydraulic cylinder assembly.
3.6.9
Install piston bearing (8-40) into outer diameter bearing groove of piston (7-50).
3.6.10 Install o-ring seal (8-80) into inner diameter seal groove located in the piston (7-50).
3.6.11 Use pipe dope on the threads install pipe plug (7-110) into the vent tube hole in the inboard
end of the hydraulic cylinder assembly (7-10).
3.6.12 Install vent tube (7-60) into the hydraulic cylinder assembly inboard end.
3.6.13 Install the assembled piston rod (7-20) with piston (7-50) into the open end of the hydraulic
cylinder assembly and install the piston over the vent tube (7-60).
3.6.14 Install o-ring seal (8-90) into the vent tube port located in the outer end cap (7-70).
3.6.15 Install o-ring seal (8-70) into the o-ring groove located on the inner diameter of the
hydraulic cylinder assembly flange opening.
3.6.16 Install the outer end cap (7-70) assembled piston rod (7-20) with piston (7-50) onto the open
end of the hydraulic cylinder assembly and over the vent tube (7-60).
3.6.17 Install lockwashers (7-90) onto hex cap screws (7-80).
3.6.18 Install and tighten hex cap screws (7-80), with lockwashers (7-90) through outer end cap
(7-70) and into hydraulic cylinder assembly.
NOTE: For M11 hydraulic override cylinder installations refer to Section 5 step 5.2.
3.7
ACTUATOR TESTING
3.7.1
Leakage Test - All areas where leakage to atmosphere may occur are to be checked,
using a commercial leak testing solution.
CAUTION:
Pressure applied to the actuator is not to exceed the maximum operating
pressure rating listed on the actuator name tag. Test the actuator using a
properly adjusted self relieving regulator, with gauge.
3.7.2
Cycle the actuator five times at the nominal operating pressure (NOP) as listed on the
actuator’s name tag or the customers normal actuator supply pressure. If excessive
leakage across the pistons is noted, generally a bubble which breaks three seconds or
less after starting to form, cycle the actuator five times as this will allow the seals to seek
their proper service condition.
NOTE: If excessive leakage across the piston remains, the actuator must be disassembled and
the cause of leakage must be determined and corrected.