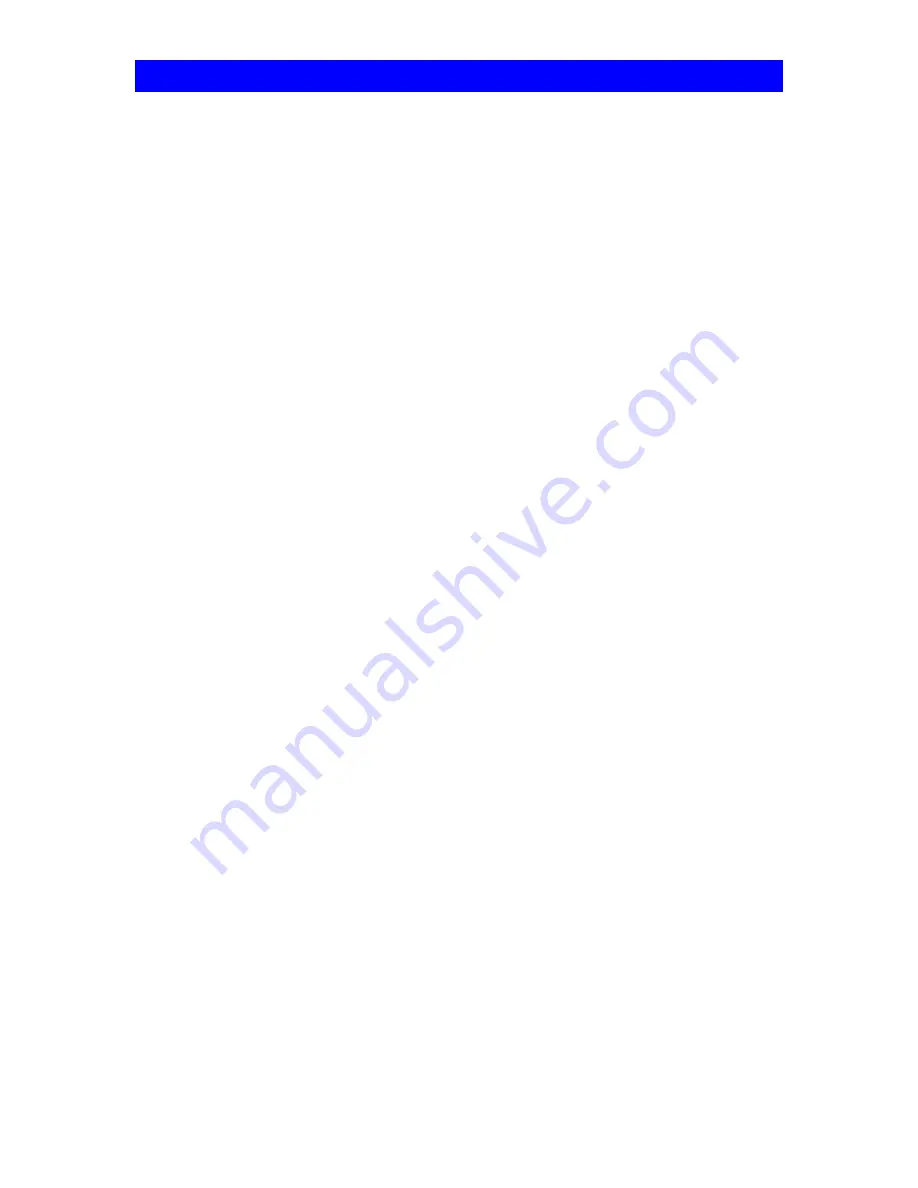
Better Water LLC; rev. May 2020
Page 55 of 78
1232 RO Operator Manual
19.
Insert the new membrane into the housing.
20.
Replace the Upper End-Cap, tightening with the tee-handle tool (
do not
over tighten
).
21.
Re-tape the 3/8" x 1/4" Fast-N-Tite with about 4 wraps of Telflon tape.
22.
Insert the 3/8" Blue Product Tubing into the 3/8" x 1/4" Fast-N-Tite.
AFTER REPLACEMENT
23.
After installation of all membranes, the RO should be started and the Product Water flushed
to drain for a
minimum of 2 hours.
Summary of Contents for 1232 RO
Page 1: ...REA 2390 1232 RO Operator Manual Better Water LLC rev May 2020 ...
Page 8: ...Better Water LLC rev May 2020 Page 4 of 78 1232 RO Operator Manual ...
Page 15: ...Better Water LLC rev May 2020 Page 11 of 78 1232 RO Operator Manual DEVICE INFORMATION ...
Page 47: ...Better Water LLC rev May 2020 Page 43 of 78 1232 RO Operator Manual SYSTEM MAINTENANCE ...
Page 74: ...Better Water LLC rev May 2020 Page 70 of 78 1232 RO Operator Manual ...
Page 80: ...Better Water LLC rev May 2020 Page 76 of 78 1232 RO Operator Manual ...
Page 82: ...Better Water LLC rev May 2020 Page 78 of 78 1232 RO Operator Manual ...