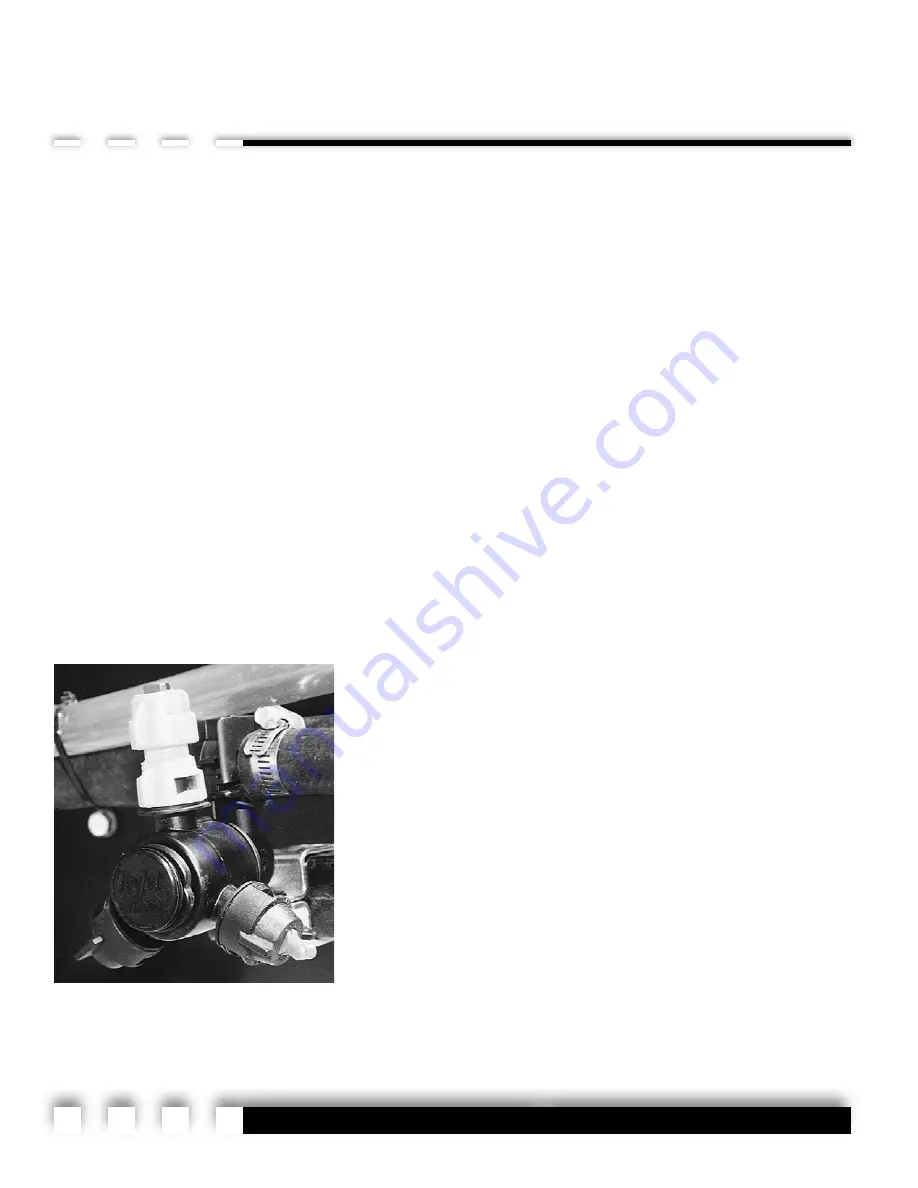
D12
•
Nozzles which produce fine droplets are usually recommended for post-emergence
applications, which require excellent coverage on leaf surfaces.
•
The most common nozzles used in agriculture are those which produce medium sized
droplets. These can be used for contact and systemic herbicide, preemergence surface
applied herbicide, insecticides and fungicides.
•
Remember that a spray nozzle in any droplet size category can produce different size
droplets at different spray pressures. A nozzle might produce medium droplets at low
pressures, while producing fine droplets as pressure is increased.
Spray Tip Turret
Each spray nozzle outlet on the Field-Pro IV has been equipped with a 360-degree nozzle
turret for fast and convenient spray tip changes in the field. With just a twist of your wrist, you can
quickly choose the right tip for the right job, assuming that different types of spray tips have been
installed on each turret.
You may wish to equip the turret with spray tips for each type of application
you perform, such as burndown, pre-emerge and post applications. Or, you may
want to equip the turret with at least two of the most commonly used tips, so a
quick change can be made in the event a tip gets plugged or damaged.
To change from one tip to another, simply rotate the turret until you hear a
“click”. Because the 360-degree turrets feature
positive shutoffs between each tip outlet, you can also use the turret to shut off
individual spray tips on the boom. Simply rotate the turret to a “click” position
between spray tip outlets. This feature is particularly useful when you need to
change nozzle spacing or reduce the swath width.
Spray tip turret in
“off” position.
Summary of Contents for field-pro IV 1600
Page 10: ...A9 A B C D E G F P N 67657 A P N DEC HAZ01 A P N 67673 B Safety Sign Locations P N DEC HAZ08 A...
Page 13: ...A12...
Page 19: ...B6...
Page 29: ...C10 Raven 450 Wiring Diagram...
Page 47: ...D14...
Page 50: ...E3 50 Hours 12 Hours 2 places 12 Hours 2 places 12 Hours Grease Zerk Locations...
Page 59: ...E12...
Page 62: ...G1 PARTS LISTING Frame and Tank Assembly...
Page 67: ...G6...
Page 68: ...G7 Base Plumbing Details...
Page 70: ...G9 Pro 90 Boom...
Page 71: ...G10 Pro 90 Boom...
Page 75: ...G14...
Page 76: ...G15 Pro 90 Boom Hydraulic Schematic...
Page 78: ...G17 Pro 90 Boom Plumbing...
Page 80: ...G19...
Page 82: ...G21 Foam Guidance System...
Page 86: ...G25 1600 1850 Gallon Rinse System Assembly...
Page 90: ...G29 Deluxe Plumbing Plate with 5 Valve Stack Assembly...
Page 92: ...H1 Base Wiring Details...
Page 94: ...H3 Control Valve Wiring Details...
Page 96: ...H5 Light Wiring Details...