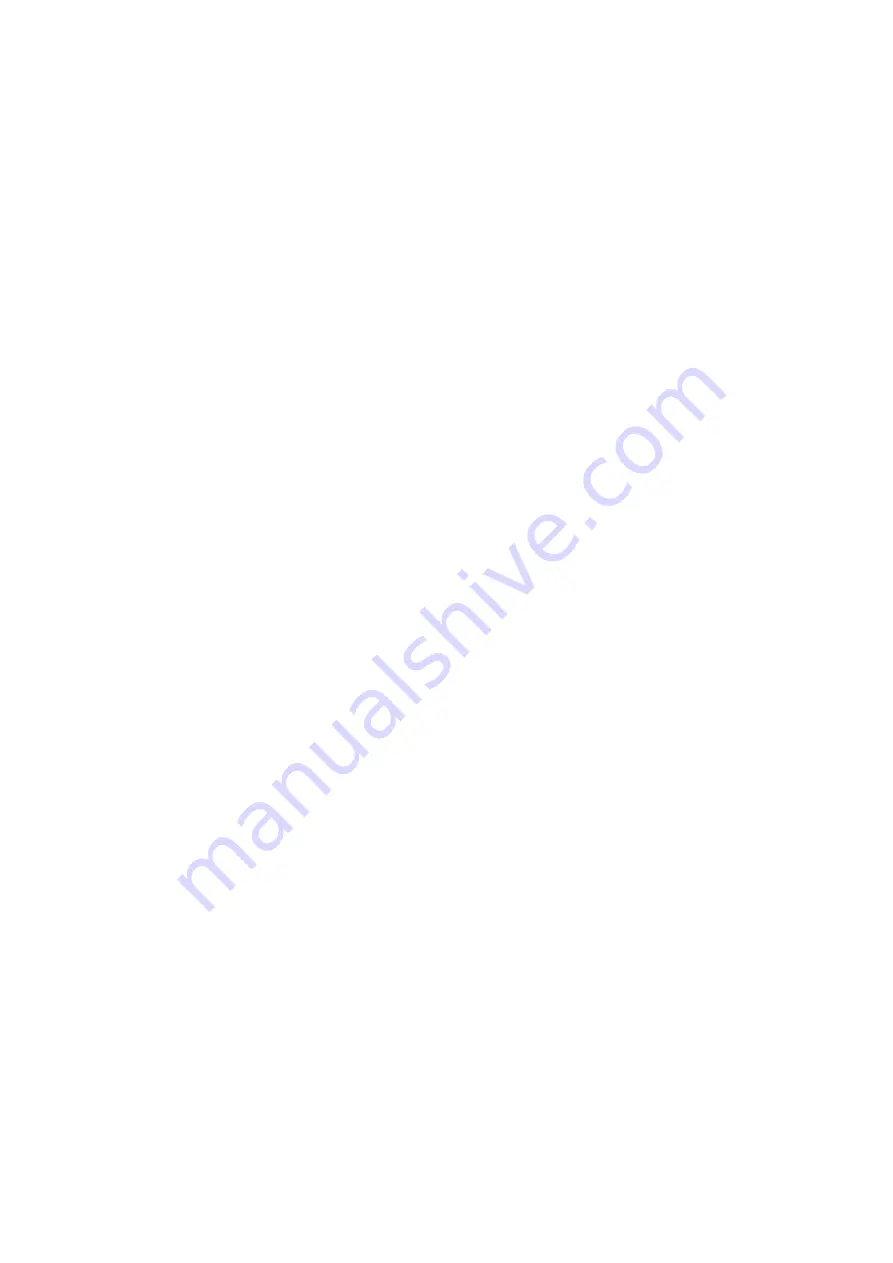
42
shaft.
In case of drive by pulleys check:
–
There is not any gap between shafts and pulleys.
–
The pulleys are parallel and aligned.
–
The belts are strained with the correct value. An excessive strain of the belts will lead
to a premature wear of the bearings.
4.2 INLET CIRCUIT
The design of the inlet circuit must be done in order to prevent the cavitation. In the follow-
ing chapter 5.2 D is described how to dimension the inlet circuit. In any case it is neces-
sary to verify with a pressure device or a pressure gauge in the inlet fitting of the pump
(point 7 in the installation scheme), that the pressure doesn’t fall under -0,2 bar.
The inlet line must have a filter with a filtering degree between 50 and 80 mesh as indicat-
ed in the chapter 5.2B. The filter produces a hydraulic loss that reduces the pump suction
capacity. For this reason the filter must have an appropriate flow rate. It is recommended
to use a filter with a capacity 2,5 times the pump flow rate.
The inlet pressure of the pump does not have to exceed 5 bar.
The diameter of the filter pipes must not be lower than the diameter of the pump inlet
pipes.
The filter must be installed as close as possible to the pump in an easily accessible posi-
tion, and must be inspected before each pump starting.
In case of pressure feed through a centrifugal pump, make sure the provided capacity is at
least 1.5 times more than the pump capacity.
In case of feed from a tank follow these instructions:
-
The tank must have a minimum capacity of four times the pump capacity per minute.
-
The pump inlet pipes must be located near the bottom of the tank, with a water head of at
least 200 mm, avoiding the formations of siphons.
-
The suction area must be protected by turbulence caused by the tank feeding pipe, and
by the return pipelines, through special bottom closed bulkheads.
The tank must be provided with the safety devices indicated in the chapters 5.2 E and 5.2
F.
-
We suggest carrying out the piece of pipeline directly next to the pump with flexible hoses,
suitable to isolate the rest of the system from the vibrations caused by the pump-
engine/motor unit.
-
Use only stiff or flexible strengthen pipes for anti-deflection.
-
The inlet pipelines must be as straight as possible, reducing as much as possible curves,
elbows and rough fluctuations of section.
-
Do not use oil-pressure pipe fittings, 90° elbows, fittings with multiple ways, wing nuts etc.
-
Do not use foot or one-way valves.
-
Do not install devices for detergent sucking in the inlet circuit of the pump.
Make sure the inlet line, before being connected to the pump, is perfectly clean inside.
Summary of Contents for C 1248
Page 8: ...7...
Page 33: ...32 PART NR 31 1547 99 2 REV 03...
Page 64: ...63 PART NR 31 1547 99 2 REV 03...
Page 96: ...95 PART NR 31 1547 99 2 REV 03...