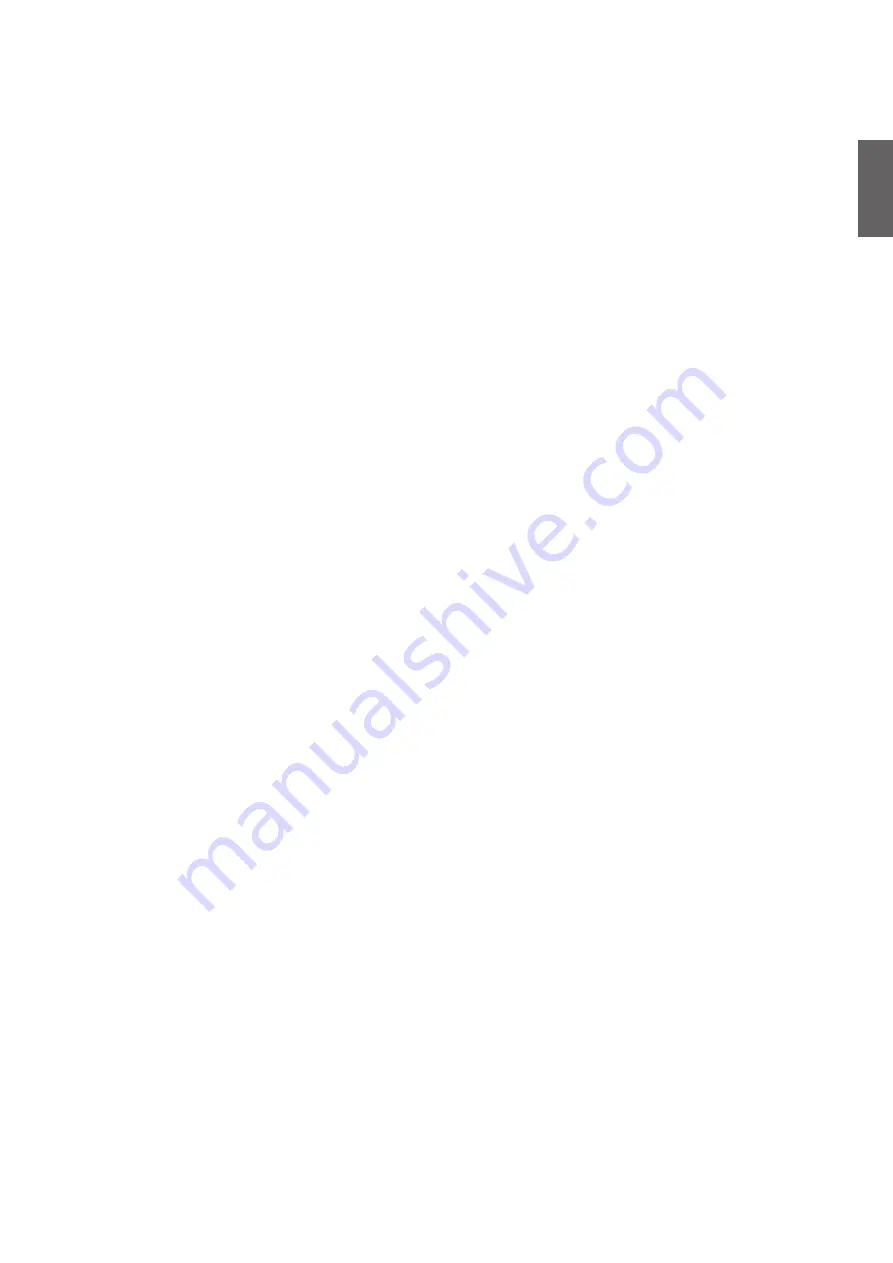
23
EN
4) INSTALLATION
4.1) OVERALL DIMENSIONS
Dimensions of the foundation plate are shown in Fig. 2.
IMPORTANT:
It is essential to keep the distance from the rack (40 mm), in order to position and remove the actuator once the rack is fitted to the gate leaf.
The types of fittings of the foundation plate are mainly the following:
4.2) INSTALLATION WITH OPTIONAL BULL.PI RAISED BEDPLATE
The BULL.PI accessory that facilitates quick fixing on existing concrete floor, is available on request.
For more information refer to the instructions supplied with the accessory.
4.3) INSTALLATION WITH ADJUSTMENT IN HEIGHT ON THE ALREADY EXISTING BASE IN CONCRETE
By using the plate as drilling template, drill 4 holes, and insert the Ø 10mm steel screw anchors for threaded bars.
Tighten the 4 threaded bars "S", M10/120mm, and anchor the screw "T" anchors by tightening the nuts “B” to floor with the corresponding washers.
With reference to Fig. 3, position the foundation plate by means of the adjustment nuts “A”. After carrying out the required regulations, position the motor
as shown in Fig.6 and lock it, as indicated in Fig.7.
4.4) INSTALLATION WITH ADJUSTMENT IN HEIGHT ON CONCRETE BASE
With reference to Fig. 4, fit the stretcher bolts on the foundation plate and provide for a hole of adequate size.
Immerse the stretcher bolts in concrete, then remove the nuts “D” and the 11x30, large band washers “R”. Move them under the plate to allow for
regulations in height of the actuator (Fig. 5).
Carry out the regulations shown in Fig. 6 and lock the motor as indicated in Fig.7.
CAUTION: apart from the fitting modality used, carefully check that the actuator is steadily positioned and the materials are suited to the intended use.
4.5) RACK FIXING
Galvanized steel rack, 123x30mm.
Position the spacers D by welding or fit them to the gate with screws at 130/150mm height from the centre line of the slot used for fitting to the base on
which the foundation plate is to be fixed.
Keep the pitch of teeth between the two parts of the rack; the joining with another piece of rack would make it easier to achieve (see Fig.8)
Secure the rack with the screws V making sure, once the actuator has been installed, that between rack and the drive gear there is always approx. 1mm
clearance (see Fig.9); to get this clearance use the slots on the rack.
5) MANUAL OPERATION (FIG. 12-13-14)
In the event of power failure or malfunction, to manually operate the gate proceed as follows:
- After inserting the customized key C, turn it anti-clockwise and pull the lever L (opened padlock)
- The geared motor is unlocked and the gate can be moved by hand.
- To return to the normal operating mode, close the lever L again and manually activate the gate until it is geared.
6) HOW TO POSITION THE LIMIT SWITCH BRACKETS
Open manually the gate and leave approximately of 1÷3cm, depending on gate weight, between gate and positive mechanical stop A; tighten the limit
stop flask S with the grains G to press the limit stop micro. Repeat the sequence with closing gate.
7) HOW TO INSTALL THE MAGNETS (BULL 1224 TURBO.S OR ACCESSORY MLS) FIG.11
The magnets are housed in special supports (fig.12-”A”). These magnets are to be fitted to the limit switch brackets or the rack and cause the triggering
of sensors when they approach them.
7.1) FITTING ONTO THE LIMIT SWITCH BRACKETS
The bases are complete with hooking tongue allowing the fitting of the magnets to the limit switch bracket supplied with the operator, as shown in Fig.12-B.
This type of fitting allows to rapidly adjust the position of magnets. After calculating the correct distance, fix the support in the correct position by means
of a screw, so as to avert the moving of the bracket.
7.2) FITTING ONTO THE RACK
As an alternative, the supports can be fitted directly to the rack, by using the slots shown in Fig. 12-C. This fitting mode does not allow for subsequent
regulations. It is therefore advised to make some trials with temporarily fitted supports before carrying out the final fitting.
IMPORTANT:
The correct distance of the magnet with respect to the sensor depends on the installation characteristics. This space cannot be preset
and must be adjusted on a trial basis.
The distances regarding the triggering of the sensor (value X) with respect to distance K of 3 and 35 mm, which are shown in Fig. 12are only indicative.
In any case, distance K must not exceed 35 mm as a higher distance will not allow the triggering of the magnetic sensor.
Summary of Contents for BULL 1224 TURBO
Page 2: ...2 A B 1 200 245 316 400 300 215 400 34mm BULL PI Optional 40 3 1 8 2 0 4 7 0 1 8 0 2 3...
Page 3: ...3 V Z R 4 7 B F T MIN 10 mm MAX 20 mm MIN 120 mm MAX 140 mm 5 6 R D R D...
Page 5: ...5 12 13 14 C L 7 4 1 2 3 POWER 2 x 1 5 RG 58 5 4 x 0 25 4 6 5 2 x 0 25 3 x 0 25 15...
Page 7: ...7 18 19 A B C...
Page 75: ...75...