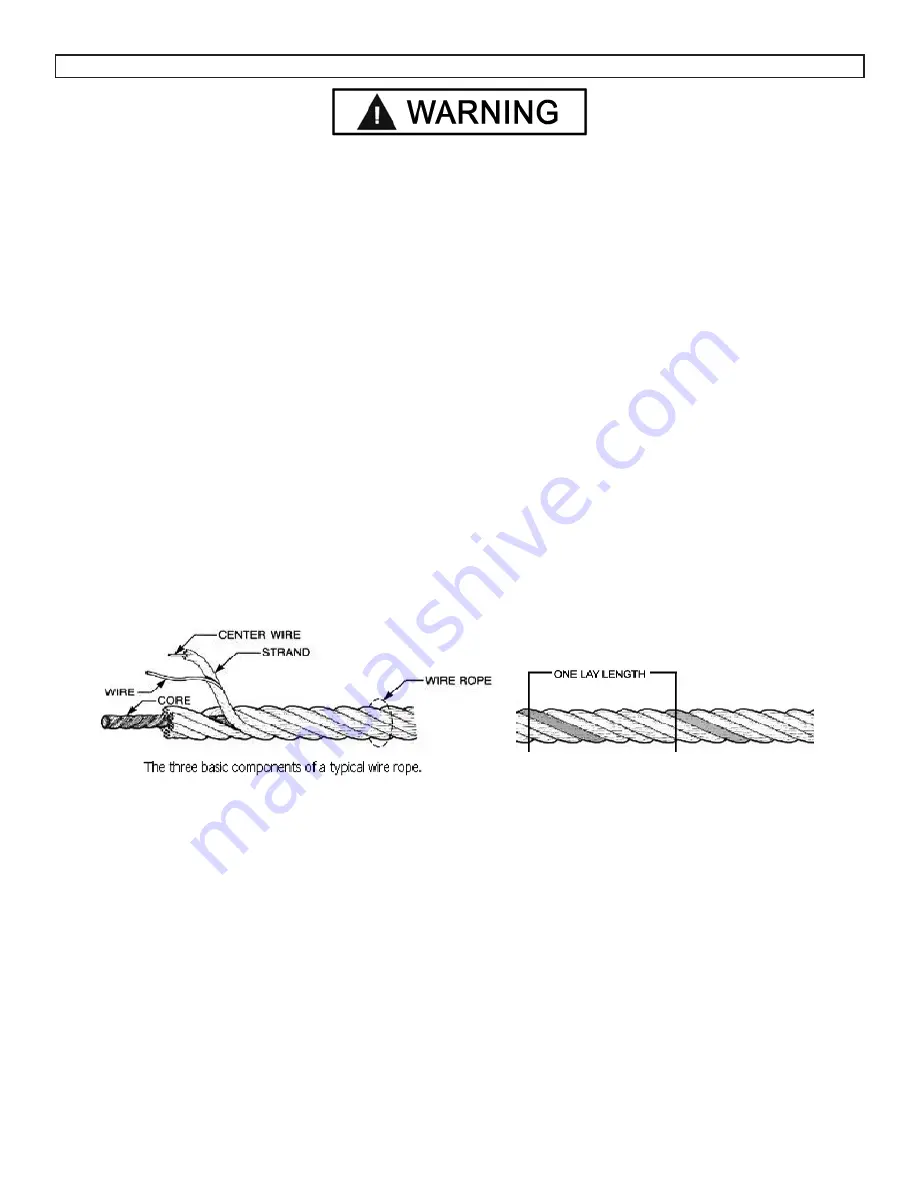
32
t
Lifting cables should be replaced every three to five years or when visible signs of damage are apparent.
DO NOT
USE LIFT WITH DEFECTIVE / WORN CABLES.
t
Lifting cables should be maintained in a well-lubricated condition at all times. Wire rope is only fully protected when each
wire strand is lubricated both internally and externally. Excessive wear will shorten the life of the wire rope. The factory sug-
gested wire rope lubricant that penetrates to the core of the rope and provides long-term lubrication between each individual
strand is 90-WT gear oil or ALMASOL® Wire Rope Lubricant. In order to make sure that the inner layers of the rope remain
well lubricated, lubrication should be carried out at intervals not exceeding three months during operation.
t
All sheaves and guide rollers in contact with the moving rope should be given regular visual checks for surface wear
and lubricated to make sure that they run freely. This operation should be carried out at appropriate intervals generally not
exceeding three months during operation. For all sheave axles, the factory recommends standard wheel bearing grease.
For all sheaves and/or guide rollers, the factory recommends 90-WT gear oil or similar heavy lubricant applied by any
method including pump / spray dispensing, brush, hand and/or swabbing.
.
HOW OFTEN TO INSPECT
t
Lifting cables should be visually inspected at least once each day when in use, as suggested by American Petroleum
Institute (API) RP54 guidelines.
t
Any lifting cable that has met the criteria for removal from service must be immediately replaced.
WHEN TO REPLACE LIFTING CABLES DUE TO BROKEN WIRES
t
Lifting cables should be removed from service when you see six randomly distributed broken wires within any one lay
length, or three broken wires in one strand within one lay length.
OTHER REASONS TO REPLACE LIFTING CABLES
t
Corrosion that pits the wires and/or connectors.
t
Evidence of kinking, crushing, cutting, bird-caging or a popped core.
t
Wear that exceeds 10% of a wire’s original diameter.
t
Evidence of heat damage.
HOW TO FIND BROKEN WIRES
t
The first step is to relax your rope to a stationary position and move the pick-up points off the sheaves. Clean the
surface of the rope with a cloth — a wire brush, if necessary — so you can see any breaks.
t
Flex the rope to expose any broken wires hidden in the valleys between the strands.
t
Visually check for any broken wires. One way to check for crown breaks is to run a cloth along the rope to check for
possible snags.
t
With an awl, probe between wires and strands and lift any wires that appear loose. Evidence of internal broken wires
may require a more extensive rope examination.
WIRE ROPE INSPECTION AND MAINTENANCE
Summary of Contents for PL-14000
Page 25: ...25 ...
Page 29: ...29 Not provided by BendPak 4450mm lg 2500mm lg 2200mm lg Multiple Unit Hydraulic Hose Routing ...
Page 35: ...35 ...
Page 36: ...36 ...
Page 41: ...41 Grease Port Lubrication Locations Lubricate Once A Week ...
Page 43: ...43 ...