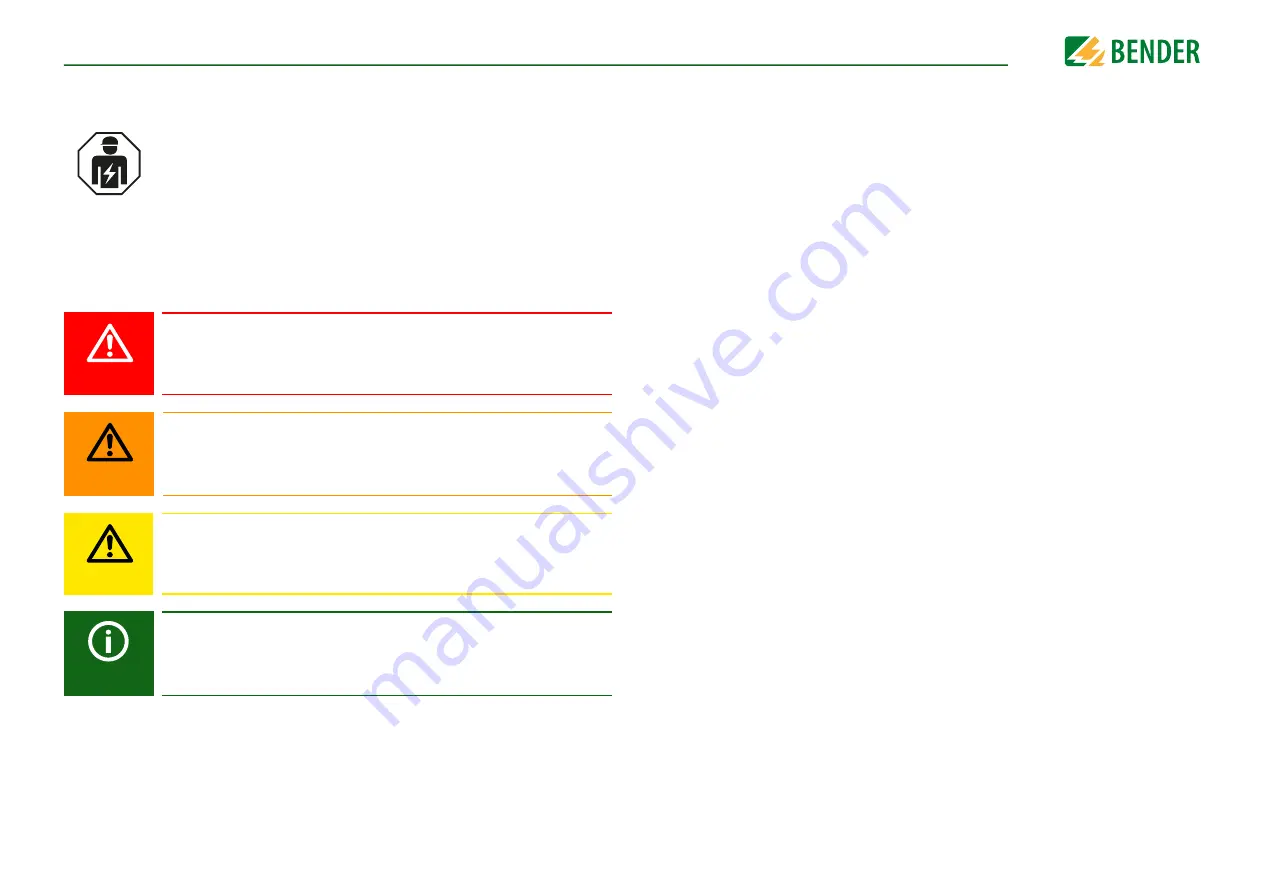
isoNAV685-D_D00215_02_M_XXEN/04.2017
6
Important information
1. Important information
1.1 How to use this manual
Always keep this manual within easy reach for future reference.
To make it easier for you to understand and revisit certain sections in this manual, we
have used symbols to identify important instructions and information. The meaning of
these symbols is explained below:
This manual is intended for
qualified personnel
working in electrical en-
gineering and electronics!
This signal word indicates that there is a
high risk of danger
that will re-
sult in
electrocution
or
serious injury
if not avoided.
This signal word indicates a
medium risk of danger
that can lead to
death
or
serious injury
if not avoided.
This signal word indicates a
low level risk
that can result in
minor or mo-
derate injury
or
damage to property
if not avoided.
This symbol denotes information intended to assist the user in making
optimum use
of the product.
DANGER
WARNING
CAUTION
1.2 Technical support
For commissioning and troubleshooting Bender offers you:
1.2.1 First level support
Technical support by phone or e-mail for all Bender products
• Questions concerning specific customer applications
• Commissioning
• Troubleshooting
Telephone:
+49 6401 807-760*
Fax:
+49 6401 807-259
In Germany only:
0700BenderHelp (Tel. and Fax)
E-mail:
1.2.2 Repair service
Repair, calibration, update and replacement service for Bender products
• Repairing, calibrating, testing and analysing Bender products
• Hardware and software update for Bender devices
• Delivery of replacement devices in the event of faulty or incorrectly delivered
Bender devices
• Extended guarantee for Bender devices, which includes an in-house repair service or
replacement devices at no extra cost
Telephone
:
+49 6401 807-780** (technical issues)
+49 6401 807-784**, -785** (sales)
Fax:
+49 6401 807-789
E-mail:
Please send the devices for
repair
to the following address:
Bender GmbH, Repair-Service,
Londorfer Strasse 65,
35305 Grünberg