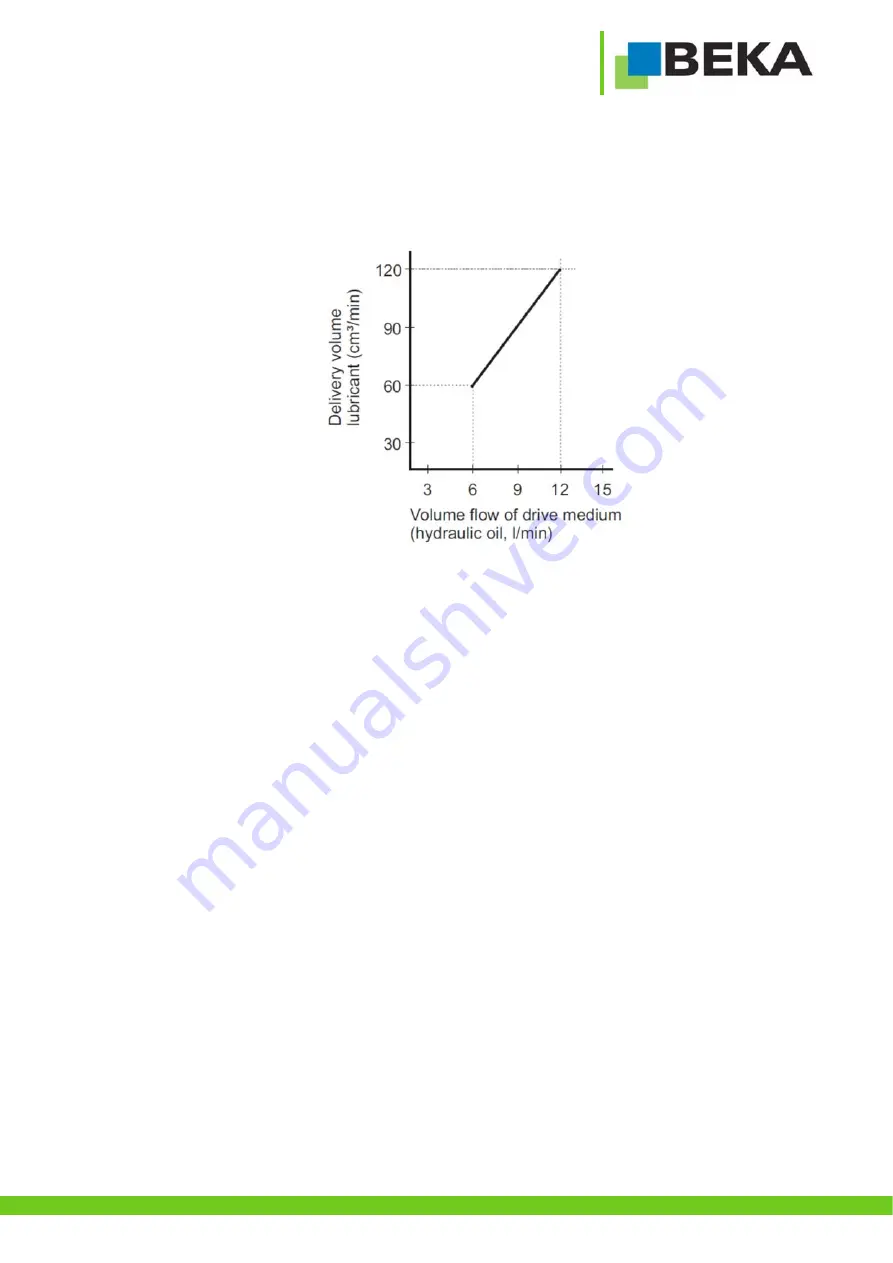
Page
21 ©
BEKA 2019 All rights reserved!
...a product of
10.6 Delivery
volume
The device delivers a constant delivery volume of 120 cm³/min from a volume flow of the drive medium of 12 l/min (The volume flow
of the drive medium is internally limited to max. 12 l/min).
If the volume flow of the drive medium is lower, the volume flow changes as shown in the figure (fig. 23).
Delivery volume depending on volume flow:
Figure 23