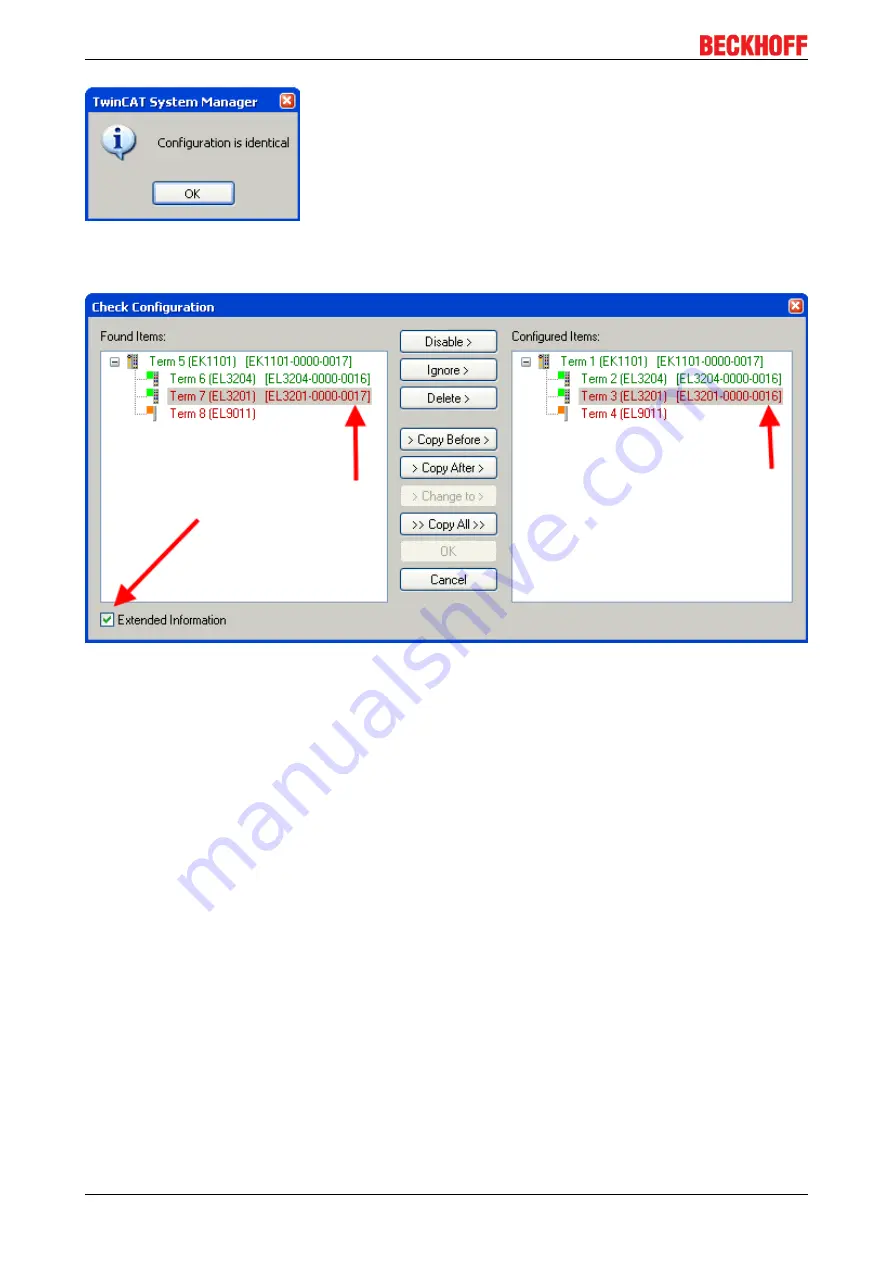
Commissioning/Configuration
EP1xxx
100
Version: 2.5.0
Fig. 78:
Configuration is identical
otherwise a change dialog appears for entering the actual data in the configuration.
Fig. 79:
Change dialog
In this example in Fig.
"Change dialog"
, an EL3201-0000-
0017
was found, while an EL3201-0000-
0016
was
configured. In this case the configuration can be adapted with the
Copy Before
button. The
Extended
Information
checkbox must be set in order to display the revision.
Changing the ESI slave identifier
The ESI/EEPROM identifier can be updated as follows under TwinCAT:
• Trouble-free EtherCAT communication must be established with the slave.
• The state of the slave is irrelevant.
• Right-clicking on the slave in the online display opens the
EEPROM Update
dialog, Fig.
"EEPROM
Update"