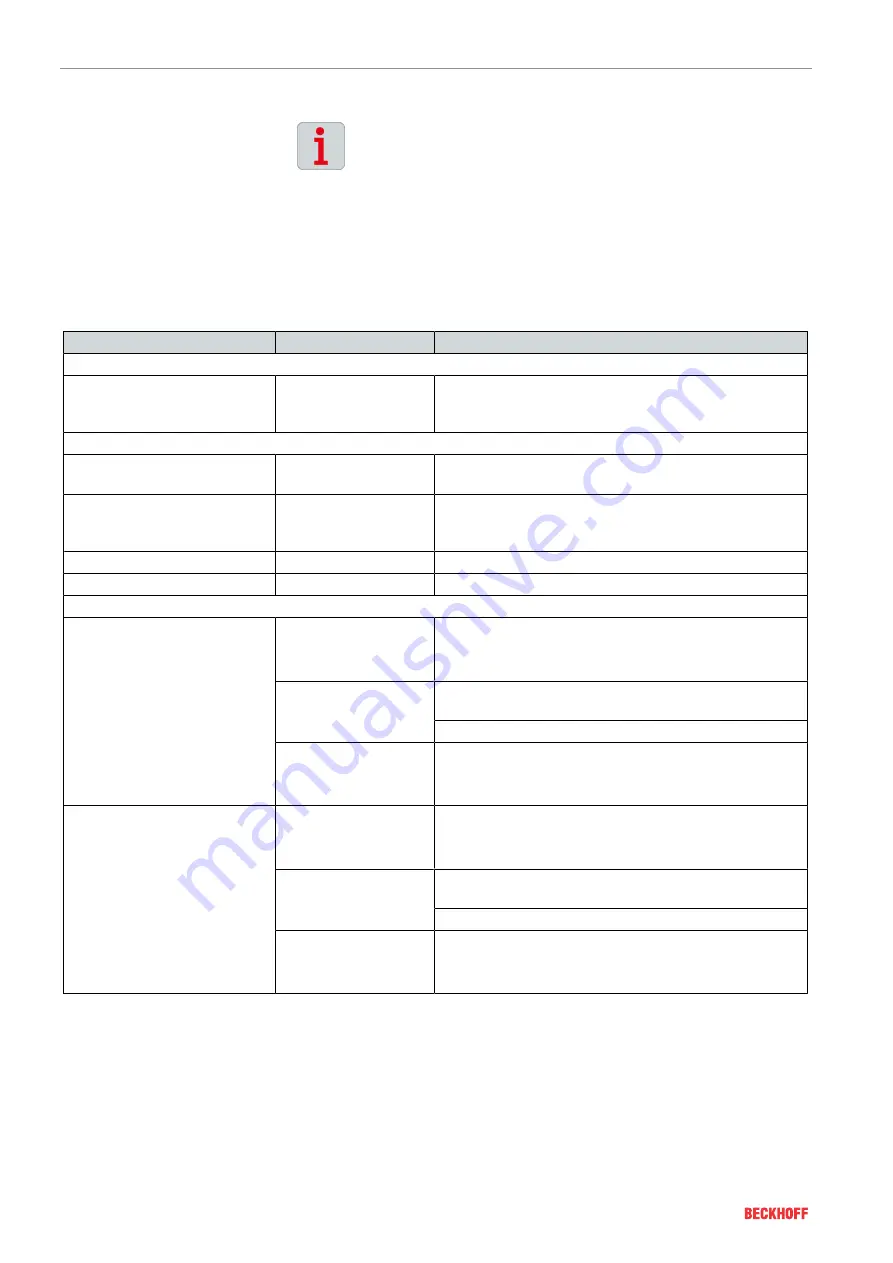
Maintenance and cleaning
84
───
Version: 1.0
eXtended Transport System
10.2
Intervals
Adapt the maintenance cycles in case of higher loads
Operation at the limits of the permissible environmental conditions
and operating states will shorten the intervals. Depending on the
mechanical dynamics due to mounted devices and movements, the
service life of the mover rollers may be shortened. Therefore, adapt
the maintenance cycles to the respective load on the system.
We have provided you with a list of maintenance work and intervals
for the associated components below. The intervals are based on
the total operating time of the system and not on the operating time
of individual components. The data apply to laboratory conditions
and a relative humidity of 50% at 25 °C:
Component
Interval
Maintenance
Complete system
Seals
6 months
and after each high-
pressure cleaning
Visual inspection to ensure seals are seated correctly
Modules
Module side surfaces
2 weeks
Visual inspection for abrasion marks on the magnet
carriers
Interface cover
6 months
Unscrew the cover
Check the interface for moisture
Replace the seal if necessary
Feedback Sensor System
6 months
Visual inspection of the sensor surfaces for abrasion
Machine bed
6 months
Check the fastening of the modules to the machine bed
Guide rails
Straight guide rails
Every month
Clean the running surfaces
Recommended cleaner:
Isopropanol
6 months
Check all connections for firm seating, abrasion marks,
corrosion and wear
Check the fastening of the guide rails to the modules
As required
Lubricate the running surfaces of the curves
Recommended lubricant:
Vaseline
Curved rails
Every month
Clean the running surfaces
Recommended cleaner:
Isopropanol
6 months
Check all connections for firm seating, abrasion marks,
corrosion and wear
Check the fastening of the curved rails to the modules
As required
Lubricate the running surfaces
Recommended lubricant:
Vaseline