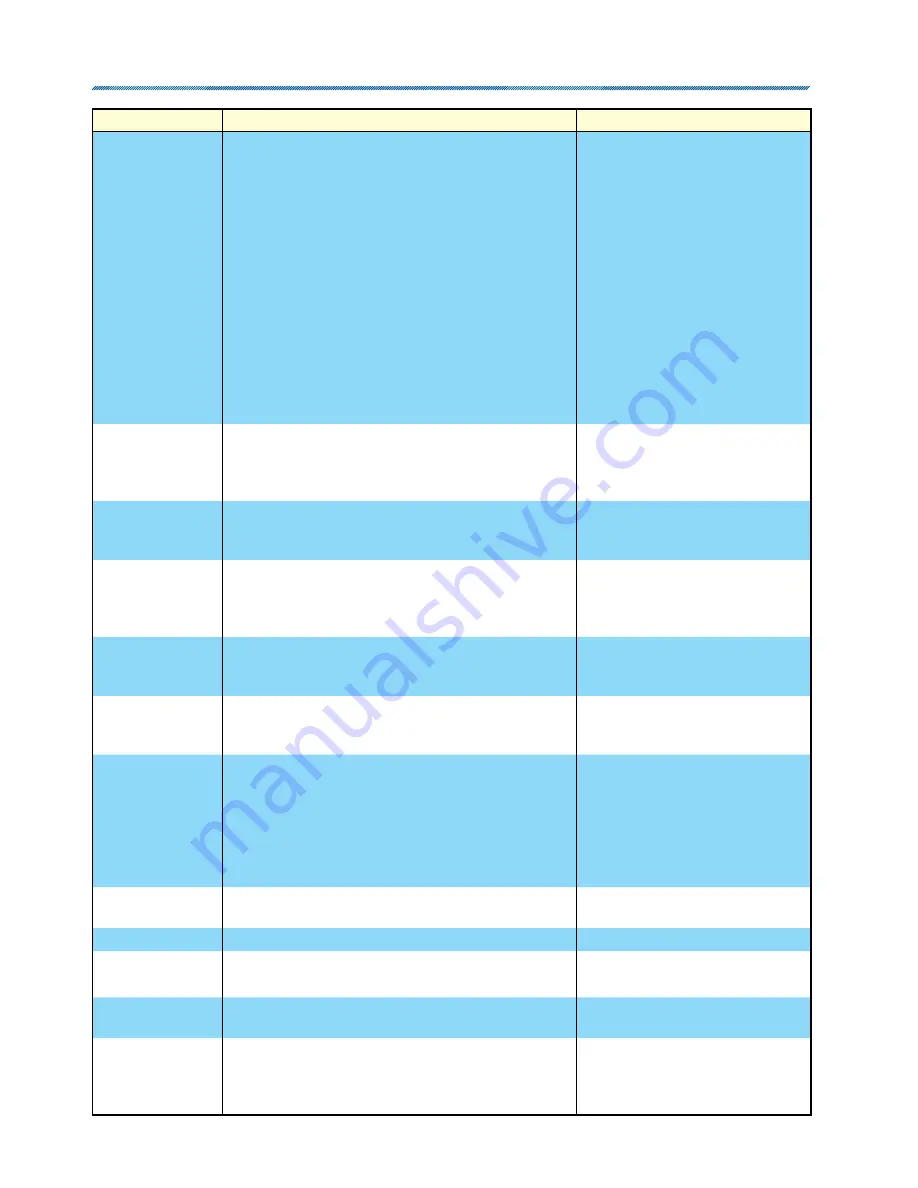
80-4280-10, Rev. 4
65
Command
Description
Argument
n
and Information
alarmoutmask
n
Sets/displays (in hexadecimal format) which
conditions will cause an alarm:
0x00000001 - Demand Loss of Signal
0x00000002 - Torque High
0x00000004 - Stall Condition
0x00000008 - Torque Stop
0x00000010 - Stop/Limit
0x00000020 - Feedback Loss of Signal
0x00000040 - Temperature too High/Low
0x00000080 - Position Outside of Limits
0x00000100 - Real-time Clock Failure
0x00000200 - Torque Measurement Failure
0x00000400 - Position Analog/Digital Circuit Failure
0x00000800 - Demand Measurement Failure
0x00002000 - Position Loss of Signal
0x00004000 - Temperature Measurement Failure
0x00008000 - Memory Failure
0x00010000 - Invalid Button Pressed
0x00020000 - Demand too High
n
= "0x0": no listed condition
causes a status alarm
n
= "0xffffffff": all listed conditions
cause a status alarm
n
= hexadecimal value for specific
condition(s) which will cause
an alarm. Multiple conditions
may be selected by performing
a hexadecimal addition of the
condition values; e.g., Stall
Condition and Torque Stop alarms
--
hex
0x04 + 0x08 = 0x0C.
configformodel
n
Sets certain DCM-2 default values based on the
actuator Serial number. These values are direction
rotation for an increasing CPS-4 signal, expected
range of CPS-4 signal and the maximum travel.
n
= "1": executes command
drvdir
n
Sets/displays the actuator output shaft rotation
direction resulting from an increasing Demand
signal.
n
= "0": CW rotation
n
= "1": CCW rotation
drvtiming
n
Sets/displays number of seconds the actuator
takes to travel from 0% to 100%. Also indicates
frequency of motor voltage as provided by the
DCM-2.
n
= seconds
gearratio
n
Sets/displays the gear ratio from the motor to the
output shaft.
See page 7 for
n
value (gear
ratio) appropriate for the actuator
model and stroke timing.
limitalarm
n
Sets/displays alarm action if the actuator travels
outside of the electronic limits and contacts an over-
travel limit switch.
n
= "0": mute (no alarm)
n
= "1": always
opmode
n
Sets/displays the mode that controls the Demand
signal source. This mode selects analog or digital
control.
n
= "0": analog Demand
n
= "1": digital Demand
n
= "2": run CW
n
= "3": run CCW
n
= "4": stay
n
= "5": stop
restoremodes
n
Returns the DCM-2 settings to the original factory
configuration.
n
= "1": executes command
sernum
n
Sets the actuator serial number.
n
= serial number
stallprot
n
Sets/displays stall protection state.
n
= "0": disabled
n
= "1": enabled
stalltime
n
Sets/displays time the actuator runs in one direction
before stall alarm is activated.
n
= seconds: acceptable range is
30–300 seconds.
stepsize
n
Sets/displays the size of one incremental movement
of the output shaft.
n
= % of travel desired: acceptable
range is 0.10%–2.5%. Include "%"
symbol after number, otherwise the
unit of measure will be degrees.