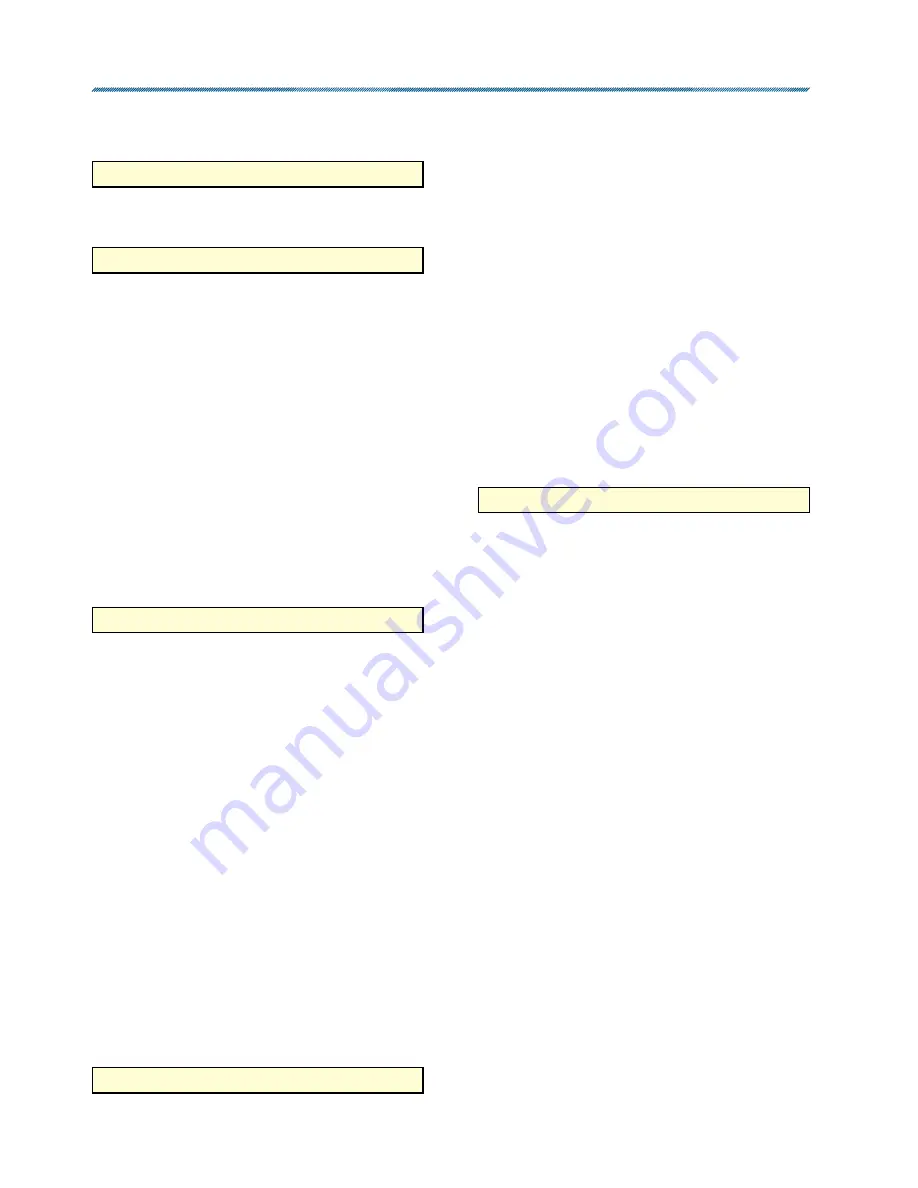
80-4280-10, Rev. 4
1 Starts
: The total number of motor starts.
2 Reversals
: The total number of times the
motor has started in the direction opposite to
the previous start.
3 Stalls
: The total number of times the stall time
has been exceeded.
4 OverTorques
: The total number of times that
excessive torque was detected at the output
shaft.
5 Pk Torque
: The highest recorded torque on
the output shaft.
6 TotRunTm
: Total amount of time the motor
has been powered (in seconds).
7 High Temp
: Highest temperature recorded
in the DCM-2 compartment (in degrees
fahrenheit).
8 Low Temp
: Lowest temperature recorded in the
DCM-2 compartment (in degrees fahrenheit).
MENU 3E -- Manual Operation
This menu is used to allow manual operation
using HART
®
communications. There are three
manual operation procedures available:
1 Op mode (Menu 4G):
Selects the operating
mode of the DCM-2. There are six possible
choices: “Follow”, “Hold”, “RunCW”,
“RunCCW”, “Stay” and “Stop”. “Follow” mode
is the normal state of operation and allows
the DCM-2 control in response to the analog
input Demand signal. “Hold” mode forces
the DCM-2 to position according to the HART
Demand value (see right). “RunCW” mode
forces the actuator to move CW. “RunCCW”
forces the actuator to move CCW. The “Stay"
mode forces the actuator to maintain its
present position. Note that in "Stay" mode,
the Handwheel cannot be freely turned. The
"Stop" mode removes power from the motor.
Note that in "Stop" mode the Handwheel can
be freely turned. Note that the Handswitch
overrides all operating modes.
2 Demand
: This procedure sets the effective
Demand signal. If "Op mode" is set to
"Hold", entering a valid value (-5% to 105%)
will control the motor. If "Op mode" is set
to "Follow", the analog Demand signal is
displayed (unless an alarm condition exists).
3 Reset Stall
: This procedure resets normal
actuator operation after a stall condition has
caused the motor to shut down. Note that
stall conditions can also be reset by simply
reversing the input Demand signal or cycling
the actuator AC power.
55
the signal is brought below this level. This
value should be set above "DemRngUpr".
MENU 5A -- Dem Curve Spcl
This menu allows setting the Demand signal
characterization curve.
MENU 4E -- Feedback Setup
This menu is where all the Feedback signal
related actuator parameters are set.
1 FBRngLwr
: The value of the Feedback signal
(in mA) that corresponds to a 0% output shaft
position. This value can range between 3.00
mA and 16.00 mA (default = 4.00 mA).
2 FBRngUpr
: The value of the Feedback signal
(in mA) that corresponds to a 100% output
shaft position. This value can range between
7.00 mA and 21.00 mA (default = 20.00 mA).
3 Feedback
: Enables or Disables the Feedback
signal.
4 FB Curve
: Allows a choice in the relationship
between the applied Feedback signal and the
actual position of the actuator. Choices are:
Linear & Inverted Demand (“InvDem”).
MENU 4F -- Torque Setup
This menu is where all the Torque related
actuator parameters are set.
1 Trq/Thrust
: Enables or disables torque
sensing.
2 Ovt Prot
: Enables or disables overtorque
protection which will remove power from the
motor if excessive torque is detected.
3 AlarmLevel
: Sets the value that, if exceeded,
will cause the Torque Alarm to activate (20–
105%).
4 ShutDwnTrq
: Sets the output shaft torque in
percentage of actuator rating that, if exceeded,
removes power from the motor (25–115%).
5 Trq Null
: The torque sensor value that
represents 0% output shaft torque. This value
is unique for each actuator and may be found
on a label inside the DCM compartment.
6 Trq Const
: The internal DCM-2 signal span
associated with the output shaft torque. This
value is determined during manufacture and is
noted on a label inside the DCM compartment.
MENU 3D -- Statistics
This menu is where all the actuator’s stored
operating statistics are
available.