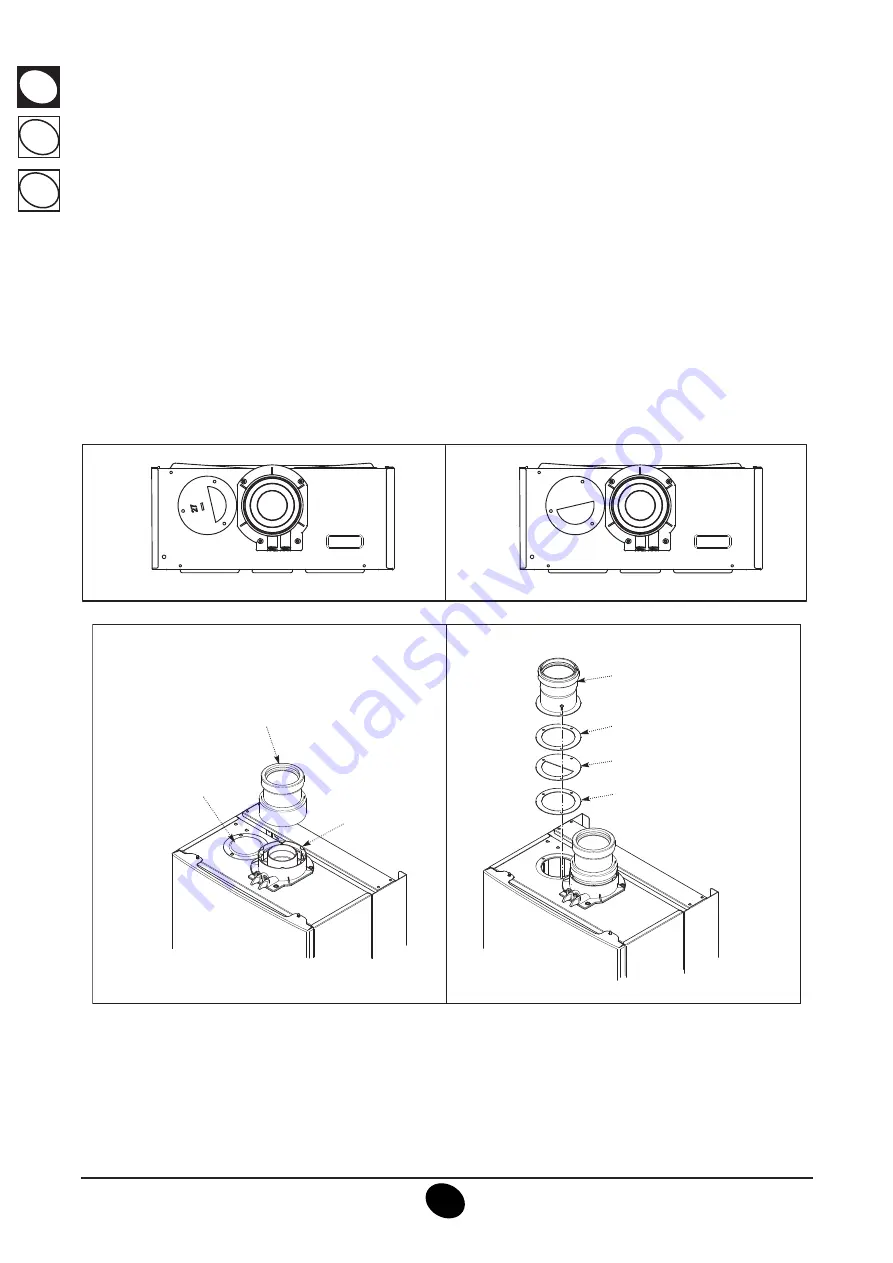
BAXI - 925.200.1
12
GB
HU
CZ
INSTRUCTIONS PERTAINING TO THE INSTALLER
925.492.2
IMPORTANT
:
If the fl ue system is to be fi tted prior to the boiler, temporary precautions must be taken to prevent
rain entry into the room of installation. Any precautionary measures must be removed prior to fi tting the boiler.
Flue Duct Adaptor
Engage the fl ue duct adaptor on the boiler adaptor, making sure that it is pushed down as far as possible.
Air Duct Adaptor
Undo the screws securing the blanking plate to the boiler top panel. Discard the plate.
There is a restrictor plate supplied in the kit with the gas boiler. This restrictor is used either way up depending upon model
of boiler - see fi gure 9.
IMPORTANT:
The restrictor MUST be positioned as shown in the diagrams below.
Take one of the gaskets supplied in the kit and place on the boiler top panel.
Align the appropriate restrictor as shown. Position the second gasket over the restrictor.
Using the screws previously removed secure the air duct adaptor to the top panel.
Continue to fi t the twin fl ue system.
Position of Restrictor model 240 Fi Position of Restrictor model 310 Fi
Figure 9a
Figure 9b
Flue Duct
Adaptor
Air Duct
Adaptor
Gasket
Restrictor
Gasket
Blanking Plate
BoilerAdaptor
Figure 9a
Figure 9b