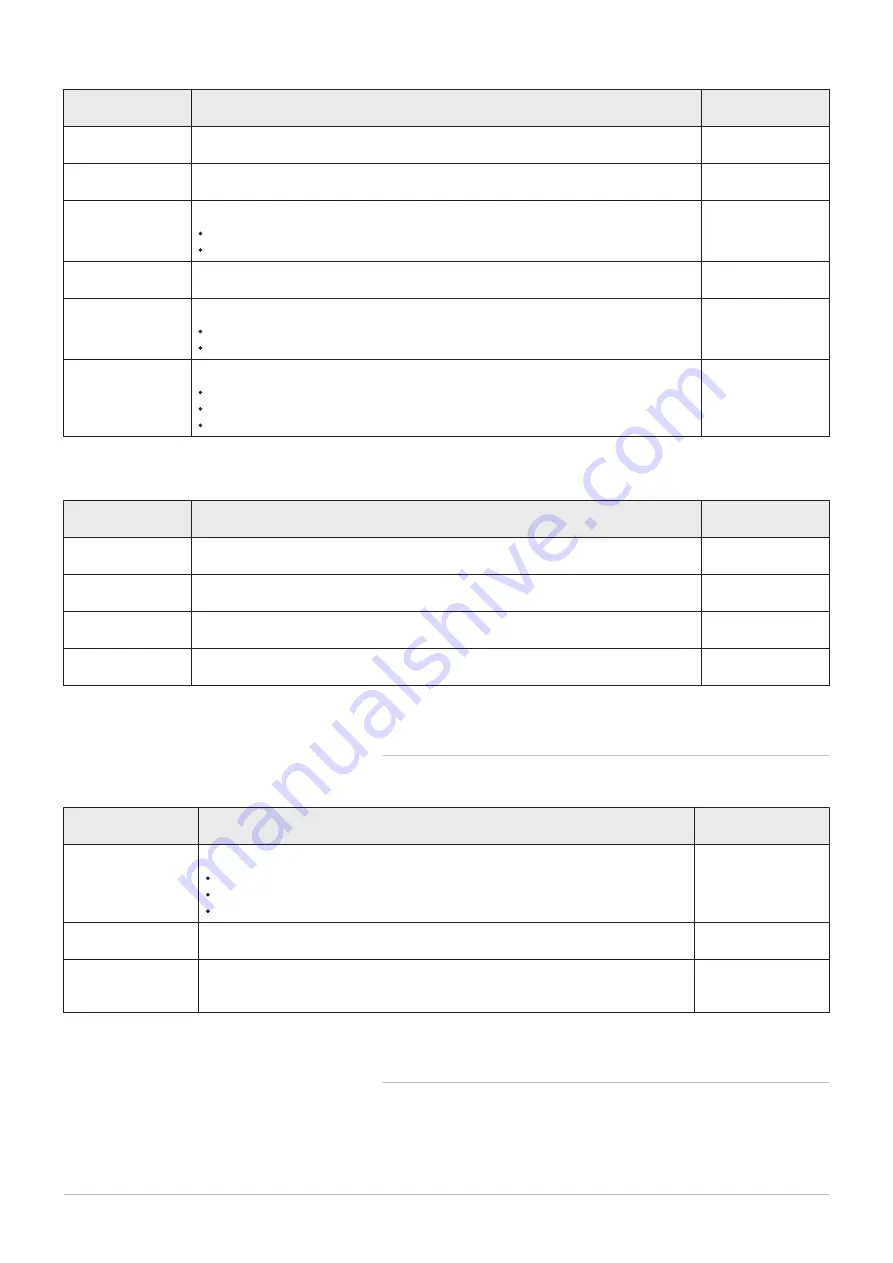
Parameter
Description
Factory setting
SCB-10
CascInterStageTim
e (NP009)
Switch on and switch off timing for the producer of the cascade
Can be set from 1 Min to 60 Min
4
CascTOutsideCool
Para (NP010)
Outdoor start temperature cooling of all stages in parallel mode
Can be set from 10 °C to 40 °C
30
CascadeTypeAlgo
(NP011)
Choice of Cascade Algorithm type, power or temperature
Temperature
Power
Temperature
CascPowerRiseTi
me (NP012)
Cascade, Time to reach Temperature Septoint
Can be set from 1 to 10
1
CascForceStop
Pprim (NP013)
Force Primary Pump to Stop on cascade
No
Yes
No
Cascade Mode
(NP014)
Functionnement Mode of cascade : automatic, heating or cooling
Automatic
Heating
Cooling
Automatic
Tab.79 Adv. Parameters
ADV parameter
Description of the ADV advanced parameters
Factory setting
SCB-10
NP001
Hysterese high for Producer Manager
Can be set from 0.5 °C to 10 °C
3
NP002
Hysterese low for Producer Manager
Can be set from 0.5 °C to 10 °C
3
NP003
Maximum error gain for Producer Manager
Can be set from 0 °C to 10 °C
10
NP004
Proportional Factor for cascade with Temperature algorithm
Can be set from 0 to 10
1
9.4.6
Installation Setup > Outside temp > Parameters,
counters, signals
Tab.80 Parameters
Parameter
Description
Factory setting
SCB-10
Outdoor sensor
(AP056 )
Enable outdoor sensor
No outside sensor
AF60
QAC34
1
Summer Winter
(AP073)
Outdoor temperature: upper limit for heating
Can be set from 15 °C to 30.5 °C
22
Season cross-over
(AP075)
Temperature variance from set outdoor upper temp. limit in which the generator
will not heat or cool
Can be set from 0 to 10 °C
4
9.4.7
Installation Setup > Digital input > Parameters, counters,
signals
EP : Entry Parameters = Input parameters
9 Settings
74
7762758 - v05 - 19082020