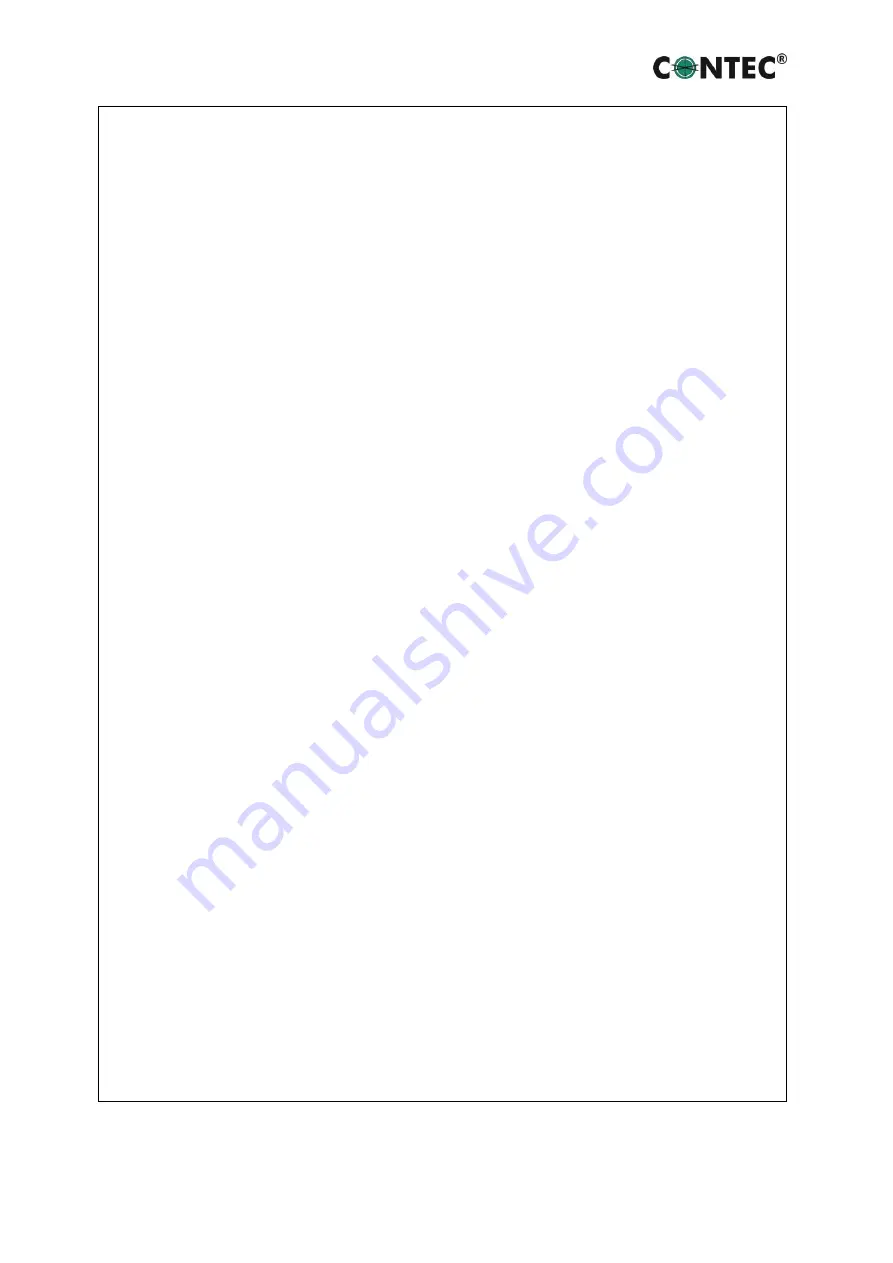
Manual MODUL 200
®
- 7 -
CONTEC
Maschinenbau
& Entwicklungstechnik GmbH
© CONTEC
®
2016
Hauptstrasse 146, 57518 Alsdorf (Sieg) / Germany
Tel: +49 (0) 2741 9344-0 Fax: +49 (0) 2741 9344-29
clockwise. Turn in a clockwise direction if the path is heavier on the right-hand side.
Reconnect the shot enter pipe with the clamps, connect the shot hose and try a short test run.
Repeat the adjustment if necessary, until the path is smooth, even and without variation.
5.2 Adjusting the height of the MODUL 200
®
There are three adjustable screws for changing the height of the MODUL 200
®
. By changing
the height, the gap between the floor and the magnetic frame is adjusted accordingly. For a
more effective performance, the smaller the gap between floor and machine, the better. (Less
wear & tear and loss of abrasive). However, a rough, uneven floor requires a slightly larger
gap than a smooth floor.
For changing the height of the front of the machine, the screw for adjusting is situated on the
upper end of the drive unit frame (Appendix diagram No. 227) under the control panel. For
the back of the machine, the two screws are situated on the rear wheel unit.
Unscrew the nuts of the screws – this applies to all screws. Turning the screws clockwise
lifts the machine, turning them anti clockwise lowers it. The gap between the magnetic frame
(Appendix diagram No. 207, 79 and 81) and the floor should be the same all over. For most
floors, this figure is between 5 mm and 10 mm.
On the front and sides of the magnetic frame are rubber strips (Appendix diagram No. 83)
which act as protective seals against escaping abrasive. If the height of the machine is
changed, the height of the rubber strips must also change accordingly. Slacken screws of the
brackets (Appendix diagram No. 85 and 86) which clamp the rubber strips and place them in
the desired position. They should always lie snug to the floor.
5.3 Wear & tear on the blast wheel and shot cage
The blast wheel (Appendix diagram No. 115) is a pure wear & tear part and must be checked
regularly. CONTEC
®
recommend a first check after 30 hours of blasting. The life of the
blast wheel depends on the application of the machine.
For example, a lot of wear & tear occurs when blasting soft concrete with a lot of surface fat.
Concrete dust is a very aggressive substance and increases wear & tear enormously. This
decreases when blasting steel or ceramic tiles. To give an accurate figure for the lifetime of
the wheel is therefore impossible. As a rough guide, this could be anywhere between 30 and
100 hours.
Take off the shot hose (Appendix diagram No. 125) in between the shot valve and the shot
enter pipe (Appendix diagram No. 123). Loosen the four nuts which secure the blast wheel
cover (Appendix diagram No. 117) to the machine. Remove the blast wheel cover carefully.
Between the blast wheel cover and the blast chamber is a rubber sealing which may, during
the process of operation stick to both sides. Pay special attention not to tear or rip it. Failure
to do so will result in damage to this sealing.
Now the blast wheel should be visible. In the middle of the blast wheel there is a hexagonal
shaped screw. Loosen the screw and remove the wheel from the blast chamber. Check the
wear & tear on the wheel. The thickness of the four blades should not be less than 5 mm. If
less, the blade could break and destroy the whole wheel.
Summary of Contents for CONTEC MODUL 200
Page 1: ...MODUL 200 Mobile Shotblaster Instruction manual...
Page 24: ......