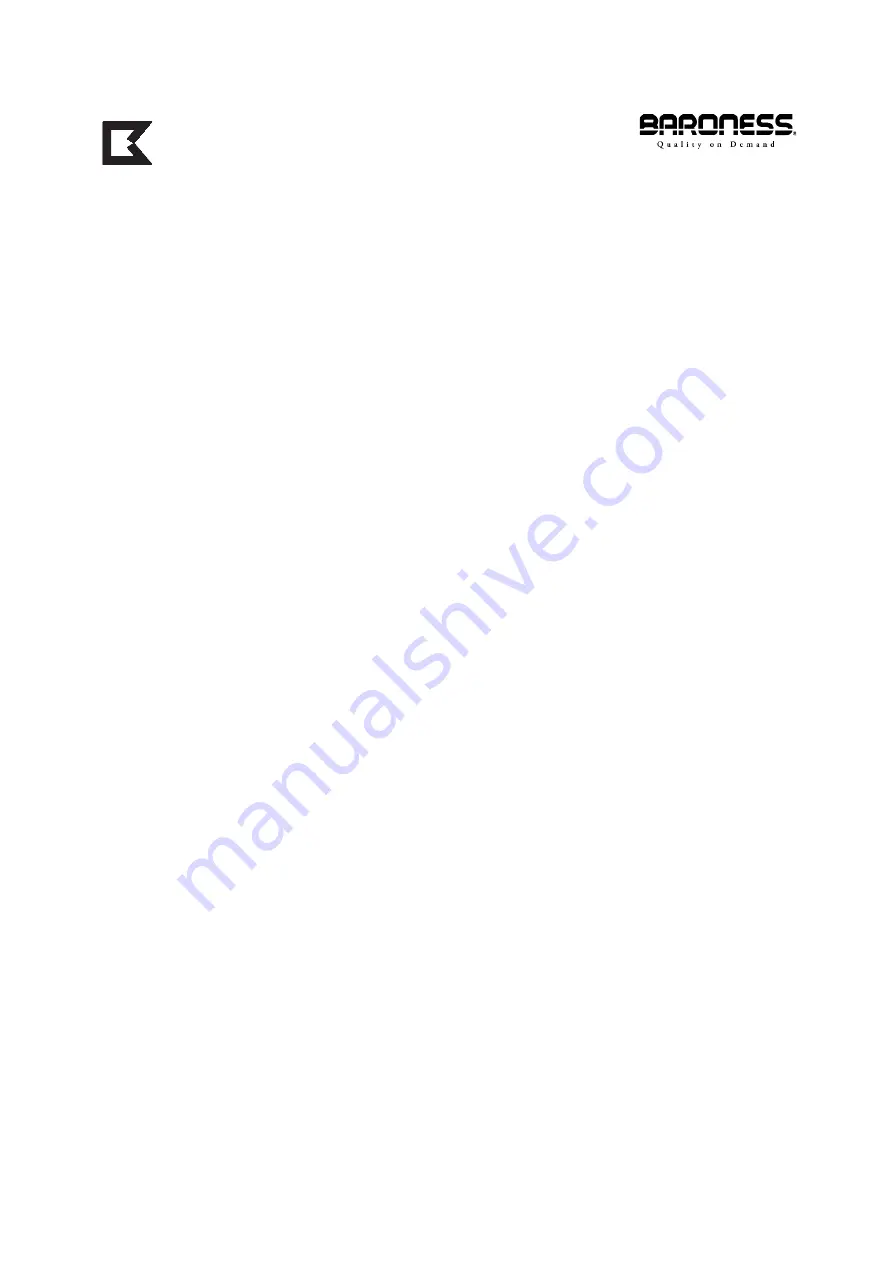
MANUFACTURER’S WARRANTY COVERAGE
:
OWNER’S WARRANTY RESPONSIBILITIES
:
As the equipment owner, you are responsible for performance of the required maintenance
listed in your owner’s operating manual
. KYOEISHA CO.,LTD recommends that you retain
all receipts covering maintenance on your equipment, but KYOEISHA CO.,LTD cannot
deny warranty coverage solely for the lack of receipts.
As the equipment owner, you should be aware that KYOEISHA CO.,LTD may deny you
warranty coverage if your equipment or a part has failed due to abuse, neglect, or improper
maintenance or unapproved modifications.
U.S. and CALIFORNIA EVAPORATIVE EMISSION CONTROL WARRANTY
STATEMENT
The United States Environmental Protection Agency (EPA), the California Air Resources
Board (CARB) and KYOEISHA CO.,LTD are pleased to explain the evaporative emission
control system’s warranty on your
2018 model year equipment. In California, new
equipment that use small off- engines must be designed, built and equipped to meet the
State’s stringent anti
-smog standards. KYOEISHA CO.,LTD must warrant the evaporative
emission control system on your equipment for the period listed below provided there has
been no abuse, neglect or improper maintenance of your equipment leading to the failure of
the evaporative emission control system.
Your evaporative emission control system may include parts such as: fuel tanks, fuel lines
(for liquid fuel and fuel vapors), fuel caps, canister, vapor hoses, clamps, connectors and
other associated emission-related components.
Where a warrantable condition exists, KYOEISHA CO.,LTD will repair your equipment at no
cost to you including diagnosis, parts and labor.
This evaporative emission control system is warranted for two years. If any evaporative
emission-related part on your equipment is defective, the part will be repaired or replaced
by KYOEISHA CO.,LTD. However as for the warranty of emission control system of the
engine,
refer to the operator’s manual of the engine
.
䠧䠵䠫䠡䠥䠯䠤䠝 䠟䠫
.,
䠨䠰䠠
Head Office : 1-26,Miyuki-cho,Toyokawa,Aichi-Pref., 442-8530 Japan.
Turf Care Machinery
Tel : 81-533-84-1095
Fax : 81-533-84-1225
㻱㼂㻞㻜㻝㻤㻭㻭㻜㻝㻙㻝
Summary of Contents for LM315GC
Page 6: ...LM315GC Introduction ...
Page 8: ...LM315GC Contents ...
Page 14: ...LM315GC Safety Page 1 6 Safe Operating Practices ...
Page 15: ...Waste Disposal Page 2 2 About the Waste disposal Page 2 2 Disposal LM315GC Disposal Page 2 1 ...
Page 82: ...LM315GC Maintenance Page 5 20 Long Term Storage ...