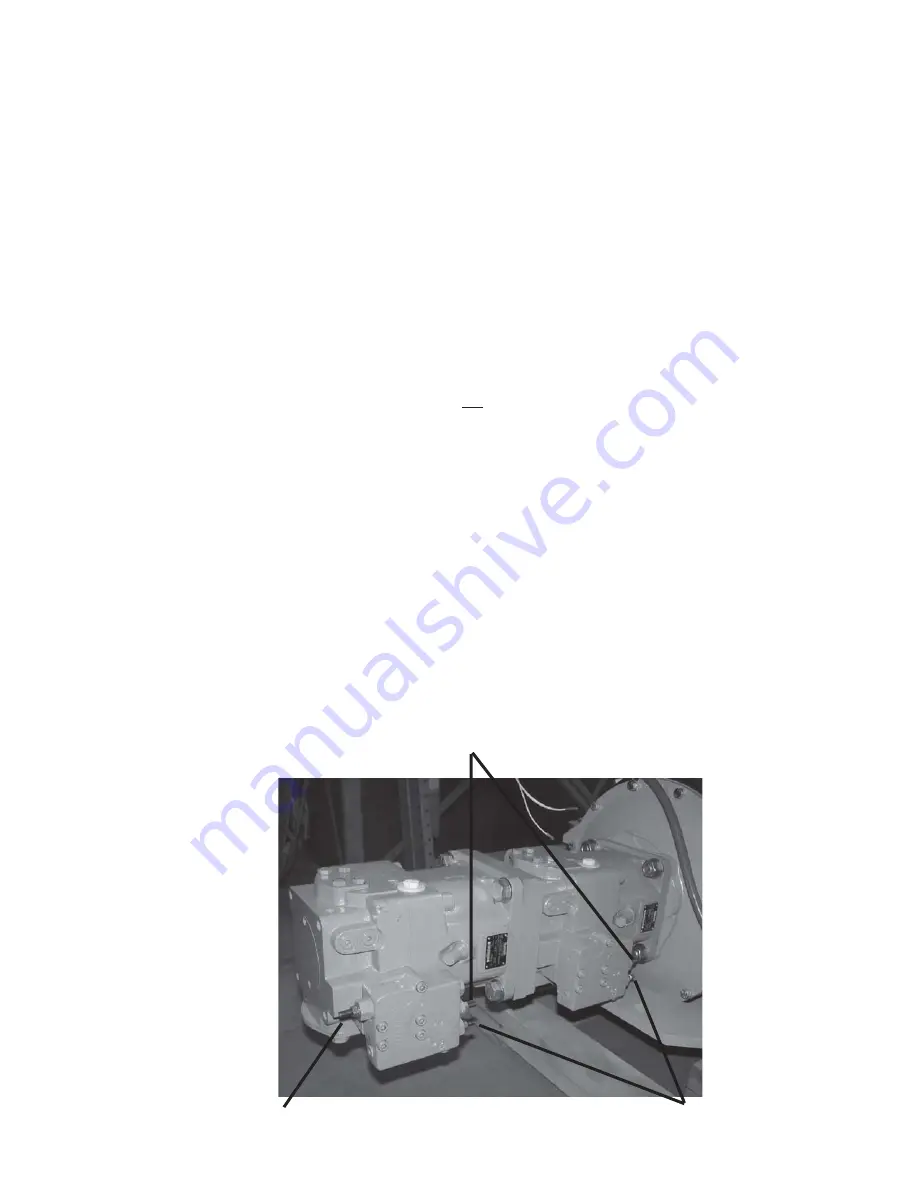
page 34
295 AC
800-00158
HYDRAULIC PRESSURE ADJ (AA11V-095)
(AA11V-095)
ADJUSTING WORKING PRESSURE (3600 PSI) AND STANDBY PRESSURE (425 PSI)
Note: When setting the working pressure and standby pressure on a double pump system the two pumps must be
set at equal pressures for optimal efficiency. The pressure readings from the pump output test port, or the
system pressure output test port is the highest pressure from the either pump. To set both pumps equally,
increase one of the blocks to the proper setting. Now increase the other block such that the gauge reads
above the proper setting to ensure it is the one giving the reading, now back down the pressure to the proper
reading.
If the proper setting can not be obtained this way the pumps will have to be isolated and adjusted
independently. Remove one pump at a time from the system by removing the load sense line from the
opposite pump to be adjusted. Tighten a JIC plug to the tee, LOOSELY screw on a cap to the pump to keep
dirt and dust out (if cap is to tight it will add to system pressure). Adjust pressures and reconnect hoses.
Repeat for other pump.
Standby pressure
Pump compensator
Torque Control
1. Install an electronic (digital) gauge on the system pressure test port (which is located on the main control
valve).
NOTE: When setting standby pressure, pressure will spike to approx. 3600 PSI before reading 425 PSI. This
will ruin a 1000 PSI gauge. Use an electronic (digital) gauge to check standby pressure.
2. With engine at low throttle, set standby pressure to 425 PSI (turn screw clockwise to increase,
counterclockwise to decrease).
3. To adjust pressure, loosen jam nut on pressure control block located on pump with 1/2" wrench. Adjust
pressure by turning screw in or out with a 5/32" allen wrench. Retighten jam nut prior to taking pressure reading.
4. Install a 5000 PSI gauge on the system pressure test port (located on the fire wall, or the PX port on the upper
control valve).
5. With engine at low throttle, bottom out the main boom (up) or stick boom (in or out) and set the system pressure
on the compensator screw to 3600 PSI (turn screw clockwise to increase, counterclockwise to decrease).
The torque control is factory set and generally will not require adjustment. Turning the screw in (clockwise) will
increase the load on the engine by holding the pumps on stroke at a higher pressure.
Summary of Contents for 295
Page 3: ...page3 295AC 800 00158 Introduction...
Page 16: ...page16 295AC 800 00158 Maintenance A PREVENTIVE MAINTENANCE Maintenance...
Page 26: ...page26 295AC 800 00158 Maintenance B HYDRAULIC SYSTEM...
Page 49: ...page49 295AC 800 00158 F12 SWING MOTOR MAINTENANCE CONTINUED...
Page 51: ...page51 295AC 800 00158 Maintenance C ELECTRICAL SYSTEM MAINTENANCE...
Page 65: ...page65 295AC 800 00158 Maintenance D POWER UNIT MAINTENANCE...
Page 75: ...page75 295AC 800 00158 Structural E STRUCTURAL MAINTENANCE...