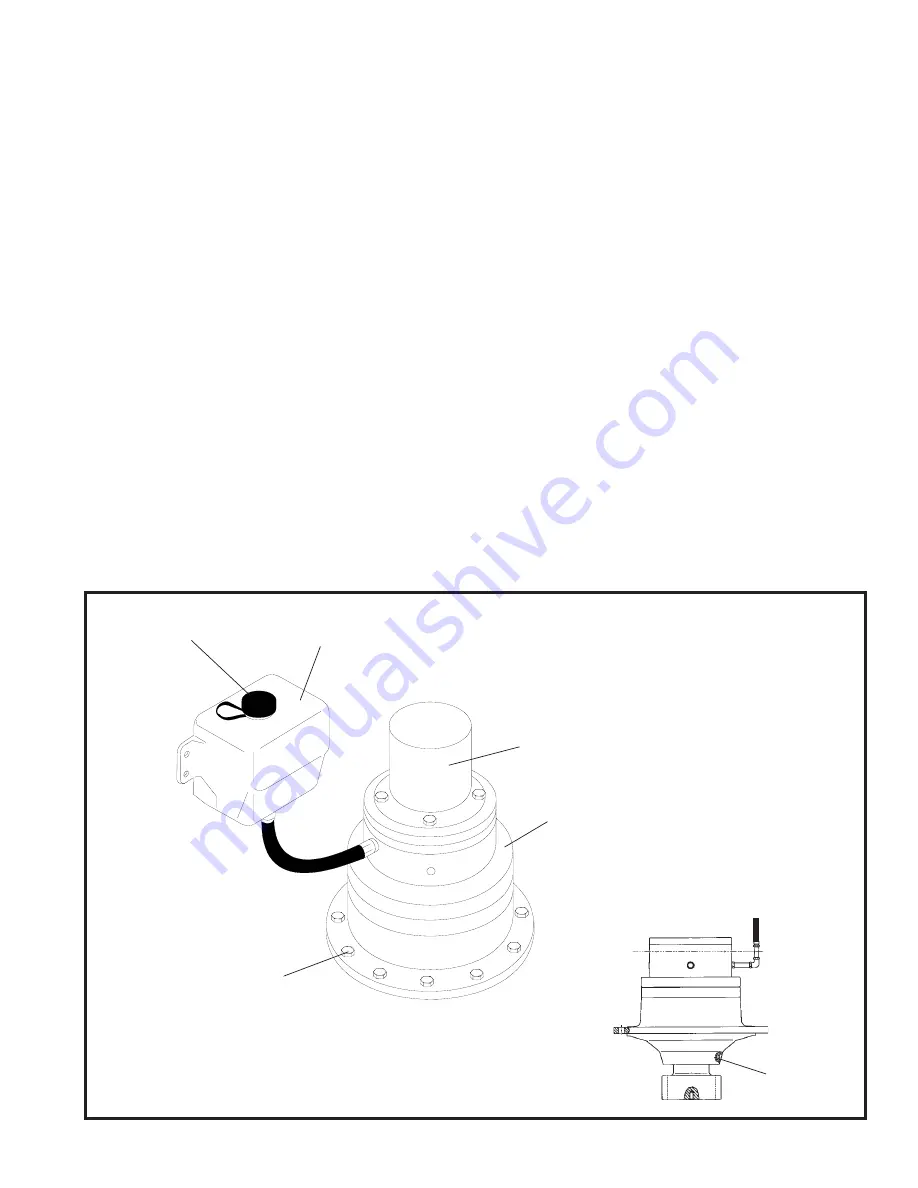
page 50
295 AC
800-00158
SWING MOTOR GEARBOX MAINTENANCE (G6/08)
RRT-G6/08 2-STAGE, VERTICALLY MOUNTED GEARBOX:
CHECKING FLUID LEVELS
A lube reservoir is connected to the gearbox with a hose. Check that the lube reservoir is at half full before operating.
FLUID TYPE
Use EP80-90 Gear Fluid in gearbox and lube reservoir.
FILLING THE GEARBOX WITH FLUID
To fill the gearbox with fluid, keep adding fluid to the lube reservoir until gearbox is full and lube reservoir remains at
half full. The filler cap has a built-in breather which allows air to escape as needed.
FLUID CAPACITIES
Fluid capacity of gearbox .................... 10.78 quarts.
Fluid capacity of lube reservoir ........... 2 quarts (keep at half full once gearbox is filled with fluid).
RECOMMENDED FLUID CHANGE INTERVALS
Fluid should be changed after the first 50 hours of machine operation, and every 400 hours after that. Drain plug is
located under gearbox mounting flange.
MOUNTING BOLT TORQUE
Gearbox mounting bolts should be torqued to 300 Ft. Lbs. of lubed torque. Use anti-seize lubricant 514-00700.
Figure 1
Swing Motor
Lube Reservoir
Drain Plug
Swing Motor Gearbox
Lube Reservoir
Filler Cap
Fluid Level
inside Gearbox
Swing Motor Gearbox
Mounting Bolts
Summary of Contents for 295
Page 3: ...page3 295AC 800 00158 Introduction...
Page 16: ...page16 295AC 800 00158 Maintenance A PREVENTIVE MAINTENANCE Maintenance...
Page 26: ...page26 295AC 800 00158 Maintenance B HYDRAULIC SYSTEM...
Page 49: ...page49 295AC 800 00158 F12 SWING MOTOR MAINTENANCE CONTINUED...
Page 51: ...page51 295AC 800 00158 Maintenance C ELECTRICAL SYSTEM MAINTENANCE...
Page 65: ...page65 295AC 800 00158 Maintenance D POWER UNIT MAINTENANCE...
Page 75: ...page75 295AC 800 00158 Structural E STRUCTURAL MAINTENANCE...