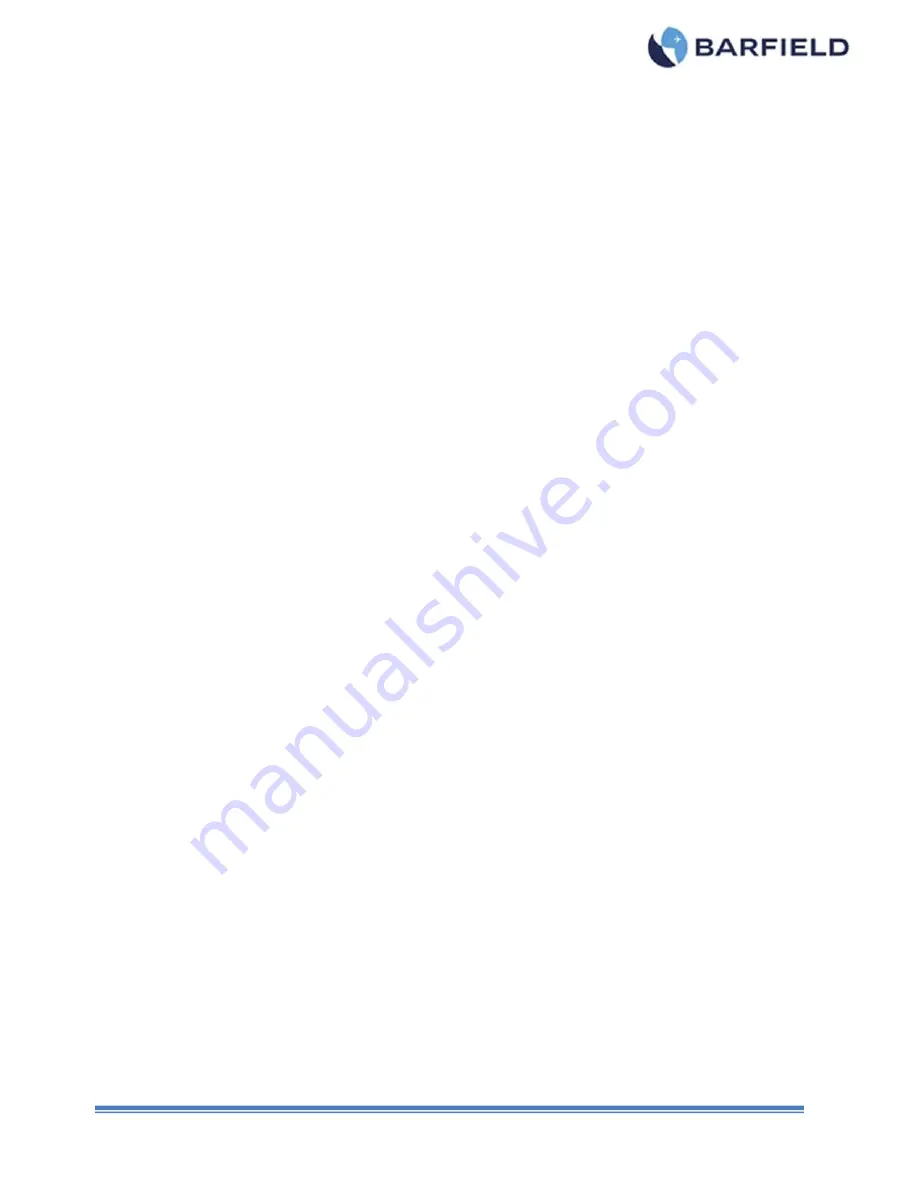
56-101-01175 Revision P Page | 8
Note
(*1)
:
ROC (with 125 cu in volume or less) default is 3,000 ft/min in Aeronautical mode.
Note
(*2)
:
RtCAS (with 75 cu in volume) default is 300 kts/min in Aeronautical mode.
Note
(*3)
:
Ps Channel: Specification based on (0.01% FS) accuracy based on calibrated
range of 3.0369 to 32.1480 inHg (± 0.003 inHg). The operating range is 55,000,
accuracy specification is declared up to 53,000 ft. The 53,000 ft accuracy tolerance
is slightly derated as compared with 52,500 ft and lower altitudes.
Note
(*4)
:
Pt Channel: Specification based on typical accuracy (0.06% FS). As a result of
the Qc Auto Zero, the Pt Channel accuracy is 0.005% FS rising to 0.06% FS at
650 kts. Refer to Note
(*6)
below for more details.
Note
(*5)
:
Barfield has confirmed “typ” stability performance to be the expected performance
that is experienced. If this level of accuracy performance is required, the customer
should retain the calibration certificate results over the past recent years to have
proof of the annual Incoming (As-received) results. This will provide the customer
with the performance level of accuracy the unit is providing, and they can confirm
it’s meeting their required performance requirements for the application.
•
If the Incoming (As-
received) performance is not meeting the customer’s
required accuracy, the recommended 12-month calibration interval should be
reduced to obtain the required accuracy required.
Note
(*6)
:
Specifications based on empirical results obtained from the evaluation of units
received back for annual recertification. However, if the application requires this
level of accuracy, historic proof of accuracy should be maintained. This can be
established by keeping a record of the annual calibration certifications, specifically
the Incoming (As-received) report, as this provides proof of accuracy and stability
maintained over the recommended 12-month annual calibration cycle.
•
Unlike most 3
rd
party calibration services, customer units calibrated and certified
by Barfield will receive an (1) Incoming (As-received) report and an (2) Outgoing
(As-left) calibration certification report. The incoming report provides the ability to
track and prove stability and accuracy. As an OEM, Barfield is the most qualified
to calibration, perform repairs, installs MODs, and provide firmware updates.
Note
(*7)
:
This tolerance represents the DPS1000 internal leak rate with no hoses attached to
the Static (Ps) or Pitot (Pt) ports. If configured with AN4 ports, the AN4 ports are
capped.
Important note regarding Leak Testing:
To obtain the true Leak Rate, the effects
of adiabatic must be considered, thus thermal equilibrium of the Static and Pitot
channel pneumatic may be required. This can be achieved by increasing the WAIT
time while performing Leak Testing using either of the two modes provided: (1)
traditional manual Leak Rate Timer mode or (2) while in automatic ATP Leak Test
mode. Thermal equilibrium occurs when the trapped air in the Static channel and
Pitot Channel are not increasing or decreasing in temperature. When air is trapped
in a sealed system the pressure increases or decreases when the gas “air”
expands or contracts because of thermal instability. This small increase or
decrease in pressure will have the appearance of a larger pneumatic leak than
exists. To measure the test set or test set and aircraft true leak rate, thermal
stability must be established before the leak measurement is performed. By
increasing the wait time from 1 minute to 5 minutes or longer, this will allow thermal
stability to be achieved resulting in more accurate true leak rate results.
Note:
Accuracy specifications are based on performing the 12-month recertification cycle
when connected to a leak tight system.
Note:
Specifications are subject to change without notice.