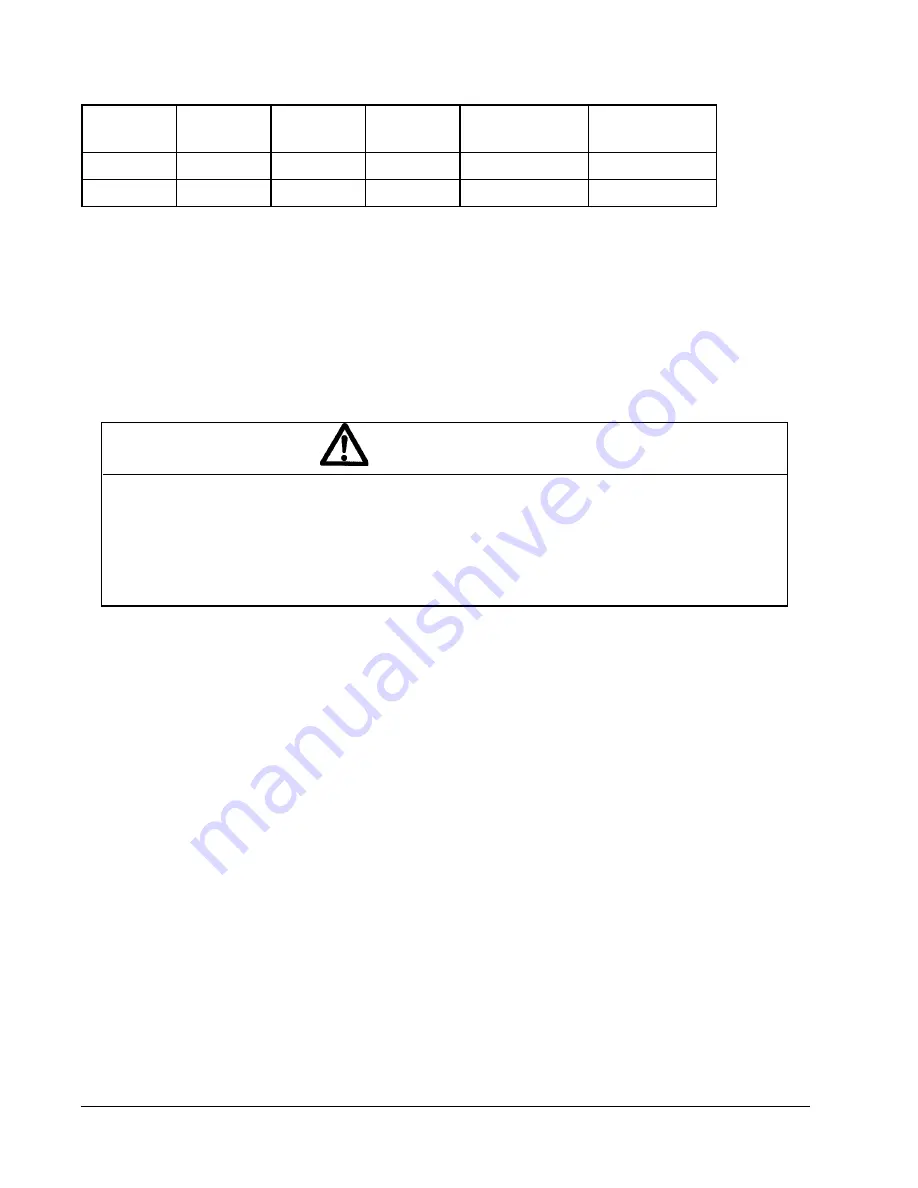
Manual 2100-592C
Page
6 of 69
1. IMPORTANT
The equipment covered in this manual is to be
installed by trained, experienced service and
installation technicians. All duct work or portions
thereof not in the conditioned space should be properly
insulated in order to both conserve energy and prevent
condensation or moisture damage.
2. APPLICATION
This is a fan-assisted forced air gas furnace with
electric air conditioning for outdoor installation. A
fan-assisted furnace is equipped with an integral
mechanical means to draw products of combustion
through the combustion chamber and heat exchanger.
The furnace installation must conform with local
building codes and ordinances or, in their absence,
with the National Fuel Gas Code ANSI Z223.1 or CAN/
CGA-B149.1, latest edition, and the National Electrical
Code ANSI/NFPA-7 or CSA C22.1, latest edition. It
is the personal responsibility and obligation of the
purchaser to contact a qualified installer to assure that
installation is adequate and is in conformance with
governing codes and ordinances.
3. DUCT WORK
The unit is designed for use with or without duct
work. See WARNING on Page 10. Flanges are
provided for attaching the supply and return ducts.
These instructions explain the recommended method
to install the air cooled self-contained electric air
conditioning and gas heating unit and the electrical
wiring connections and gas piping to the unit. The
refrigerant system is completely assembled and
charged. All internal wiring is complete.
These instructions and any instructions packaged with
any separate equipment required to make up the entire
heating/cooling system should be carefully read before
beginning the installation. Note particularly “Starting
Procedure” and any tags and/or labels attached to the
equipment.
All duct work, supply and return, must be properly
sized for the design airflow requirement of the
equipment. Air Conditioning Contractors of America
(ACCA) is an excellent guide to proper sizing.
Refer to tables later in this manual for maximum static
pressure available for duct design.
CAUTION
During the initial firing of the burners there will probably be some amount of smoke issued to the
circulating air stream as the result of residual oil burning off of the heat exchanger tubes. This oil
is required during the forming process of the stainless steel heat exchanger tubes to facilitate the
bending. OSHA or the National Toxicology Program does not list the oil as a carcinogen. In vapor
form this may be irritating to the eyes or could cause headaches. This is a one time occurrence, and
ventilation of the space may be required depending upon the space being conditioned.
Air Conditioning Module Options
STD – Standard equipment.
CCM Compressor control module has adjustable 30 second to 5 minute delay-on-break timer. On initial power up, or any
time the power is interrupted, the delay-on-make will be 2 minutes plus 10% of the delay-on-break setting. There is no
delay-on-make during routine operation of the unit. The module also provides the lockout feature (with 1 retry) for high
and/or low pressure controls, and a 2-minute timed bypass for low pressure control.
HPC High pressure control is auto reset. Always used with compressor control module (CCM) which is included. See Note
.
LPC Low pressure control is auto reset. Always used with compressor control module (CCM) which is included. See Note
.
LAC Low ambient control permits cooling operation down to 0°F.
CCM
HPC
LPC
LAC
Factory-Installed
Code
Field-Installed
Part
STD
STD
STD
X
N/A
STD
STD
STD
•
H
CMA-28
Summary of Contents for W24G2DA
Page 13: ...Manual 2100 592C Page 13 of 69 FIGURE 2A Mounting Instructions for W42G W48G and W60G...
Page 16: ...Manual 2100 592C Page 16 of 69 FIGURE 6 Common Wall Mounting Installations...
Page 26: ...Manual 2100 592C Page 26 of 69 FIGURE 12 Gas Pipe Connection W24G W36G W42G W60G...
Page 55: ...Manual 2100 592C Page 55 of 69 W24G2DA W48G2DA W60G2DA 230 208 60 1...
Page 57: ...Manual 2100 592C Page 57 of 69 W24G2DB W48G2DB W60G2DB 230 208 60 3...
Page 59: ...Manual 2100 592C Page 59 of 69 W24G2DC 460 60 3...
Page 61: ...Manual 2100 592C Page 61 of 69 W30G2DA W36G2DA W42G2DA 230 208 60 1...
Page 63: ...Manual 2100 592C Page 63 of 69 W30G2DB W36G2DB W42G2DB 230 208 60 3...
Page 65: ...Manual 2100 592C Page 65 of 69 W30G2DC W36G2DC W42G2DC 460 60 3...
Page 69: ...Manual 2100 592C Page 69 of 69 W48G2DC W60G2DC 460 60 3...