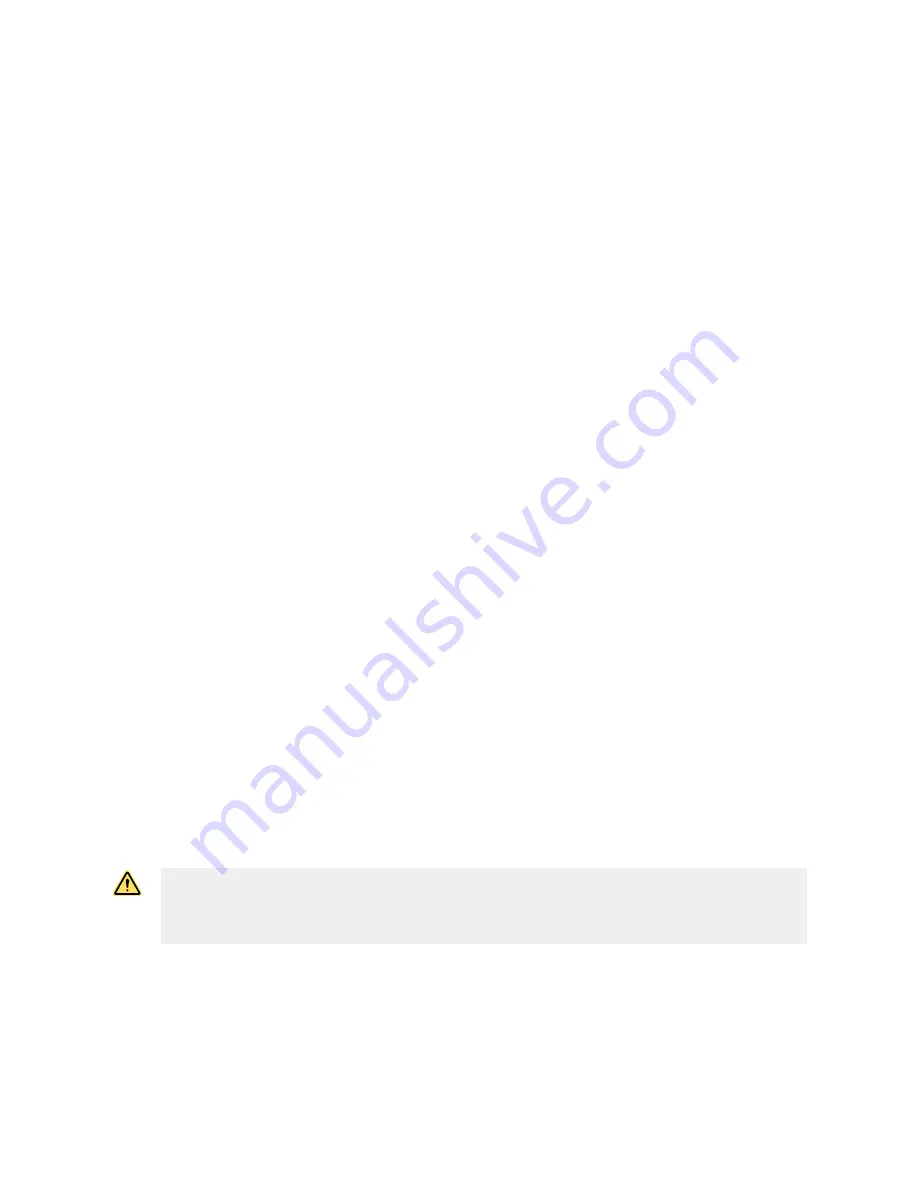
• Using
positive-opening
or direct-drive components, installed and mounted in a
positive
mode
4.4.3 Machine Primary Control Elements and EDM Input
Each of the two Machine Primary Control Elements (MPCE1 and MPCE2) must be capable of immediately stopping the dangerous
machine
motion,
irrespective
of the state of the other. These two channels of machine control need not be
identical,
but the stop
time
performance of the machine (Ts, used to calculate the safety distance, see
the Safety Distance (Minimum Distance)
11) must take into account the slower of the two channels. Some machines
offer
only one Primary Control Element. For such machines,
it may be necessary to duplicate the circuit of the single MPCE, by adding a second. Refer to
Generic Wiring to FSDs (manual reset)
on
page 33 and
Generic Wiring — Interface Module (2-Channel EDM, Manual Reset)
on page 34, or consult the machine manufacturer
for
additional
information.
4.4.4 Manual Reset/Remote Test Input and EDM
A means is provided for the
connection
of an external remote test switch or contact (typically a normally open, held closed). Cycling this
switch “turns
Off”
both OSSD outputs.
A single input provides the means to reset the system from a latch or lockout
condition,
to externally test the light screen and its
interface, and to monitor external devices (EDM) for proper
operation.
If the System is in Run
condition
with outputs On,
operating
the
switch results in a test. If the System is Latched or Locked Out,
operating
the switch results in a reset. If this input is connected to 0V dc
or
left
floating,
the System goes to a lockout
condition
on power-up. (See
on page 38 for
clearing lockouts.)
Connect the receiver’s reset/test wire (pin 8) to the supply voltage (see
Generic Wiring to FSDs (manual reset)
on page 33 and
Wiring — Interface Module (2-Channel EDM, Manual Reset)
on page 34) via the reset switch. The switch should be a normally closed
(N.C.) reset switch, or contacts of the Machine Control Test circuit (typically a normally open contact held or energized closed), or the
monitoring contacts of the external device(s) being
verified.
One switch could be used for the Reset and Test
functions,
or they can be
separate switches. However, all switches should be mounted as
specified
on page 15).
Manual Reset/System Test Procedure
To operate the switch (and perform a manual reset or a system test), open the normally closed (N.C.) switch for a minimum of 1/4
second and then close it.
Manual Reset
From a Latched or Lockout
condition,
operating
the switch results in a manual reset. Safe work procedures must require that a start-up
procedure is followed and that the individual performing the reset of the guarding device
verifies
that the
entire
hazardous area is clear
of all personnel, before performing each reset. If any area can not be observed from the reset switch
location,
additional
supplementary
guarding must be used: at minimum, visual and audible warnings of machine start-up.
Resetting
a safe guarding device must not
initiate
hazardous
motion.
Remote (External) Test
When in RUN mode, opening this switch for more than 1/4 second will
initiate
a Test cycle that turns OFF the OSSD outputs and
generates an internal self-test.
•
Automatic
(Machine) Test: An external switch, typically a normally open contact that is held closed, is used to externally
generate a test cycle of the EZ-SCREEN Type 2 and its interface. Depending on the
application
this switch can be a limit-style
switch, a hard contact from a relay, or an output from the machine control logic.
• Manual Test: A normally closed (N.C.) momentary type switch used for manual reset can also be used to manually
initiate
a test
cycle. This remote Test input may be useful for EZ-SCREEN Type 2 System setup and to verify machine control circuit
operation.
WARNING: Test
Function
A machine or
automatic
test of the EZ-SCREEN Type 2 and its interface may be required as determined by a risk
assessment and appropriate standard (for example, ISO 14121 and EN ISO 13849-1). Failure to test the
safeguarding
function
at appropriate intervals may lead to the loss of the safety
function.
External Device Monitoring Hookup
It is strongly recommended that one normally closed and one normally open, forced-guided monitoring contact of each FSD and MPCE
be connected to the Monitoring circuit (see
Generic Wiring to FSDs (manual reset)
on page 33 and
Generic Wiring — Interface Module
on page 34). If this is done, proper
operation
of the MPCEs will be
verified.
Receiver quick disconnect pin 8 provides
connection
for external device monitoring. External Device Monitoring (EDM) must be wired in
one of two
configurations:
Power Monitoring or No EDM.
EZ-SCREEN
®
Type 2 Light Screen
www.bannerengineering.com - Tel: 763.544.3164
31