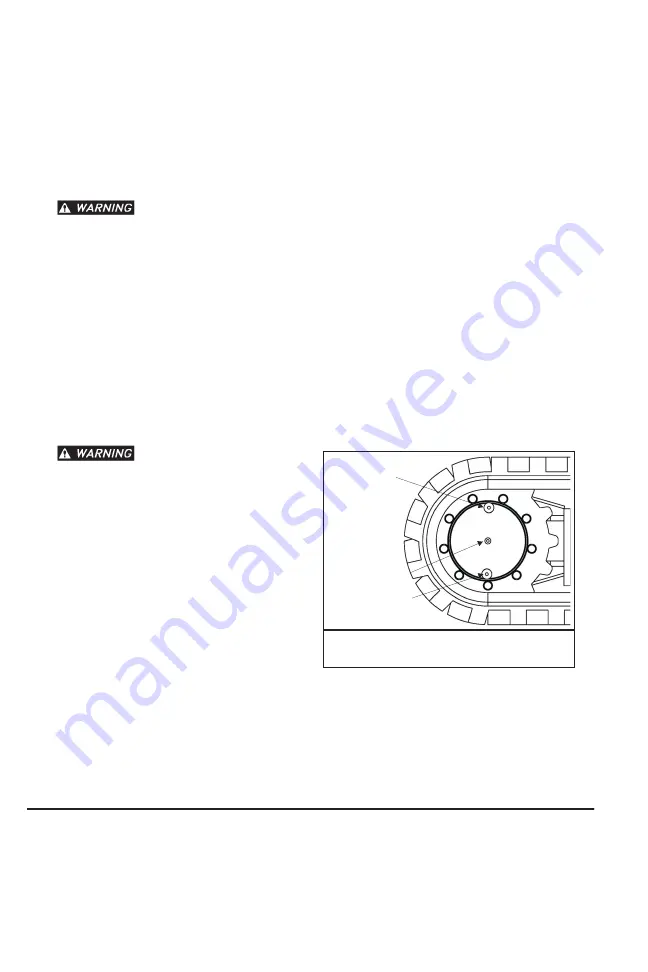
MAINTENANCE
Never at tempt to clean, ad just or lu bri cate a track unit while it is in
mo tion. Fail ure to heed may re sult in se ri ous per sonal in jury or death.
GENERAL
Proper tension of the rubber track is essential for maximum track and under carriage life and
will result in less down time. See ADJUSTMENTS on page 15.
Over tightening track can accelerate under carriage bearing wear and over stress and stretch
or crack the rubber track allowing contaminants to deteriorate the rubber compound and steel
reinforcing components.
Loose tracks can derail during turning and can also reduce machine stability during
operation. It is also possible for the drive sprocket to slip over the belt driving lugs causing
wear to the rubber track and possible failure. Derailing causes track damage.
Loose tracks will allow
excessive machine motion resulting in
decreased stability during operation.
Never repair with used or worn components
(idler, sprocket, rollers).
LUBRICATION
1. Different OEM brand hydraulic wheel
motor drives are used on track unit
assemblies, but the lubricating
procedure is similar. See figure 7.
2. Park the unit so the fill plug is at the top.
Some units will have a plug identified as
"FILL". If the plug is not identified, the
two opposite plugs are the same and either can be positioned at the top.
3. Check oil level at center check plug. Oil should seep out when plug is removed. Top off
if required.
4. Lubrication Specifications: Consult the wheel motor manufacturer's instructions for the
proper lubricant, quantity and operating temperature range.
Page 14
Maintenance
FIGURE 7.
TYPICAL MOTOR LUBRICATION
FILL PLUG
CHECK LEVEL PLUG
DRAIN PLUG