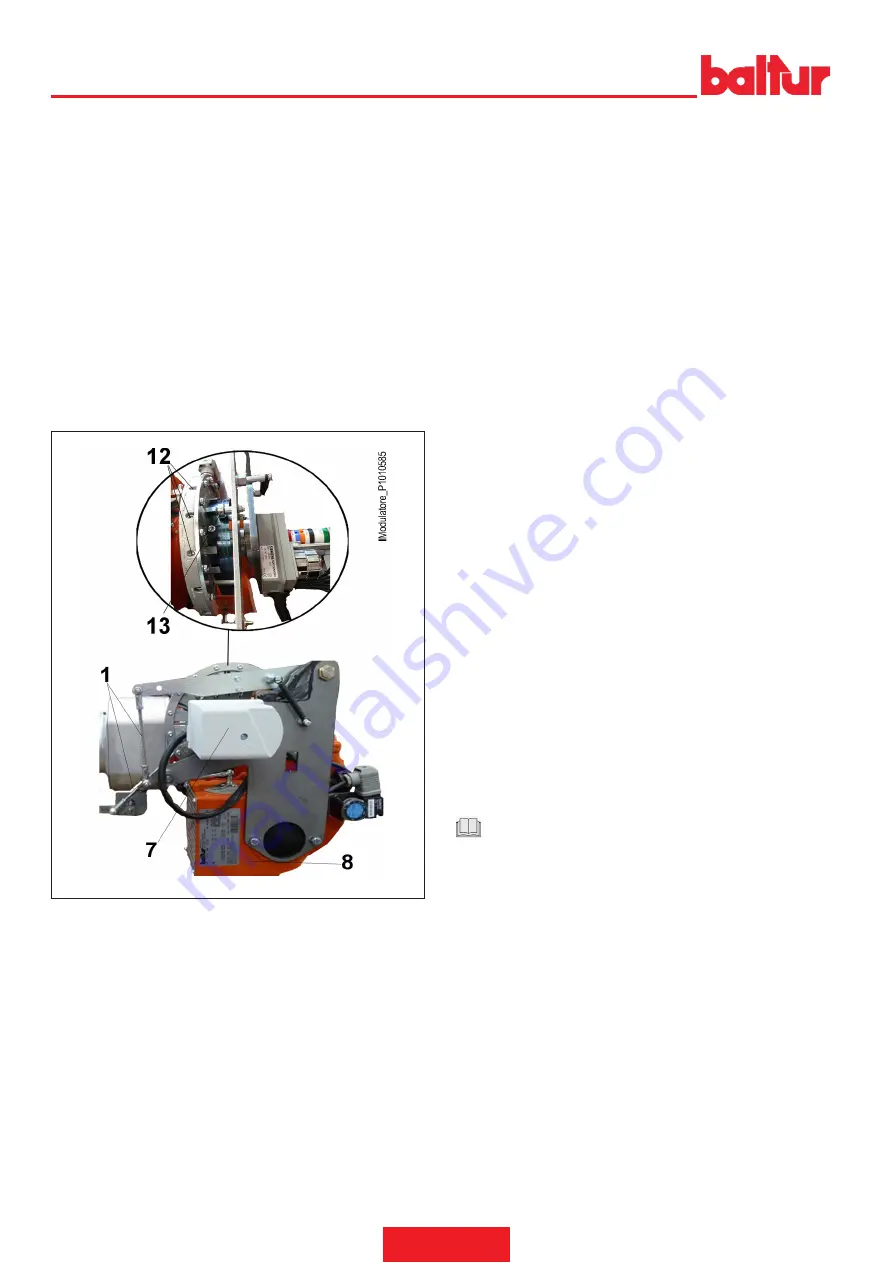
•
During the first ignition several “lock outs” may occur due to the
following reasons:
-
The gas piping has not been bled from air correctly and so
there is not enough gas to provide a stable flame.
-
The “lock out” with flame present may be caused by instability
in the ionisation area, due to an incorrect air/gas ratio.
•
Correct the air flow acting on the screw(s) (11), where the bearing
(12) is located:
-
in a clockwise direction the air flow increases
-
in an anticlockwise rotation: the air flow decreases.
•
It may occur that the ionisation current is disturbed by the discharge
current of the ignition transformer (the two currents have a common
path on the burner’s “mass”) so the burner locks out due to an
insufficient ionisation. Invert the supply (230V side) of the ignition
transformer.
•
This problem may also be caused by an insufficient “ground
connection” to the burner’s casing.
SECOND STAGE POWER REGULATION.
After first ignition adjustment, press the switch on the connector (4)
towards the maximum.
Check that the electric servomotor second
stage gas flow rate regulation cam is positioned at 120°.
•
To regulate the gas flow operate the valve pressure regulator.
Consult the instructions related to the installed gas valve model.
Avoid keeping the burner running if the heating capacity is greater
than the maximum amount allowed for the boiler, to avoid damaging
it.
•
For adjusting the air flow rate, operate on the screws (11), correct
the rotation angle of the air gate in the suitable position to guarantee
the right quantity for the power burned.
•
Check the combustion parameters with appropriate instruments
(C02 max= 10%, O2 min=3%, CO max=0,1%)
FIRST STAGE POWER REGULATION
After regulation of the burner in the second stage, return the burner
to the first stage. Press the switch on the connector (4) towards the
minimum without varying the adjustment of the gas valve already
performed.
•
Regulate the 1st stage gas flow rate to the required value using the
regulation cam for servomotor minimum output. (See Servomotor
cam regulation).
•
If necessary, correct the combustion air supply adjusting the
screw(s) (12).
•
Check the combustion parameters in the 1st stage with appropriate
instruments (C02 max= 10%, O2 min=3%, CO max=0,1%)
•
Check the efficiency of the thermostats or boiler pressure switches
(they should shut down the burner when triggered).
ADJUSTING THE FLOW RATE FOR IGNITION
•
Once regulation of minimum flame has been carried out, the burner
needs to be switched off and check that ignition occurs properly.
If necessary, it is possible to optimise burner regulation during
ignition, proceeding as follows:
-
Regulate the gas flow rate upon ignition, using the cam IV (see
Servomotor cam regulation). It is usually advisable to set cam
IV at a slightly higher angle than the first stage cam III.
•
Correct the air flow rate delivery using the screw(s) (12).
CAUTION / WARNINGS
After the regulation, check that the Cam V value is greater than
that of Cam IV (5°÷10°).
16 / 30
0006160096_202206
ENGLISH
Summary of Contents for TBG 35 MC
Page 2: ......
Page 31: ...SCHEMI ELETTRICI 29 30 0006160096_202206 ITALIANO...
Page 61: ...WIRING DIAGRAMS 29 30 0006160096_202206 ENGLISH...
Page 63: ......