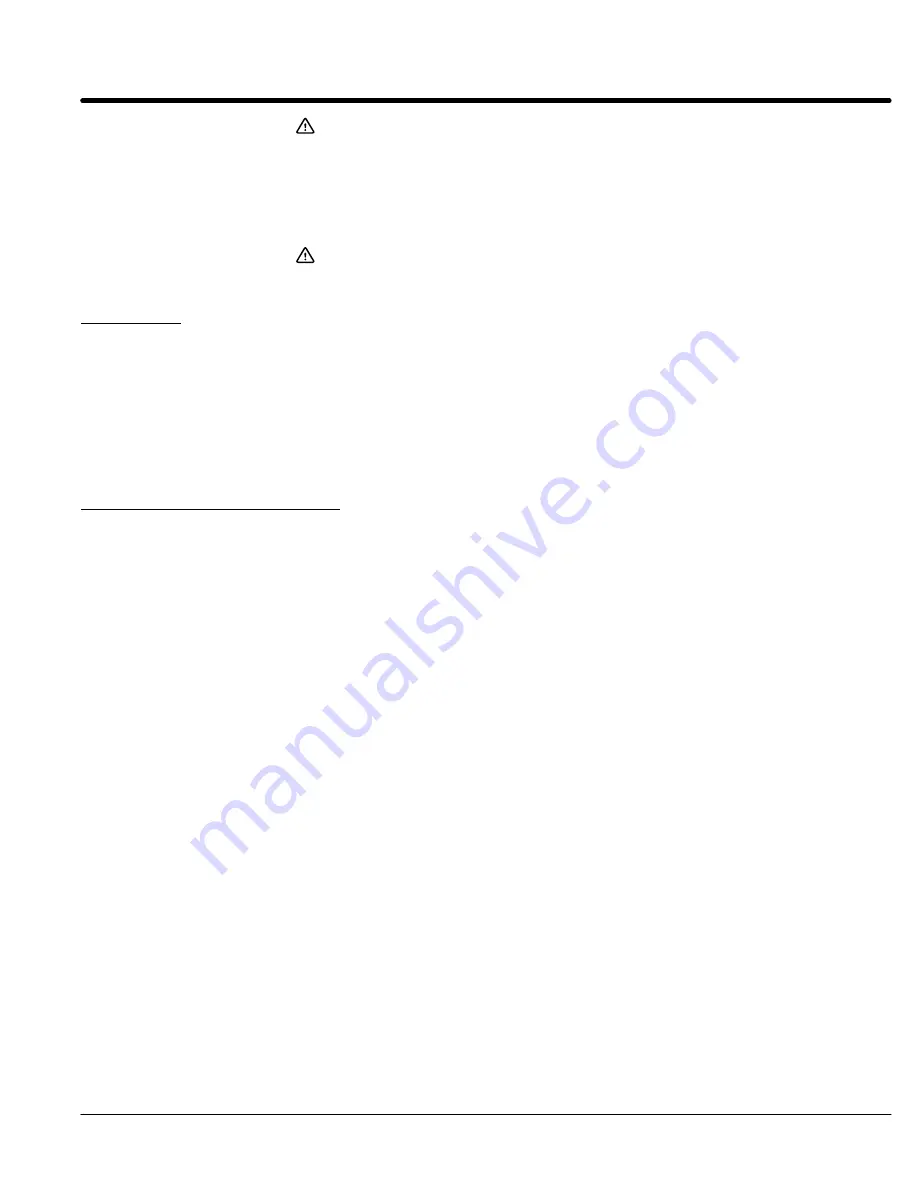
Troubleshooting and Maintenance 4-3
MN1269
WARNING: Do not touch any circuit board, power device or electrical
connection before you first ensure that power has been
disconnected and there is no high voltage present from this
equipment or other equipment to which it is connected. Electrical
shock can cause serious or fatal injury. Only qualified personnel
should attempt the start–up procedure or troubleshoot this
equipment.
WARNING: Do not remove cover for at least five (5) minutes after AC power is
disconnected to allow capacitors to discharge. Electrical shock can
cause serious or fatal injury.
Maintenance
The only periodic maintenance required on the servo control is an occasional inspection
for accumulated dust or dirt on the heat sinks and circuit boards. Heat sinks must be kept
clean for maximum cooling efficiency. Also, shop dust in some environments tends to be
electrically conductive and can cause servo control malfunction.
1.
If cleaning is needed, carefully vacuum loose dirt or use dry compressed air.
2.
Remove power and ensure that bus capacitor voltage has bled down before
checking connections.
3.
Periodically check all connections and fasteners for tightness.
Servo Control Card Replacement
1.
Remove power and ensure that the bus capacitor voltage has bled down.
DO NOT short capacitor with a screwdriver or clip lead.
2.
Measure capacitor voltage with a voltmeter or wait for 3 minutes for capacitor to
bleed off.
3.
Disconnect both of the module top edge connector by holding printed circuit
board while pulling connector away from board.
4.
Disconnect the signal–input connector in the same fashion.
5.
Loosen the chassis mounting screws (module heatsink brackets are slotted)
and slide module out from chassis.
Servo Systems Co. • 115 Main Road • P.O. Box 97 • Montville, NJ, 07045-0097
(973) 335-1007 • Toll Free: (800) 922-1103 • Fax: (973) 335-1661
www.servosystems.com