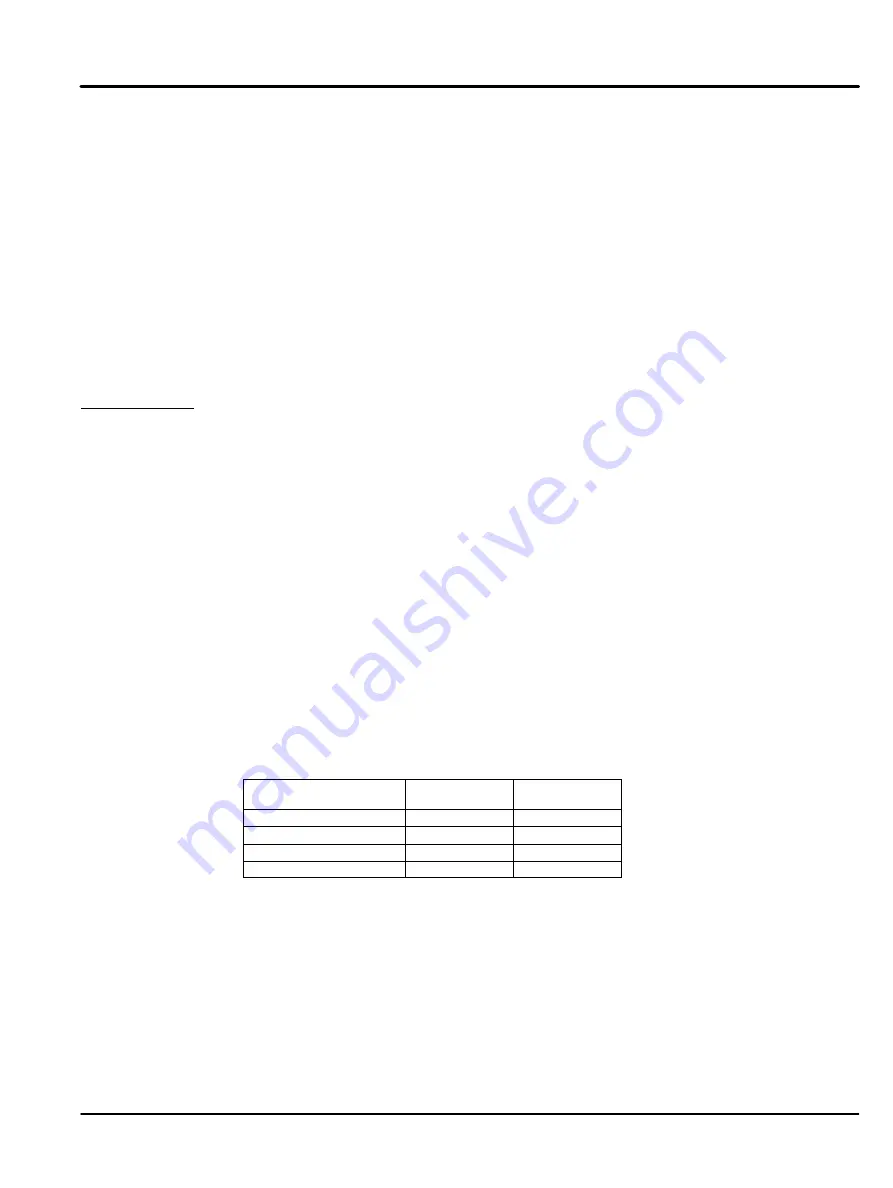
Operation 4-5
MN2408
No Load Test
To allow a timed No Load Test of the engine/generator set while using the AMF control
application, a digital input contact from an external timer must be programmed for NO LOAD Test
The sequence of operation for a No Load Test condition is as follows:
1.
With the utility supply normal and the generator stopped, a no load test sequence may
be initiated by closing an external exercise timer contact to the programmed digital
input for No Load Test.
2.
After the external exercise timer contact closes, the engine will start and come–up to
normal operating speed and voltage. The controller will issue an alarm of a No Load
Test condition. The connected transfer switch will remain on the utility and the
generator will not transfer on load. Note: should the utility supply fail, the generator will
automatically transfer on load.
3.
The engine will continue to run as long as the external exercise timer contact remains
closed.
4.
After the external exercise timer contact opens, the engine will continue to run for its
cool down time as programmed, then it will automatically stop.
Standard Faults
When a fault occurs, information about the fault is displayed. The engine controller has many
analog and digital inputs for monitoring and control operations. Three types of faults are used:
1.
Internal Faults are derived from a combination of digital and analog inputs.
2.
Digital Input Faults are initiated from external contact inputs.
3.
Analog Input Faults are initiated from external analog signal inputs.
Figure 4-3 shows how the controller inputs and outputs are organized.
A description of each is provided.
Internal Faults
Overspeed Shutdown
Overspeed Shutdown is initiated when the engine's speed has increased above the overspeed setpoint. The overspeed fault
circuit is internally programmed as a latching shutdown fault. The overspeed shutdown fault circuit is programmable for the
percentage of nominal engine speed (i.e. overspeed setpoint) and for the transient time delay period. The programming
prompts for overspeed are located in the main menu programming loop.
Loss of Speed
Loss Of Speed is initiated when the engine's speed sensing circuit does not detect a speed signal for a period more than 2
Alarm/Shutdown
seconds following a run signal. The loss of speed fault may be user programmed as a latching shutdown fault or alarm only.
The programming prompts for loss of speed are located in the main menu programming loop.
Overcrank Shutdown
Overcrank Shutdown is initiated when the engine fails to start after the selected crank time or number of crank cycles. The
overcrank fault circuit is internally programmed as a latching shutdown fault and is not user programmable.
Switch not in AUTO
Switch not in AUTO is initiated when the controller's operating mode switch is changed from the auto position to any other
position (ON the keypad). This fault is internally programmed as a non latching alarm. In the main programming loop, this
alarm may be user programmed to initiate the common fail output relay.
Digital Input Faults
Four digital faults are provided and these are user programmable. Each digital fault input circuit is activated by a remote
Digital Inputs (N/O or N/C)
sensing contact that is external to the controller. Each digital fault input circuit may be programmed with a unique fault label
description as stored in the controller's non-volatile memory.
Factory settings have four standard digital faults as follows:
Fault
Name
Fault
Action
Digital Inputs
Terminal #
Low Oil Pressure
Shutdown
1
High Engine Temperature
Shutdown
2
Battery Charger Input Fail
Alarm
3
Low Fuel Level
Alarm
4
The following is a list of all digital faults:
High Bearing Temp
Failed To Sync
Reverse Power
Bat Charger Input Fail
High Cooler Vibration
Low Fuel Press
Fail To Sync
Bat Chrg Trouble
High Engine Temp
Low Engine Temp
Vent Damper Fail
Bat Charger Fail
High Engine Vibration
Low Oil Pressure
Gen Breaker Open
DC Fail
High Fuel Level
Low Fuel Level
Ground Fault
Breaker Tripped
High Oil Level
Low Oil Level
No Load Test
Basin Rupture
High Oil Temp
Fuel Leak
ATS In Bypass
High Winding Temp
Low Fuel Press
Remote Emerg. Stop
*Highintkmanftemp
Low Coolant Level
Air Damper Tripped
Blank" (i.e. no text for unused inputs)
Summary of Contents for GLC30
Page 12: ...2 2 General Information MN2408...
Page 32: ...2 22 General Information MN2408...
Page 42: ...3 10 Receiving Installation MN2408 Figure 3 4 Three Phase WYE and DELTA Connections...
Page 52: ...4 6 Operation MN2408 Figure 4 3 Engine Controller Inputs Outputs...
Page 64: ...4 18 Operation MN2408 Figure 4 4 Configuration Data Sheet j j j j j j j j j...
Page 86: ...A 10 Series GLC MN2408 Figure A 2 Customer Interface Connection Diagram MEC20 MEC2...
Page 87: ...Series GLC A 11 MN2408 Figure A 3 Customer Interface w o Breaker Power Connection Diagram...
Page 88: ...A 12 Series GLC MN2408 Figure A 4 Single Phase w o Breaker Connection Diagram...
Page 89: ...Series GLC A 13 MN2408 Figure A 5 Single Phase One Breaker Connection Diagram...
Page 90: ...A 14 Series GLC MN2408 Figure A 6 Single Phase Two Breaker Connection Diagram...
Page 95: ...Series GLC A 19 MN2408 Figure A 11 Three Phase Connection Diagram...
Page 96: ...A 20 Series GLC MN2408 Figure A 12 Three Phase Connection Diagram with PMG...
Page 97: ...Series GLC A 21 MN2408 Figure A 13 Three Phase Connection Diagram Wire 1 0 and larger...
Page 104: ...A 28 Series GLC MN2408 Figure A 20 Control Box Connections with MEC2 Controller...
Page 105: ...Series GLC A 29 MN2408 Figure A 21 Engine Wiring Woodward 4 3L GM...
Page 106: ...A 30 Series GLC MN2408 Figure A 22 Engine Wiring Woodward 5 7L GM...
Page 107: ...Series GLC A 31 MN2408 Figure A 23 Engine Wiring Woodward 8 1L GM...
Page 108: ...A 32 Series GLC MN2408...