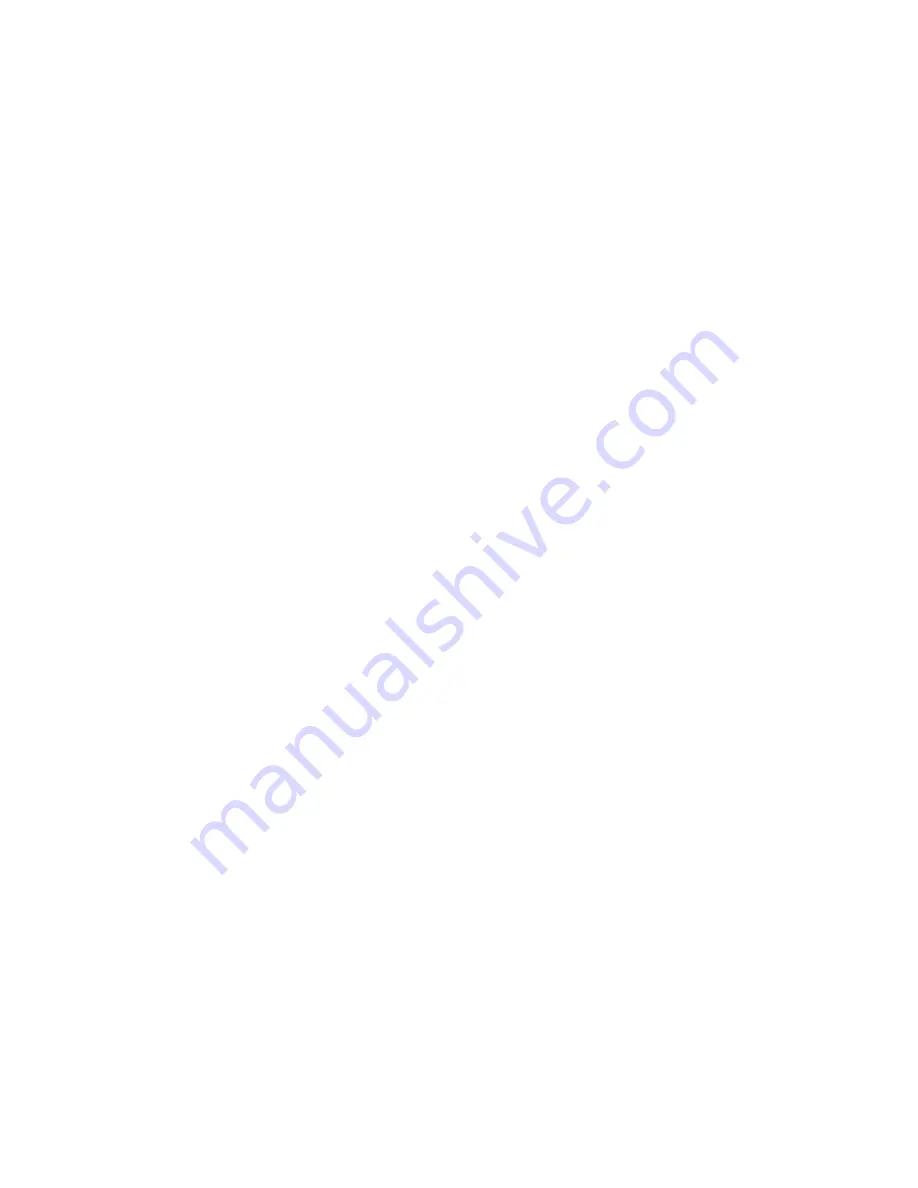
Document: 333D012G
5-18-2007
- 16 -
•
Ultraviolet (UV) Light On / Off [Optional] – A bulb, which produces light in the ultraviolet range, may be
used to help disinfect the work area. This switch controls the UV Light inside the work area if the UV Light
option is installed.
The viewscreen must be fully closed before the UV light will turn on.
The Fluorescent
Light and the UV Light are interlocked. When the viewscreen is closed, turning the UV Light On will
automatically turn the Fluorescent Light Off. Turning the Fluorescent Light On will automatically turn the
UV Light Off. The UV light will automatically shut off if the viewscreen is opened. A yellow indicator light
located below the switch will illuminate when the switch is on.
•
Fluorescent Light On / Off – This switch controls operation of the Fluorescent Light.
The cabinet blower
must be on for the Fluorescent Light to operate.
The Fluorescent Light and the UV Light are interlocked.
When the viewscreen is closed, turning the UV Light On will automatically turn the Fluorescent Light Off.
Turning the Fluorescent Light On will automatically turn the UV Light Off. A Blue indicator light located
below the switch will illuminate when the switch is on.
•
Duplex Outlets On / Off – This switch controls the duplex outlets in the work area. A Blue indicator light
located below the switch will illuminate when the switch is on.
•
Blower On / Off – This switch controls the power to the cabinet blower. A Green indicator light located
below the switch will illuminate when the switch is on.
•
Alarm reset / Sash level alarm – For normal operation, the viewscreen must be placed at the allowable
opening of 8” or 10” [203.2mm or 254mm]. The sash alarm will be activated whenever the viewscreen is
raised above or lowered below this level. To mute the audible alarm, press the alarm reset button. The
indicator light located below the switch will continue to flash. After five minutes, if the conditions persist, the
alarm will sound again to remind you to reposition the viewscreen to its proper level. You may press the
alarm reset switch again to mute the audible alarm for an additional five minutes.
Programmable Delay Off Time Function
The following procedure can be used to program a Delay Off time for UV, outlets, or fluorescent lights:
NOTE - The device to be programmed should be in the OFF condition before you start programming.
15 minute increment programming:
1.
Press and hold the pushbutton of the device you want to program.
2.
In about 3 seconds you will hear a short ‘beep’. This indicates that you have turned the device ON,
are in the programming mode for the device, and have programmed it to turn OFF in 15 minutes.
Release the pushbutton.
3.
Each subsequent press of the device pushbutton while in the programming mode will add 15 minutes
to the Delay Off time. (e.g. pressing the pushbutton 3 additional times would set the delay to 60
minutes, 15 min. initially plus 3 x 15 minutes additional delay times).
4.
The device control will remain in the programming mode for about 4 seconds if the pushbutton is not
pressed.
5.
Once the programming mode for the device has ended the device can be turned OFF normally, if
desired, by pressing the device pushbutton.
6.
The programmed device will turn OFF automatically at the end of the Delay Time.
7.
Each time a programmed device is turned off manually or automatically the programming is cleared
and must be reentered, if desired.
Summary of Contents for SterilGARD III Advance
Page 35: ...Document 333D012G 5 18 2007 34 Appendix...
Page 38: ...Document 333D012G 5 18 2007 37 Dimensional Drawing Standard Configuration SG403A...
Page 39: ...Document 333D012G 5 18 2007 38 Dimensional Drawing Standard Configuration SG603A...
Page 41: ...Document 333D012G 5 18 2007 40 Interior View Exterior View Cable port plug not shown...
Page 42: ...Document 333D012G 5 18 2007 41 Ladder Schematic SG403A...
Page 43: ...Document 333D012G 5 18 2007 42 Ladder Schematic SG603A...