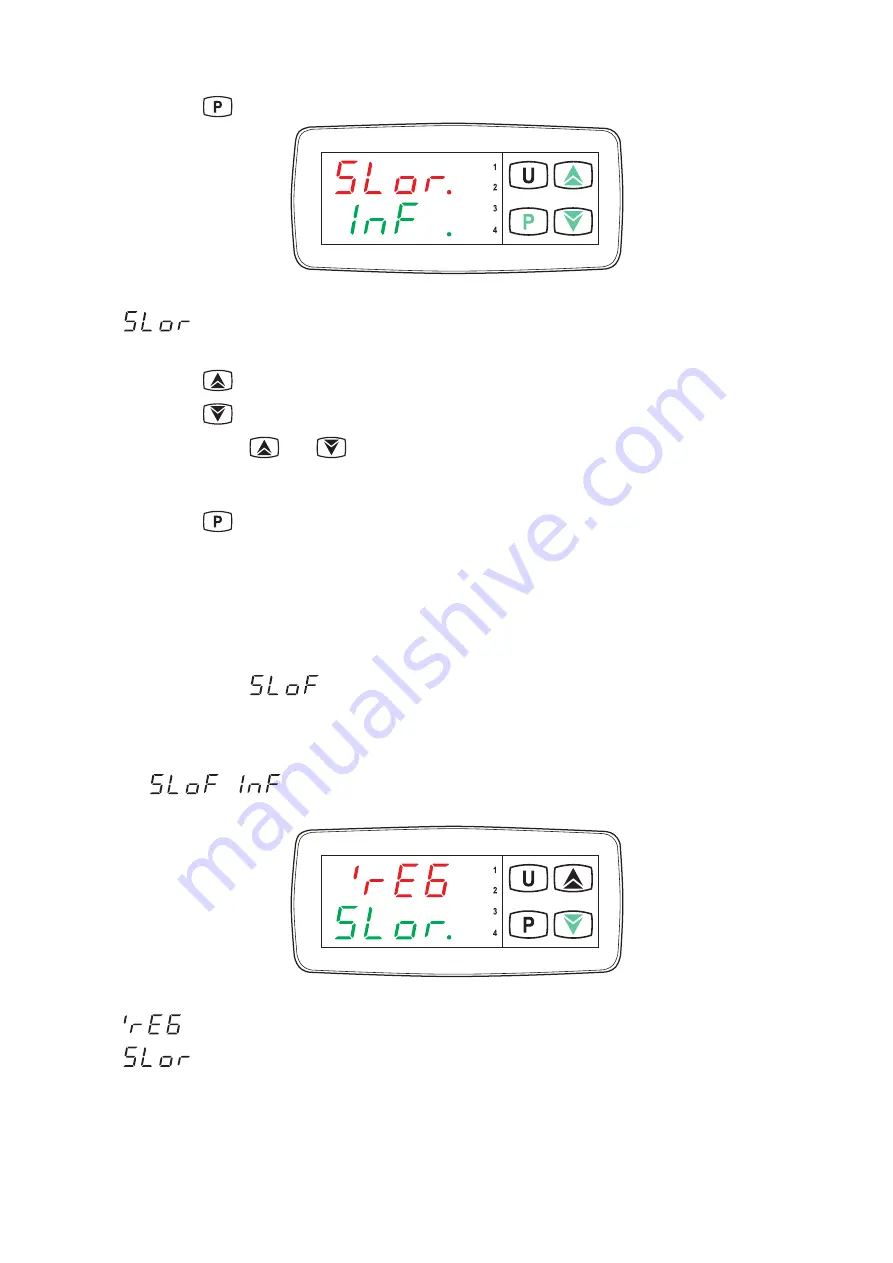
Copyright 2013 Baker Hughes Company.
English–Dry
TC / Liquid
TC Temperature Calibrators | 33
2. Press the
key.
Figure
41: Heating Gradient (SLor) Entry
flashes on the upper display.
The current heating gradient appears on the lower display.
3. Press the
key to increase the heating gradient.
4. Press the
key to decrease the heating gradient.
Note:
Press the
and
key to raise and lower the value by 0.1 respectively. If the keys
are held pressed for at least one second, the value increases or decreases quickly and after
two seconds even more quickly; this means the desired value can be reached rapidly.
5. Press the
key to confirm the heating gradient.
The display returns to the parameter level.
Note:
If no key is pressed for approximately 15
seconds, the controller automatically returns to
the calibration mode.
Note:
See Section
5.4.4.5 for details on new heating gradient parameter activation.
5.4.4.3 Setting the Cooling Gradient
The cooling gradient
is active if the reference temperature is higher than the set point
temperature.
The cooling gradient is adjustable from 99.99
°C/min to 0.00
°C/min. See Table
5 for the
maximum cooling capacity of the calibrator.
Note:
If
=
(in no function), cooling gradient control has been disabled.
1. Enter the gradient control parameter level. See Section
Figure
42: Parameter Level SLor (Heating Gradient)
appears on the upper display.
flashes on the lower display.