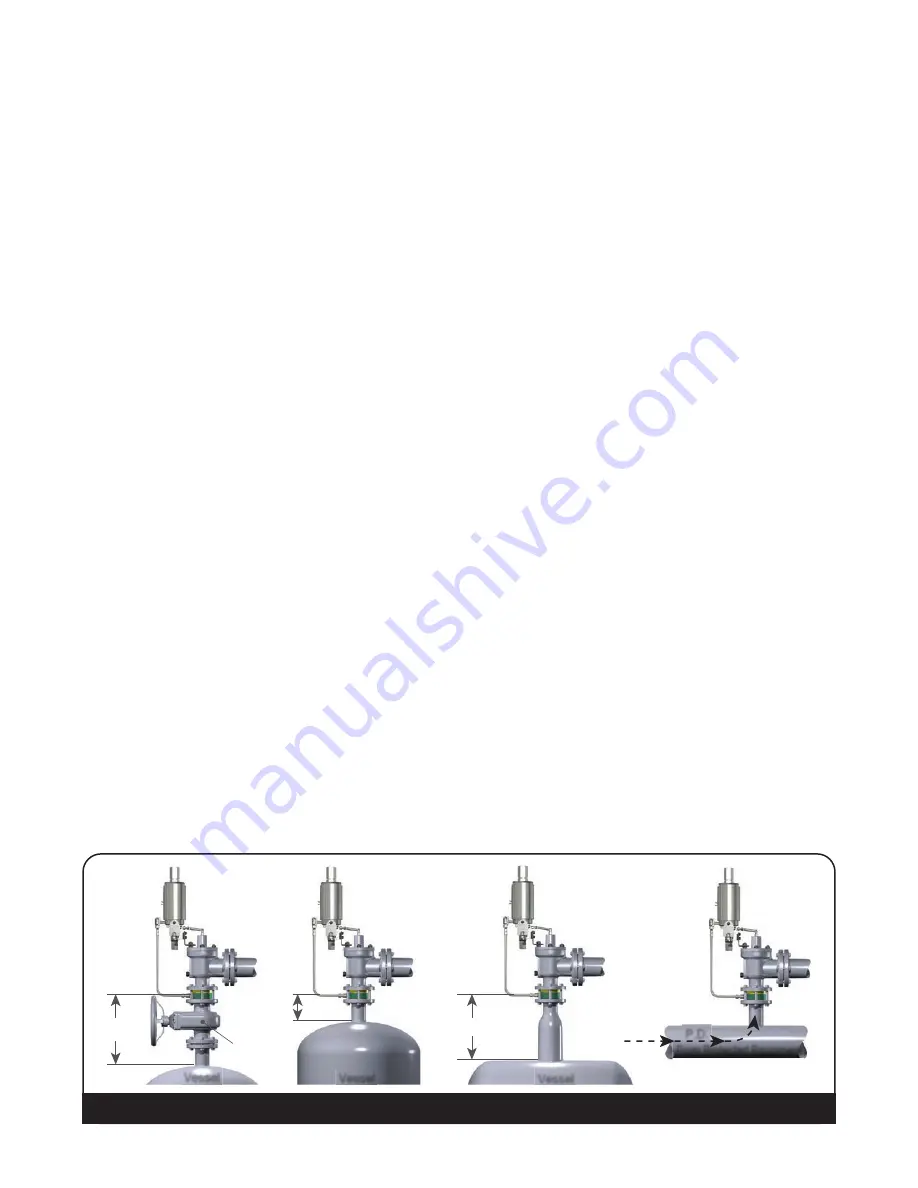
22 |
Baker Hughes
© 2020 Baker Hughes Company. All rights reserved.
XII. Recommended Installation Practices (Cont.)
B. Inlet Piping
The inlet piping (Figure 6) to the valve should be short
and direct from the vessel, or equipment, being protected.
The radius of the connection to the vessel should permit
smooth flow to the valve. Avoid sharp corners. If this is not
practical, then the inlet should be at least one additional
pipe diameter larger. The pressure drop from the vessel
to the valve shall not exceed 3% of valve set pressure
when the valve is allowing full capacity flow. The inlet
piping should never be smaller in diameter than the inlet
connection of the valve. Excessive pressure drop in gas,
vapor, or flashing- liquid service at the inlet of the POSRV
will cause extremely rapid opening and closing of the
valve, which is known as “chattering”. Chattering will result
in lowered capacity and damage to the seating surfaces.
The most desirable installation is that in which the nominal
size of the inlet piping is the same as, or greater than, the
nominal size of the valve inlet flange; and in which the
length does not exceed the face-to-face dimensions of a
standard tee of the required pressure class.
Do not locate POSRV inlets where excessive turbulence is
present, such as near elbows, tees, bends, orifice plates or
throttling valves.
Section VIII of the ASME Boiler and Pressure Vessel Code
requires the inlet connection design to consider stress
conditions during valve operation, caused by external
loading, vibration, and loads due to thermal expansion of
the discharge piping.
The determination of reaction forces during valve
discharge is the responsibility of the vessel and/or piping
designer. Baker Hughes publishes certain technical
information about reaction forces under various fluid flow
conditions, but assumes no liability for the calculations and
design of the inlet piping.
External loading, by poorly designed discharge piping and
support systems, and forced alignment of discharge piping
can cause excessive stresses and distortions in the valve
as well as the inlet piping. The stresses in the valve may
cause a malfunction or leak. Therefore, discharge piping
must be independently supported and carefully aligned.
Vibrations in the inlet piping systems may cause valve seat
leakage and/or fatigue failure. These vibrations may cause
the disc seat to slide back and forth across the nozzle seat
and may result in damage to the seating surfaces. Also,
vibration may cause separation of the seating surfaces
and premature wear to valve parts. High-frequency
vibrations are more detrimental to POSRV tightness than
low-frequency vibrations. This effect can be minimized
by providing a larger difference between the operating
pressure of the system and the set pressure of the valve,
particularly under high frequency conditions.
Temperature changes in the discharge piping may be
caused by fluid flowing from the discharge of the valve
or by prolonged exposure to the sun or heat radiated
from nearby equipment. A change in the discharge piping
temperature will cause a change in the length of the piping,
which may cause stresses to be transmitted to the POSRV
and its inlet piping. Proper support, anchoring or provision
for flexibility of the discharge piping can prevent stresses
caused by thermal changes. Do not use fixe supports.
C. Outlet Piping
Alignment of the internal parts of the POSRV is important
to ensure proper operation (see Figure 7). Although the
valve body will withstand a considerable mechanical
load, unsupported discharge piping consisting of more
than a companion flange long-radius elbow, and a short
vertical pipe is not recommended. Use spring supports to
connect outlet piping to prevent thermal expansion from
Vessel
Vessel
Vessel
Stop
Valve
The pressure
drop (P.D.)
between the
source of
pressure in the
protected
equipment and
the pressure relief
valve inlet is not
to exceed 3% of
the valve set
pressure.
P.D.
P.D.
From Protected Equipment
P.D.
P.D.
Figure 6: Pressure Drop on the Inlet Piping