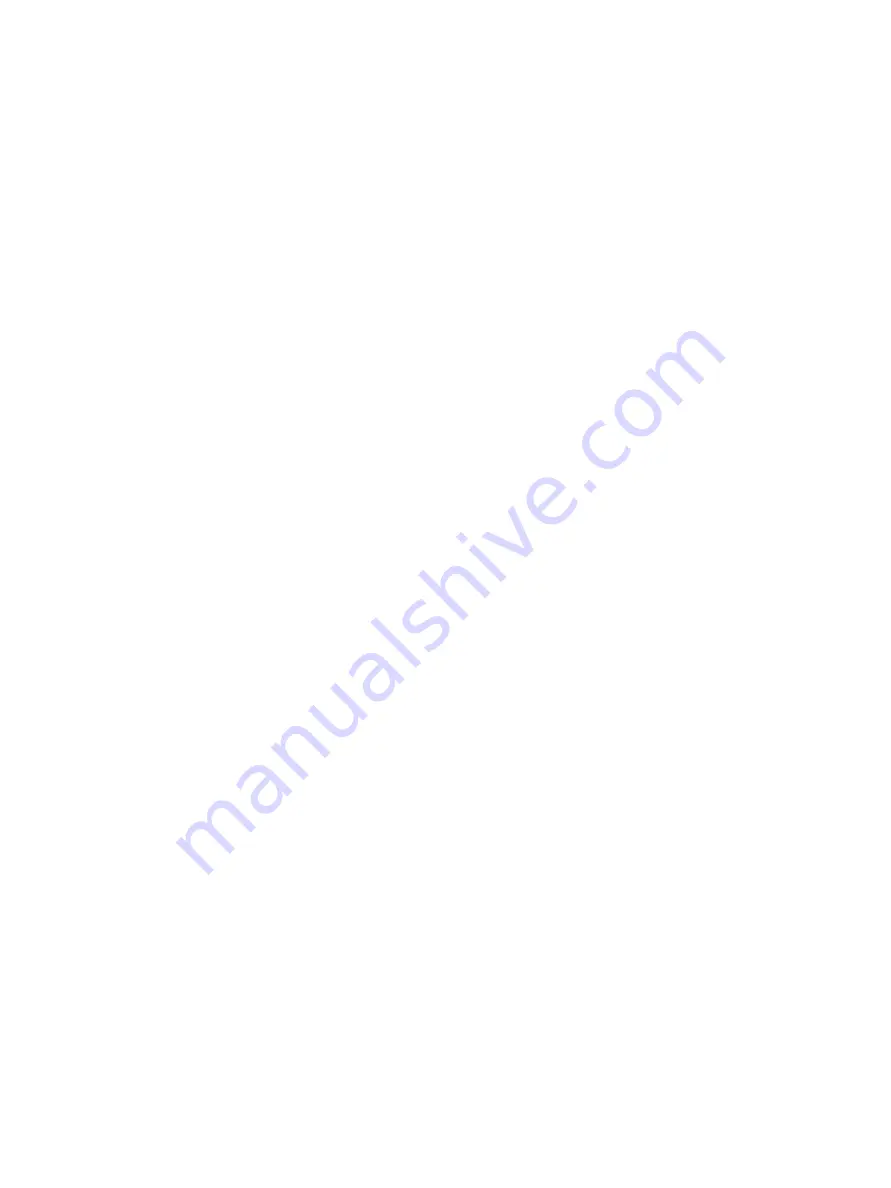
28 |
Baker Hughes
© 2020 Baker Hughes Company. All rights reserved.
gag (if used) and replace the sealing plug and gasket after ring
adjustment.
Section I valves, if possible, should have their blowdown
adjusted on the installation. If the original setting is unknown,
then use Table
11 as a guide. Further adjustment may be
necessary. For Section VIII valves, set the ring in the original
position or if unknown, use Table
11.
D. Seat Leakage
Seat Leakage is the escape of fluid with no valve lift.
Steam
Follow Safety Alerts on Section II.
Test seat leakage at 90 percent of the set pressure or 5 psig
(0.34 barg), whichever is greater. The ASME Codes require
that valves must be tight at operating pressures. After the valve
has been set at the required pressure and has reseated, yet
before it reaches operating pressure, seat should be tested for
leakage after the valve interior has dried. If there is no visual or
audible leakage, then pass a polished metal rod (temp. of rod
not to exceed 100°F or 38°C) slowly around the valve outlet
and observe if moisture forms on the rod. If the rod remains
dry, the valve is acceptable. If leakage is observed, the valve
must be reworked.
E. Recommended Back Pressure
Testing for Joint Leakage
After the valve has been set for the correct opening pressure,
valves with closed bonnets and caps are recommended to be
back pressure tested. Testing can be conducted by installing
cap with gasket and applying air or nitrogen to the base drain
connection or to the valve outlet. All other openings must be
sealed.
Test pressure should be at least 10 percent of the valve
set pressure or 30 psi (2.07 barg), whichever is greater. Air
nitrogen pressure would be held for 3 minutes before applying
leak detector solution to all connections (joints).
On bellows valves, also install a clean pipe plug in the bonnet
vent connection until it’s just short of finger tight. The purpose
is to obtain the smallest possible leak.
Examine the following for leakage during back pressure testing:
1. Nozzle/base joint
2. Adjusting ring pin seal
3. Base/bonnet joint
4. Bonnet/cap joint
5. If conventional valve, examine the “tight” bonnet vent plug.
6. If bellows valve, examine the “loose” bonnet vent plug.
Leakage is best detected by application of a commercial liquid
leak detector, i.e. Snoop
®
. Use of soap or household detergent
as a leak detector is not recommended as it may bridge small
leaks.
Repair of leaking valve joints may be attempted by tightening
the leaking joint while the valve is still on the stand. If this does
not stop the leak, tear down and inspect the leaking joint(s),
both metal surface and gasket.
If the valve internals have been disturbed, it is necessary to
retest to this manual, otherwise repeat the back pressure tests
as outlined above.
F. System Hydrostatic Testing
If the hydro pressure approaches set pressure, a test gag must
be used to keep the valve closed. Apply gag hand-tight. DO
NOT WRENCH TIGHTEN. Over gagging may bend the spindle
and damage the disc thermo lip. After hydrostatic testing the
gag must be removed and replaced by the sealing plug (gag
replacement plug) furnished for this purpose. Test gags and
sealing plugs are available from Baker Hughes.
For hydro pressure exceeding 1.5 times the set pressure
stamped on the name plate, Baker Hughes recommends that
the valve be removed and a blind flange be installed to avoid
internal damage to the valve.
When a P3 series valve, supplied with an open bonnet, is used
for outdoor service, Baker Hughes recommends that a Weather
Shield be used to protect against ice build-up and to help
stabilize the spring temperature.
XVI. Setting and Testing (Contd.)