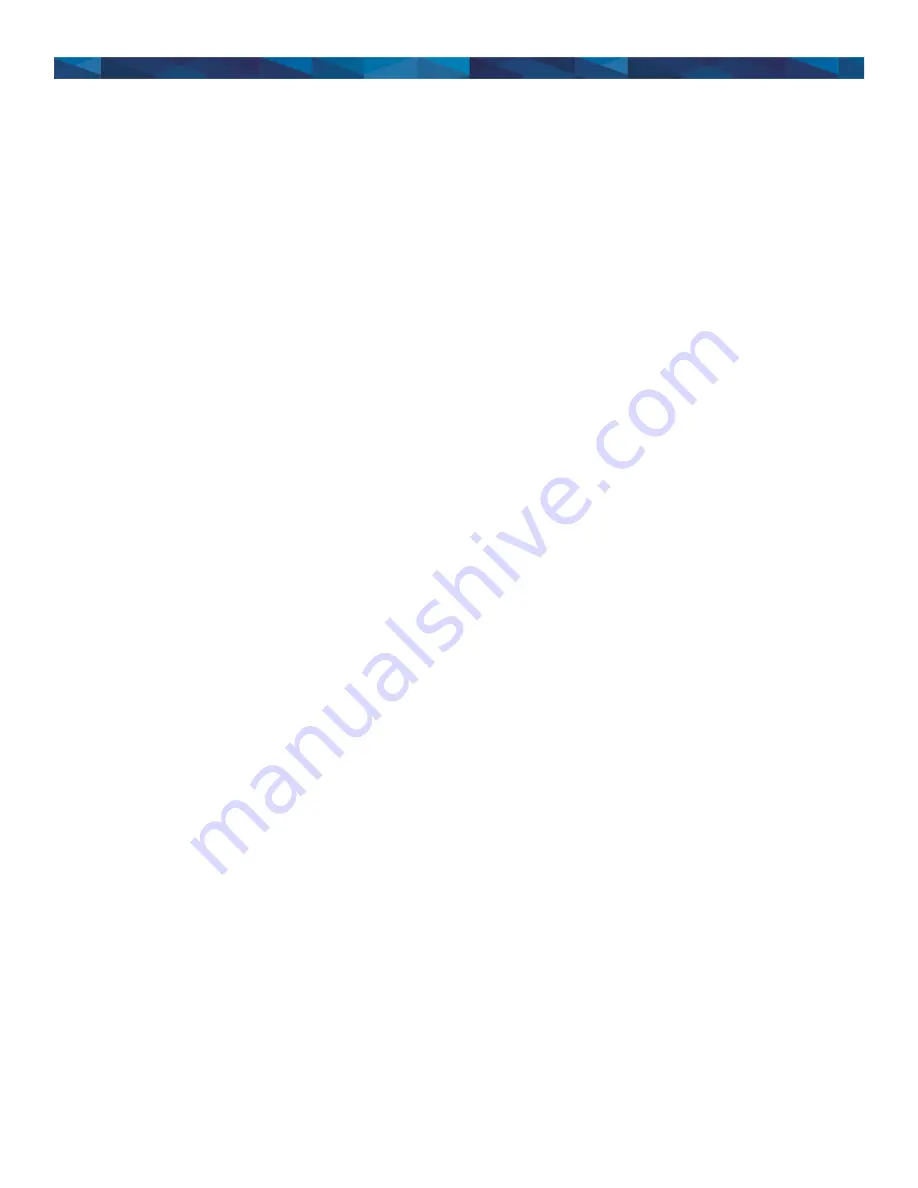
REV03026730010220
20
Maintenance
The system should be visually inspected and tested a minimum of every six (6) months according to the
procedure below during light duty cycles. Monthly inspections are recommended for systems that are being used
in excess of an average of eight (8) hours a day and five (5) days a week.
Preventative Maintenance
Prior to performing the maintenance procedure ensure that:
1.
The electrical sub-panel mounted main disconnect switch is operating properly.
2.
The user supplied remote circuit breaker is in the “OFF” position.
3.
All sources of power are isolated from the unit.
Note: Proceed only after this has been verified and properly tagged.
4.
Drain visible water and sediment from the primary and secondary filter (see Servicing Primary/Secondary Filters).
5.
Check system and all parts for corrosion and rust.
6.
Check mounting hardware – tighten as necessary.
7.
Check bolts on the pump/motor hardware for tightness, as pump/motor hardware can loosen after normal
operation for extended durations of time, due to vibration.
8.
The hardware uses lock nuts – check all bolts for secure nuts.
9.
Check all electrical terminals and connections for tightness.
10.
All motors are permanently lubricated and do not require any lubrication.
11.
Check all plumbing joints for leaks, tighten fittings and joints as necessary, and remove accumulated fuel in leak-
basin as necessary.
12.
Inspect all filter(s) and strainer.
Note: All filter elements should be replaced at least every six (6) months.
Servicing the Primary/Secondary Filters
Clogged filter elements restrict the flow of fuel, resulting in the system’s pressure gauge indicating a pressure spike. The
gauge is mounted between the pump and the fine filter. At a pressure of 22 PSI, the pump will automatically shut off and
generate a High Pressure Alarm. This signal indicates that it is time to change the filter element.
Changing the Filter Element(s):
1.
Turn the enclosure door panel selector switch to the “OFF” position – making sure the pump will not turn on.
2.
Close the inlet and outlet ball valves.
3.
Place an appropriate container underneath the filters.
4.
Open the drain valve at the bottom of the filter housing to allow all fluid to drain from the filters.
5.
Open the vent valve on the cover of the filter housing to allow the unit to vent thoroughly before opening.
6.
Loosen the 4 knobs on top of the filter housing.
7.
Remove the head gasket and expended filter cartridge and discard in accordance with local and national
regulations.
8.
Flush the interior of the housing with clean, processed, filtered product or a suitable solvent. A non-metallic bristle
brush may help to remove caked debris. Rinse the housing and unit cover with a clean solvent and dry with soft,
lint-free wiping cloths.
9.
Apply a film of lubricating oil to the gasket of the new filter.
10.
Insert a new filter cartridge into the housing. Position the housing with cartridge underneath the filter head, push,
and twist the cartridge into the head spigot. The head “conical spring” will seat/seal the cartridge in the housing.
11.
Rotate the filter housing into the collar bolts and tighten the knobs on top of the filter housing until secure.
12.
Close the drain valve at the bottom of the filter housing.
13.
Slowly open the inlet and outlet ball valves to allow the unit to fill completely.
Summary of Contents for STS 6030
Page 2: ...REV03016730010220 1 ...