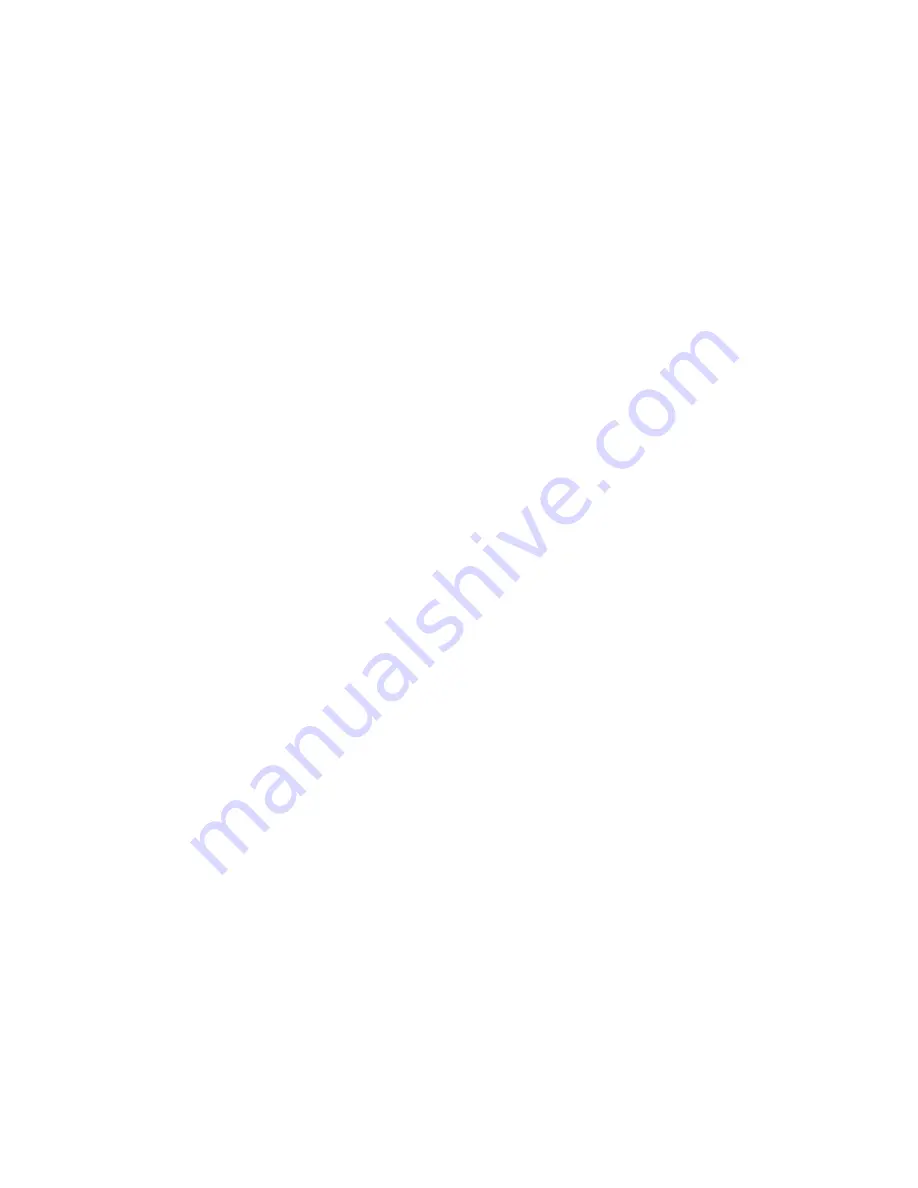
SERVICING PRIMARY FILTER
Set the telltale gauge pressure indicator (red pointer) to slightly above the black needle prior to
operation. The gauge will indicate maximum vacuum pressure during system operation.
Clogging filter elements restrict the flow of fuel and the system’s pressure gauge will indicate a pressure
drop. The gauge and differential pressure indicator are mounted on top of the primary filter head. At a
pressure drop of 25 PSI (red dial area of the gauge) the solenoid will automatically close and activate the
“HIGH PRESSURE ALARM” indicator light. The signal indicates that it is time to change the filter elements.
SERVICING AND BACK-FLUSHING PRIMARY FILTER:
1. Turn key switch to the “OFF” position – make sure pump will not turn on
2. Close the inlet and outlet ball valve
3. Place a fuel waste container below the drain valve on the bottom of the filter
4. Open the drain valve
5. Allow all fluid to drain from the filter
6. Open the vent valve on the cover of the housing ; allow the unit to thoroughly vent before
opening the cover
7. Loosen the 4 knobs attaching the head to the housing flange
8. Remove the head gasket and discard
9. Remove and discard the expended cartridge in a FIRE-SAFE place. In accordance with local and
national regulations.
10. Flush the interior of the housing with clean, processed, filtered product or a suitable solvent. A
nonmetallic bristle brush will help to remove caked-on debris. Rinse the housing and unit cover
with a clean solvent and dry with soft, lint-free wiping cloths.
11. Lightly lubricate new head gasket with Vaseline or Petroleum Jelly and position it on the head. If
Vaseline is not available lubricate the gasket with the fuel or oil it will be used in.
12. Insert a new cartridge into the housing. Position housing (with cartridge) underneath filter head.
Push/twist cartridge onto head spigot. The head “conical spring” will seat/seal the cartridge in the
housing.
13. “Rotate” housing onto the collar bolts, hand tighten knobs until head is “snug” to housing.
NOTE: A torque wrench is recommended. Tighten all collar bolts to 100 in lbs.
14. Close the drain valve on the bottom of the housing.
15. SLOWLY open the inlet and outlet valves; allow the unit to fill completely.
16. Leave the vent valve on top of the unit open; to allow entrapped air to escape while filling.
17. When a small amount of fluid flows from the vent, close it tightly.
18. During the initial filling and after the above maintenance, and while unit is in operation, examine
housing and all connections for leaks. Including head/flange junction.
19. Push the “ALARM RESET” button on the control panel to acknowledge the alarm and reset it
20. Return the pump selector key switch to “AUTO” or “RUN”
21. Check for leaks when re-starting and pressurizing the system. Your system is now ready to resume
normal operation