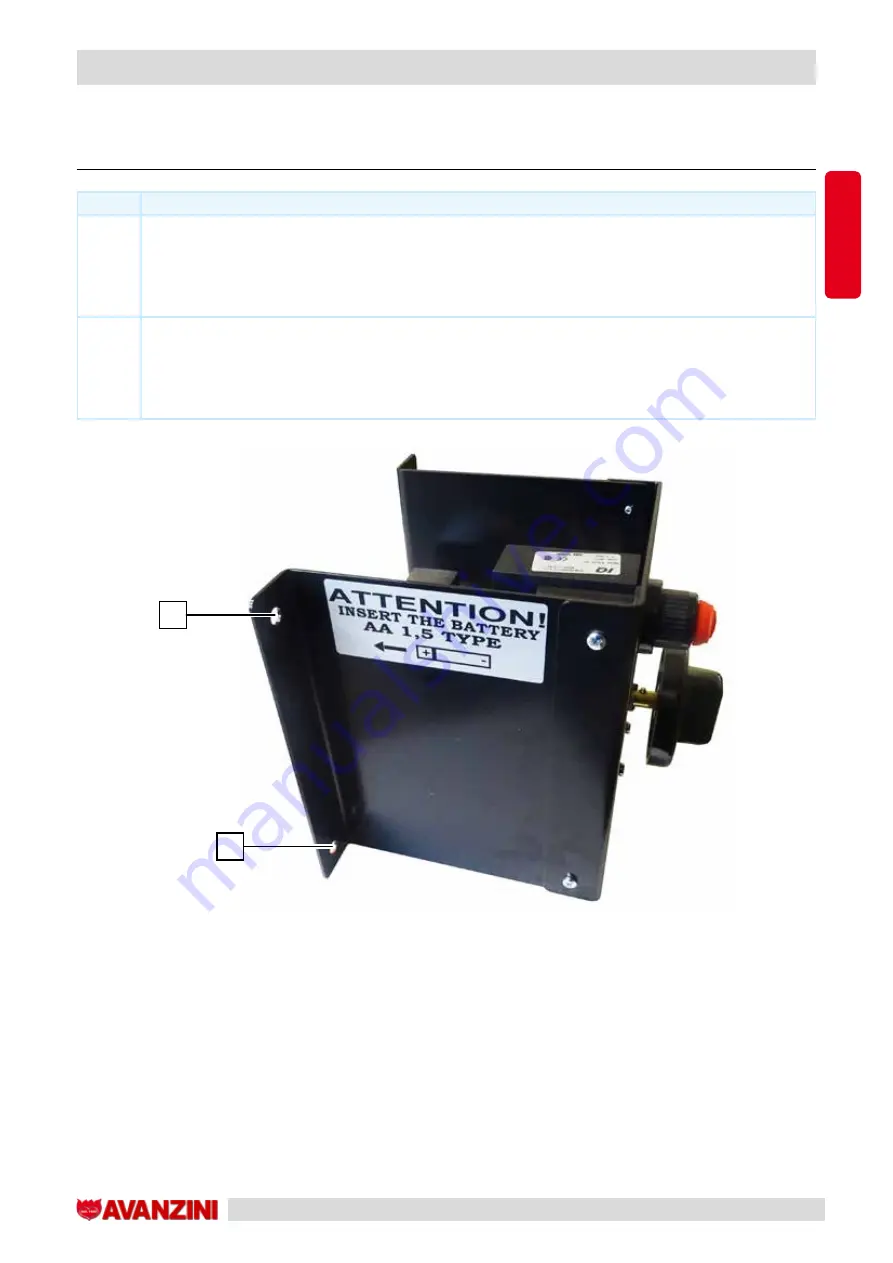
CHAPTER 5
Instructions, use and maintenance manual
D r a g o P 1 P L U S
Page 49
5.7.4. SECURING THE CONTROL PANEL WITH KNOB
STEP
ACTION
1
Identify the best position where to install the control panel (one ideal position is at the side of the
oven loading door, since it can be easily accessed by the operator yet it is protected against potential
collisions).
2
Secure the control panel using screws or plugs that are suitable for the surface in question in the 4
preset holes “
A
” (2 right and 2 left).
A
A