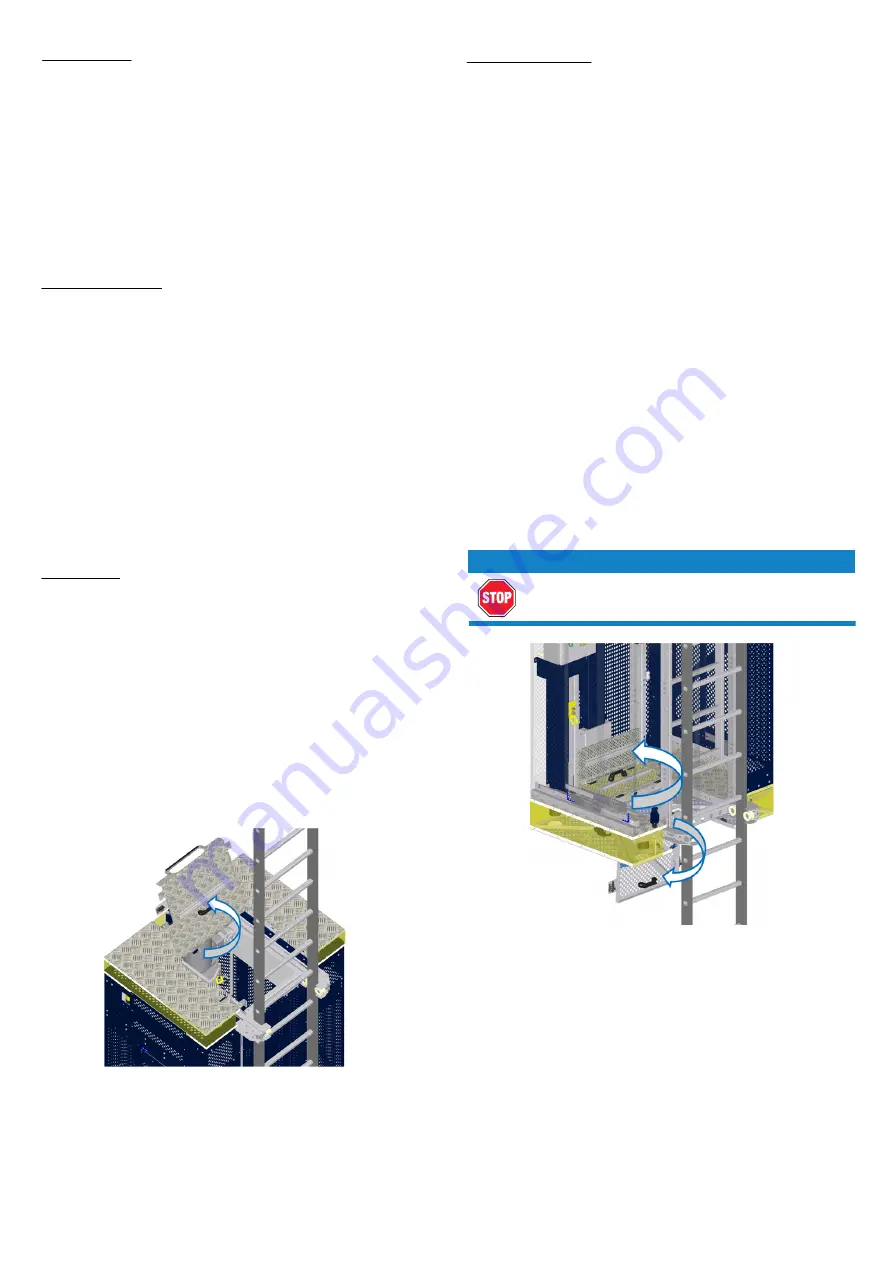
21
Normal use
During normal use with the service lift connected to the
electric grid, the sliding door is closed by pushing
th
e
actuator into the door guard locking switch. The
control is interrupted if the door is not closed correctly.
When the cabin is at a platform, the lift detection switch or
photoelectric sensor (optional features) is activated and
the sliding door can be opened. In the cabin there is a
handle to assist with opening the sliding door.
Inside the cabin there is a position platform indicator.
The green light is ON when the lift is at the platform.
Emergency use
During emergency use, for example during a power outage,
where evacuation or rescue is necessary, the door guard
locking switch can be unlocked by pushing the
emergency red release button from outside the cabin
or by turning the red release lever from inside the cabin.
(See Figure
6
in Section 3.2.1.1)
•
Inside the cabin
Turn the red release lever to open the sliding door.
•
Outside the cabin
Press the red release button to open the sliding door.
Top hatch can be opened from both sides, thus allowing
egress to and ingress from above.
4.3.3 Top/Bottom hatches
•
Inside the cabin
Use the internal emergency ladder to reach the top
hatch.
To open top hatch push it up. Once top hatch is
open, ladder becomes totally accessible.
•
Outside the cabin
To open top hatch pull it up. Once top hatch is open,
access inside the cabin by means of the internal
emergency ladder.
Figure 2
6
: Top hatch
Top hatch
The service lift has two bottom hatches, one on the floor
of the cabin and the other on the bottom full cover
obstruction device. The bottom hatches can be opened
from both sides, the bottom cabin hatch opens inwards,
and the bottom obstruction device hatch opens
outwards, thus allowing egress to and ingress from
below.
Bottom hatches
•
Inside the cabin
Before using the bottom hatches, the user must
anchored to the lower additional anchor point inside
the cabin.
To open the bottom cabin hatch pull it up. Once it is
open, push down the bottom obstruction device hatch
to open it.
When both bottom hatches are open, ladder becomes
totally accessible to exit through the bottom of the
service lift.
•
Outside the cabin
To open the bottom obstruction device hatch pull it
down. Once it is open, push up the bottom cabin
hatch to open it.
When both bottom hatches are open, the user must
be anchored to the lower additional anchor point
inside the cabin before access from the bottom of the
service lift.
DANGER
The lower anchor point must only be used for
evacuation/rescue operation.
Figure 2
7
: Bottom hatches
4.3.4 Stop/Emergency stop
a) Release the Up or Down button; the service lift should
stop
If it does not:
b) Push the EMERGENCY STOP button, and all controls
should be disabled.
Summary of Contents for OCTOPUS XL120
Page 2: ......
Page 11: ...2 5 Dimensions 2 5 1 Octopus XL120 Figure 3 Octopus XL120 dimensions 970 1200 2812 2635 8...
Page 35: ......
Page 36: ...www avanti online com...