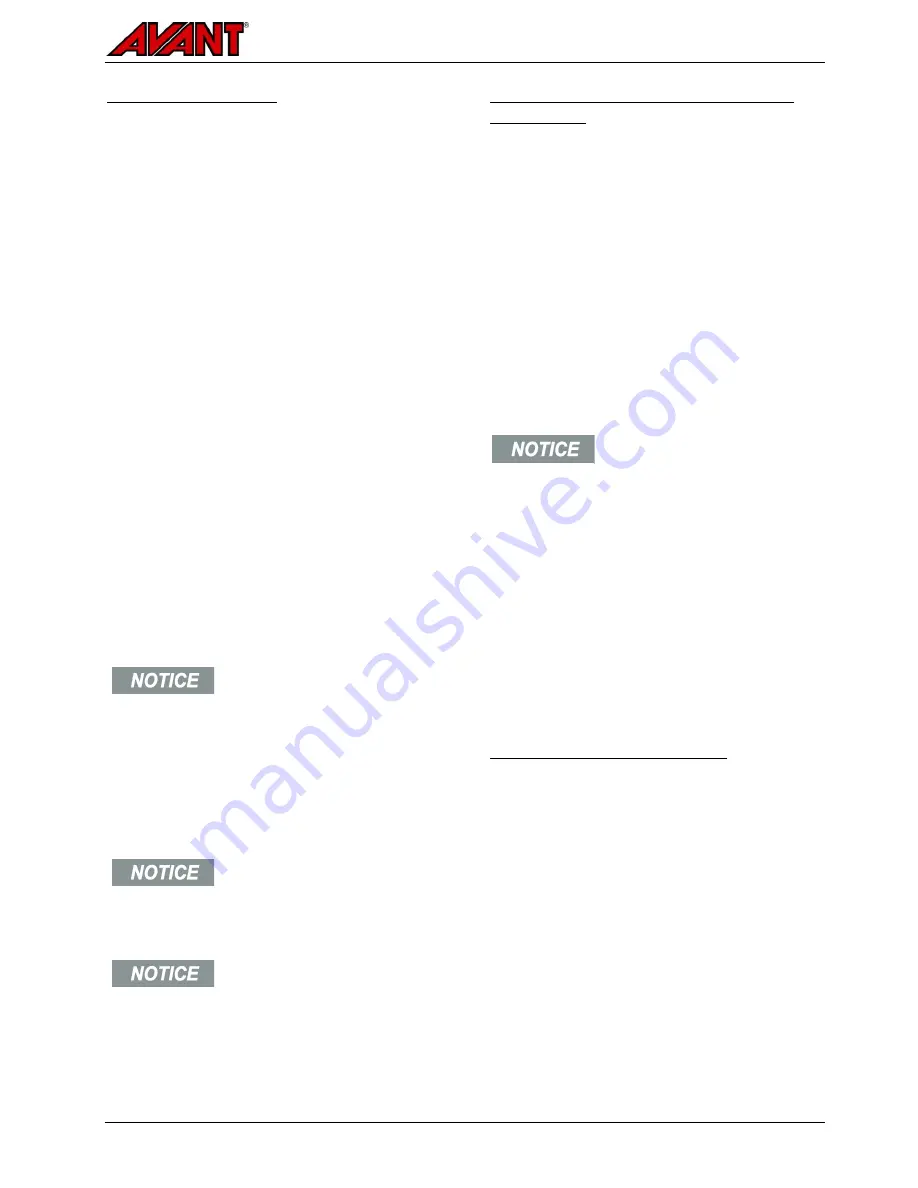
Avant 220/225
41
To start the engine:
1.
Perform daily checks (see
Maintenance &
Service
on page 57)
2.
Turn the battery disconnect switch to ON
Open gas bottle valve (225LPG only)
3.
Move the hand throttle lever to idle position
Cold start, 220 only: Pull choke knob halfway
or fully up
4.
Make sure that auxiliary hydraulics is switched
off (lever in neutral position),
see page 32.
Do
not press on the drive pedals.
5.
Turn the ignition key to the right, to ON
position. Signal lamps on the multi-function
display will light up briefly for self-check. Oil
pressure and charge indicator lights will remain
lit.
6.
Turn the ignition key further to the right, to start
position and hold until engine starts. Return
key to ON position in controlled manner.
220: Push choke knob slightly down once the
engine
has
started.
Depending
on
temperature, the knob may be pushed fully
down immediately after start or after warming
up for a moment first. Keep choke knob in full
down position in normal use.
.
..
Do not actuate the starter for more
than 10 seconds at a time. If the
engine does not start, wait for one
minute before repeating attempt. If
the engine does not start after a
few attempts, or runs poorly,
See
troubleshoot
on page 74 and the
engine owner’s manual.
After starting:
Allow the engine to warm up and
engine oil to circulate in the engine
for a moment before loading the
engine or increasing engine revs.
.
..
Make sure that all the warning
lights on the control panel are off
when the engine is running. If the
engine does not start after a few
attempts, or runs poorly,
See
troubleshoot
on page 74.
Stopping the engine (Safe stopping
procedure)
1.
Lower the boom completely down. Place
attachment firmly on the ground, engage
parking brake, stop the attachment (move
auxiliary hydraulics control lever to neutral
position,
see page 32), set engine revs to
idle.
2.
Stop the engine by turning the ignition key to
the OFF position (to the left)
3.
Release auxiliary hydraulics pressure
(see
page 56).
4.
Prevent unauthorised use of the loader. Take
off the ignition switch and turn the power off
with the battery disconnect switch.
Stop the engine as soon as possible,
if any of the following symptoms is
observed. Find out the cause before
restarting.
The oil pressure warning light, or malfunction
indication light turns on during operation.
Engine rpm increases and/or decreases
suddenly by itself, without touching the
throttle lever.
A sudden and unusual noise is heard.
Sudden increase in engine vibration.
The colour of the exhaust fumes suddenly
darkens or turns white.
Run the LPG system empty
Before replacing an empty LPG bottle, storage of the
loader, or any maintenance work on the engine,
empty the LPG fuel system.
Shut off the manual shut off valve while engine is
running
Allow to run on idle until engine shuts down
Summary of Contents for 225
Page 1: ...English Operator s Manual 2016 www avanttecno com ...
Page 50: ...Avant 220 225 50 ...
Page 77: ...Avant 220 225 77 Notes ...
Page 78: ...Avant 220 225 78 Notes ...
Page 79: ...Avant 220 225 79 Notes ...
Page 81: ...Avant 220 225 2017 1 ...