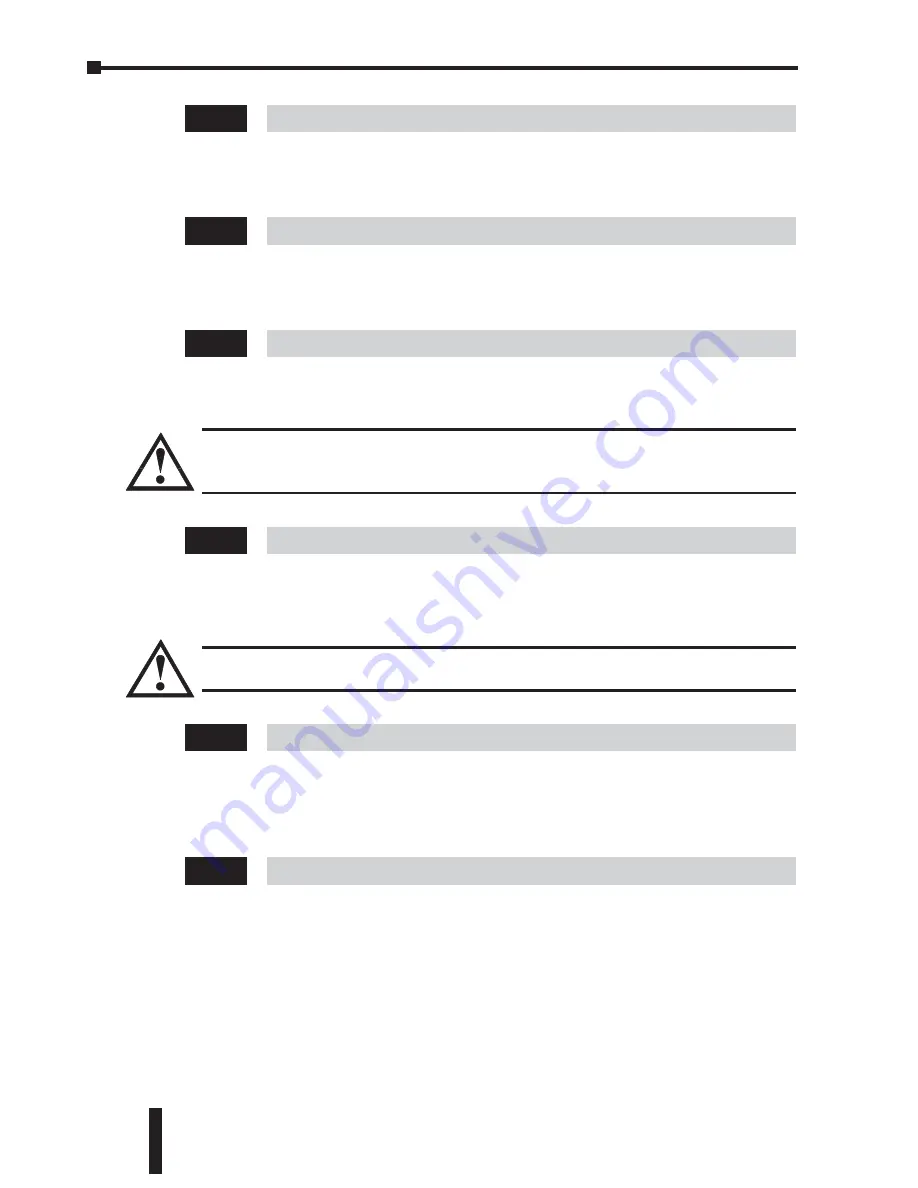
Chapter 3: Keypad Operation and Quickstart
GS1 Series AC Drive User Manual
3–10
Motor Base Frequency
Setting: 60
Range: 50/60/400
Default Setting 60
This parameter setting is determined by the motor nameplate.
Motor Base RPM
Setting: 3525
Range: 375 to 9999 RPM
Default Setting: 1750
This parameter setting is determined by the motor nameplate.
Motor Maximum RPM
Setting: 3600
Range: 0-03 to 9999 RPM
Default Setting: 0-03
This parameter setting is determined by the needs of the application.
W
ARNING
: The Motor Maximum RPM parameter (0-04) should never exceed the
maximum RPM rating for the motor you are using. If this information is not readily
available, consult your motor manufacturer.
Stop Methods
Setting: 1
Range: 0 - Ramp to Stop
Default Setting: 0
1 - Coast to stop
The application requires that this parameter be set to Coast to Stop.
W
ARNING
: If the Stop Method for the GS1 AC drive is set for Coast to Stop, the AC
drive will ignore any setting you have for Deceleration Time (1-02).
Acceleration Time
Setting: 20.0
Range: 0.1 to 600 sec
Default Setting: 10 sec
The motor should accelerate from 0 RPM to Base RPM (0-03) in 20
seconds.
Volts/Hertz Settings
Setting: 2
Range: 0 - General Purpose
Default Setting: 0
1 - High Starting Torque
2 - Fans and Pumps
3 - Custom
The GS1 Series AC drive has some predefined torque settings that meet
the needs of most applications. A custom setting is available if needed.
In this example, the motor will be running a pump.
2-00
1-01
1-00
0-04
0-03
0-02
Summary of Contents for GS1-10P2
Page 1: ...GS1 Series Drives U s e r M a n u a l 120V Input 0 25 0 5 Hp 230V Input 0 25 2 0 Hp...
Page 15: ......
Page 117: ......
Page 123: ......
Page 137: ...GS1 M...