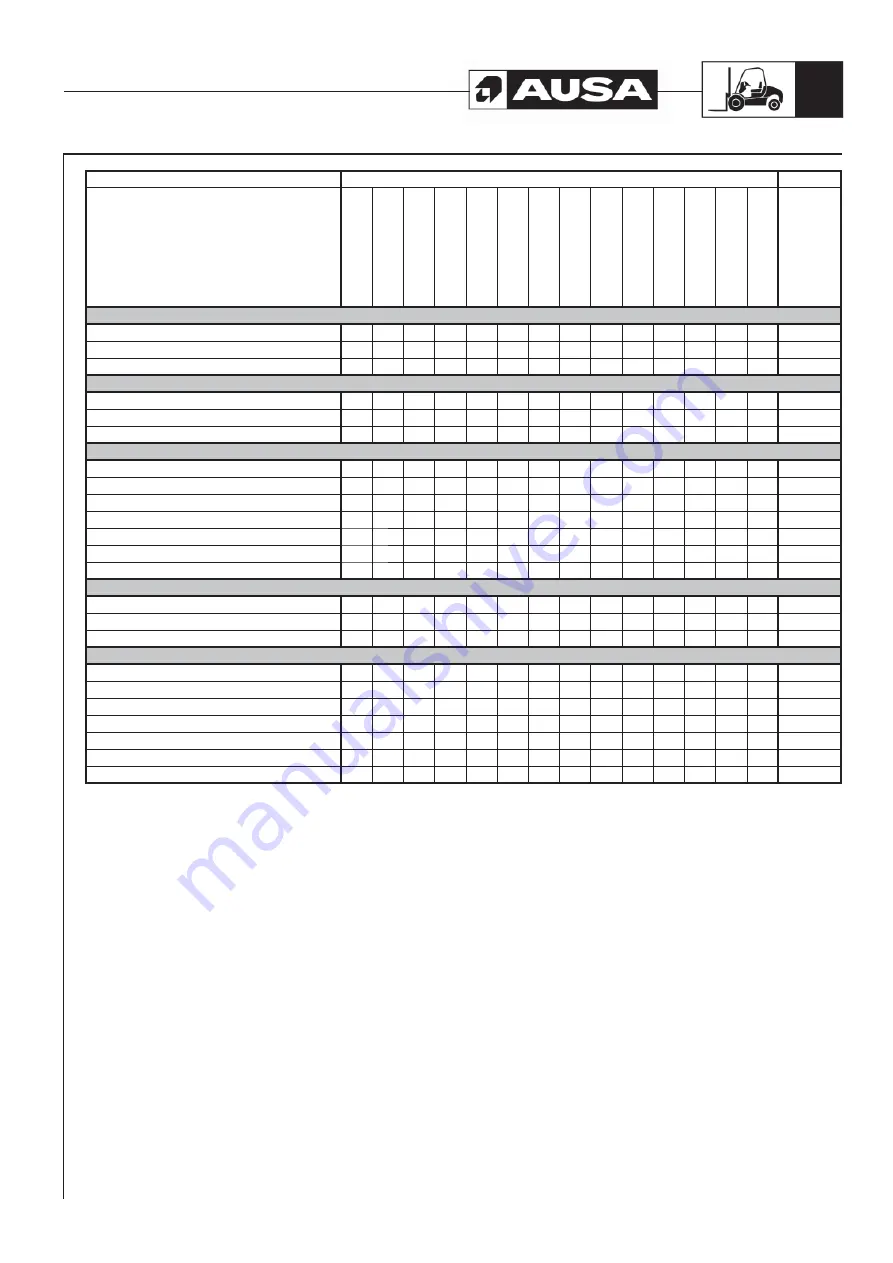
79
C200H-HI / C200H x4 / C250H-HI
C250HI LE / C250H x4 / C250H x4 LE
EVERY
I:
Inspect, verify, clean, lubricate, replace if necessary
Initial inspection (50 h)
Every 100 h.
Every 200 h.
Every 250 h.
Every 400 h.
Every 500 h.
Every 800 h.
Every 1000 h
Every 1500 h.
Every 3000 h.
Every week
Every month
Every year
Every 2 years
To
be performed by
C:
Clean
L:
Lubricate
R:
Replace
GREASING POINTS
Masts guides
L
CUSTOMER
Nipples (see section “Greasing points” in this Manual)
L
CUSTOMER
Cables and articulations (throttle, lifting rams...)
L
CUSTOMER
TRANSFER-BOX
Oil (1)
R
R
I
R
CUSTOMER
Oil leaks
I
CUSTOMER
Screws and nuts torque
I
CUSTOMER
AXLES (FRONT AND REAR)
Oil (1)
R
R
I
R
CUSTOMER
Oil leaks
I
CUSTOMER
Fixation wheel nuts torque
I
CUSTOMER
Chassis fixation screws (torque)
I
DEALER
Cardan joint fixation screws (torque)
I
DEALER
Flange fixation nut (torque)
I
DEALER
Condition of tires and pressures
I
CUSTOMER
BRAKES
Brake fluid (3)
R
I
R
CUSTOMER
Foot brake adjustment (3)
I
I
DEALER
Handbrake adjustment
I
I
DEALER
BODY / FRAME
Cabin
I
CUSTOMER
Seat belt (3)
I
CUSTOMER
Foot plate, access steps and handles (3)
I / C
CUSTOMER
Guards and covers (3)
I
CUSTOMER
Plates and decals (3)
I / C
CUSTOMER
Tipped cabin safety latch
I
CUSTOMER
Cabin lock
I
CUSTOMER
(1) Initial inspection. The initial maintenance is very important and must not be neglected.
(2) To be performed by an authorized AUSA dealer.
(3) Daily inspection item.
(4) More often under severe use such dusty areas, sand, snow, wet or muddy conditions.
(5) Or at least once a year.
(6) replace only if it is necessary.