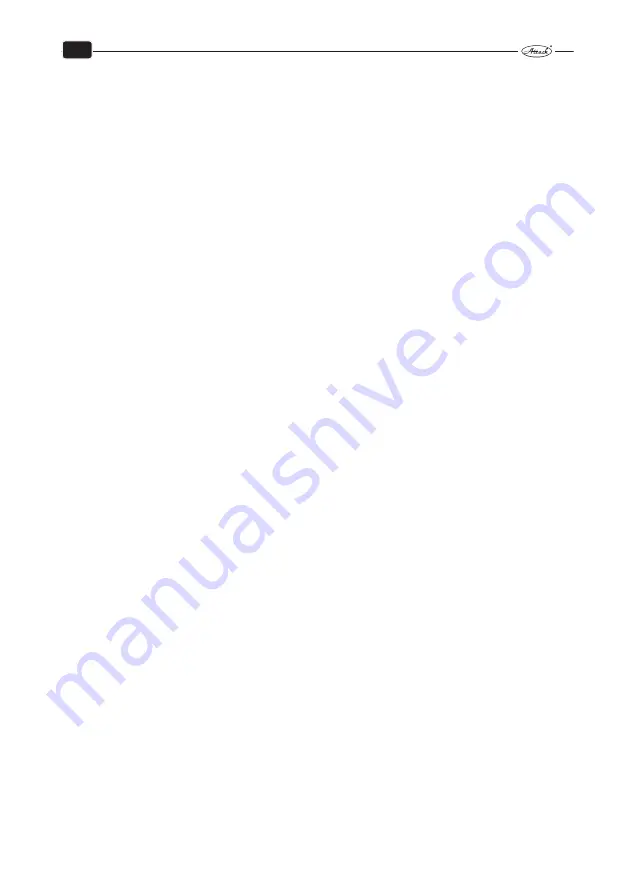
37
EN
7.9
ERROR MESSAGES
The connection of all sensors of the regulator is permanently monitored. If the regulator detects
that some of the sensors is not connected, the error messages are displayed. Messages about the
boiler overheating or fuel shortage are also displayed.
7.9.1
ERROR MESSAGES DISPLAYED
[FUEL]
– is displayed, when there is not enough fuel in the boiler. The sufficient amount of fuel is
defined by the parameter
c
90, where the figure 90 is related to the adjusted value 90 °C. Then, if
the flue gas temperature decreases under this adjusted value within the time Fb30 (time of boil-
er stop by fuel shortage), the regulator displays the [FUEL] message. To start the boiler again, it is
necessary to remove the message by the STOP button and then to press the START.
[HOT]
– is displayed, when the flue gas temperature exceeds the maximum permitted value set
by the parameter c300 (means 300 °C). The ventilator is stopped in this case. After the tempera-
ture decreases under the adjusted flue gas temperature, the ventilator is started again.
[E 1]
– is displayed, when the boiler temperature sensor fails or when it is not connected. In such
case is the regulator taking actions to ensure the safety of the boiler – the fan is stopped (if it is
currently in operation) and the circuit pump is started for eventual safe boiler cooling. After the
cause of error is removed, the error message can be erased by the STOP button.
[E 2]
– is displayed, when the boiler temperature exceeds the boiler overheating temperature
A99. The regulator stops the flue gas fan and starts the circuit pump. The error message can be
removed by the STOP button after the boiler temperature decreases to the safe value.
[E 8]
– is displayed, when the additional sensor fails (in the D.H.W. tank or accumulation tank). If
this sensor works for the D.H.W. tank, the warming is blocked. If the sensor works for the accu-
mulation tank, the pump will be permanently working. This error message cannot be removed
by the STOP button. It is automatically erased after the sensor failure is repaired.
[E128]
– is displayed, when the flue gas temperature sensor fails. In this case is the boiler control
switched to regulate according to the boiler temperature. The error message is erased automati-
cally after the fault of the flue gas temperature sensor is solved.
[
E 3
] If several failures occur in one moment, their total is displayed. In such case it is necessary to
check the functionality of all sensors.
Summary of Contents for ATTACK DPX 25 COMBI Pellet
Page 1: ...www attack sk EN 07 2019 ATTACK DPX COMBI PELET Instructions for use EN ...
Page 2: ......
Page 66: ...65 EN 13 ELECTRICAL SCHEMES 13 1 ATTACK DPX 25 30 35 COMBI PELLET ...
Page 68: ...67 EN 13 2 ATTACK DPX 40 45 50 COMBI PELLET ...
Page 83: ...11 ...
Page 98: ......
Page 99: ......