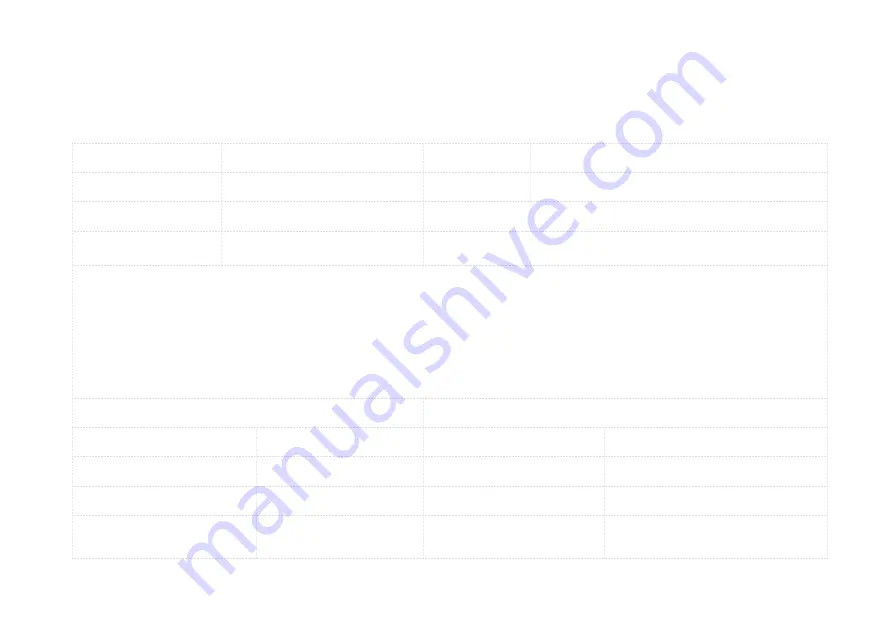
9. NOISE EMISSION VALUES
Material
Aluminum
LwA
98 dB (Measured Value)
Length
1220 mm (48”)
LpA
93 dB (Average Sound Pressure Value
Width
70 mm (3”)
K
2 dB (Tolerance in the Measurements)
Height
20 mm (0.8”)
The values stipulated above represent the emission level, and do not necessarily represent safe working level.
There is a relation between emission and exposure levels, however, this cannot be used as a reliable relation to deter-
mine whether advanced precautions are necessary. The factors, which affect the actual level of noise exposure, are
among others physical properties of the building where the saw is operated, possible other operations in proximity to the
saw, number of machines being used, in other words, other sources of noise. Furthermore, allowed noise exposure level
s may vary from country to country. This information serves for the saw operator to determine and evaluate risks accord-
ingly.
Saw Specifications
Saw Specifications
Rotation of Saw Blade
2000 rpm
Saw Blade Size
700 mm (28”)
Motor Power
4 kW
Saw Blade Thickness
5 mm
Nominal Voltage
400 V
Blade Shaft Thickness
4 mm
Blade Progress Speed
65.
/ sec. (Aluminum
material)
35
Summary of Contents for ACK700
Page 2: ...OVERALL DIMENSIONS mm 2 ...
Page 3: ...CUTTING DIAGRAM 3 ...
Page 4: ...PARTS LIST RESİM FIGURE РИСУНОК 1 4 ...
Page 5: ...RESİM FIGURE РИСУНОК 2 5 ...
Page 6: ...RESİM FIGURE РИСУНОК 3 RESİM FIGURE РИСУНОК 4 6 ...
Page 15: ...3UA030030 0005 ANGLE LOCK PIN 1PL040000 0069 GUARD GLASS 15 ...