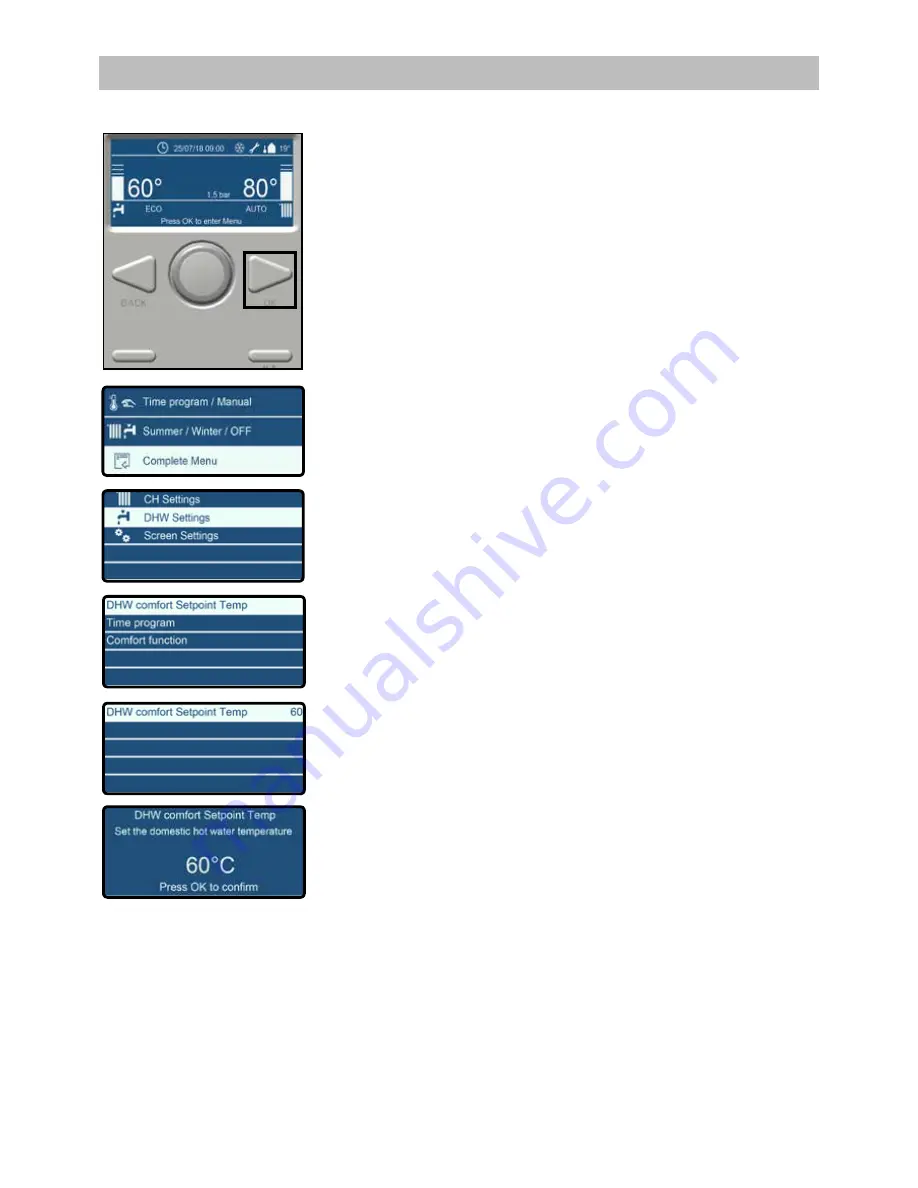
Installation & Servicing instructions ATAG iC-Range
40
12.1 Change the Domestic Hot Water setpoint temperature
1
From the controller Home screen, press
OK
.
2
Turn the selector wheel to highlight
Complete Menu
.
Press
OK
.
3
Turn the selector wheel to highlight
DHW Settings
.
Press
OK
.
4 Option
DHW Comfort Setpoint Temp
is highlighted.
Press
OK
.
5
The current DHW comfort Setpoint temperature is displayed.
Press
OK
.
7
Turn the selector wheel until the desired temperature appears on the
screen.
Press
OK
.
Available temperature settings:
10˚C - 65˚C