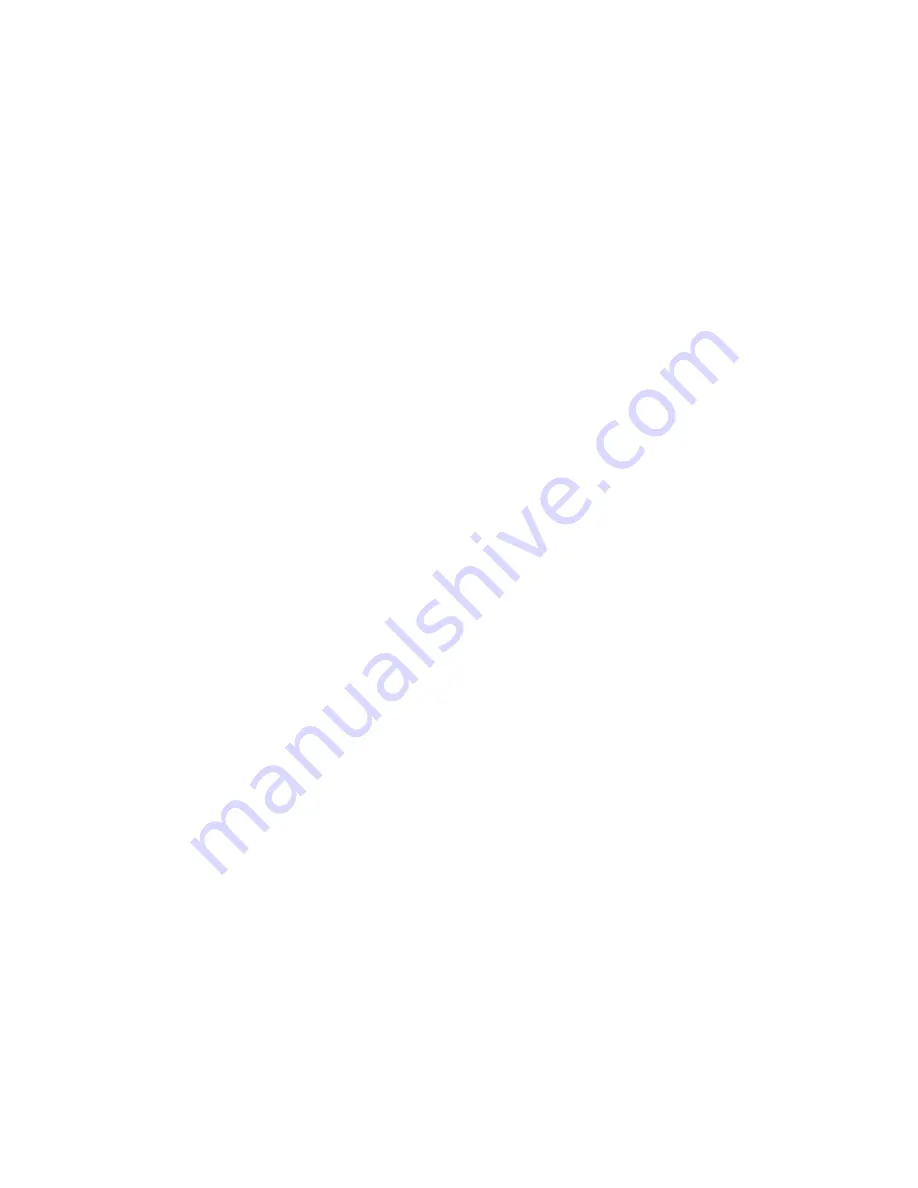
507607-03
Issue 1827
Page 8 of 23
Flushing Existing Line Set and Indoor Coil
This procedure should not be performed on systems which
contain contaminants, such as compressor burn out.
Required Equipment
The following equipment is needed to flush the existing line
set and indoor coil (Figure 10). Two clean R-22 recovery
bottles, an oil-less recovery machine with a “pump down”
feature, and two sets of gauges (one for use with R-22 and
one for use with R-410A).
Flushing Procedure
NOTE:
The line set and/or indoor coil must be flushed with
at least the same amount of refrigerant that previously
charged the system. Check the charge in the flushing
cylinder before flushing the unit.
1. Remove existing R-22 refrigerant using the appropriate
procedure.
If the existing outdoor unit is not equipped with shutoff
valves, or if the unit is not operational AND the existing
R-22 refrigerant will be used to flush the system:
Disconnect all power to the existing outdoor unit. Connect
the existing unit, a clean recovery cylinder, and the
recovery machine according to the instructions provided
with the recovery machine. Remove all R-22 refrigerant
from the existing system. Refer to the gauges after
shutdown to confirm that the entire system is completely
void of refrigerant. Disconnect the liquid and suction lines
from the existing outdoor unit.
If the existing outdoor unit is equipped with manual shutoff
valves AND new R-22 refrigerant will be used to flush the
system:
Start the existing R-22 refrigerant system in cooling mode
and close the liquid line valve. Pump all the existing R-22
refrigerant back into the outdoor unit.
(It may be necessary to bypass the low pressure switches
to ensure complete refrigerant evacuation.)
When the low side system pressures reach 0 psig, close
the suction line valve. Disconnect all power to the existing
outdoor unit. Refer to the gauges after shutdown to confirm
that the valves are not allowing refrigerant to flow back
into the low side of the system. Disconnect the liquid and
suction lines from the existing outdoor unit.
2. Remove the existing outdoor unit. Set the new R-410A
unit and follow the brazing connection procedure
outlined previously to make line set connections. Do
not install the R-410A thermal expansion valve at this
time.
3. Make low voltage and line voltage connections to the
new outdoor unit. Do not turn on power to the unit or
open the outdoor unit service valves at this time.
4.
Remove the existing R-22 refrigerant flow control
orifice or thermal expansion valve before continuing
with flushing procedures. R-22 flow control devices
are not approved for use with R-410A refrigerant and
may prevent proper flushing. Use a field-provided
fitting to reconnect the lines.
5. Remove the pressure tap valve cores from the
4SCU16/18LS units service valves. Connect an R-22
cylinder with clean refrigerant to the suction service
valve. Connect the R-22 gauge set to the liquid line
valve and connect a recovery machine with an empty
recovery tank to the gauge set.
6. Set the recovery machine for liquid recovery and start
the recovery machine. Open the gauge set valves to
allow the recovery machine to pull a vacuum on the
existing system line set and indoor coil.
7. Invert the cylinder of clean R-22 and open its valve to
allow liquid refrigerant to flow in to the system through
the suction line valve. Allow the refrigerant to pass from
the cylinder and through the line set and the indoor coil
before it enters the recovery machine.
8. After all of the liquid refrigerant has been recovered,
switch the recovery machine to vapor recovery so that
all of the R-22 vapor is recovered. Allow the recovery
machine to pull a vacuum on the system.
NOTE:
A single system flush should remove all of
the mineral oil from the existing refrigerant lines and
indoor coil. A second flushing may be done (using
clean refrigerant) if insufficient amounts of mineral oil
were removed during the first flush. After each system
flush, allow the recovery machine to pull a vacuum on
the system at the end of the procedure.
9. Close the valve on the inverted R-22 cylinder and the
gauge set valves. Pump the remaining refrigerant out
of the recovery machine and turn the machine off.
10. Use nitrogen to break the vacuum on the refrigerant
lines and indoor coil before removing the recovery
machine, gauges, and R-22 refrigerant drum. Re-
install pressure tap valve cores into the 4SCU16/18LS
unit’s service valves.
11.
Install the fixed orifice (or thermal expansion valve
approved for use with R-410A refrigerant) in the liquid
line at the indoor coil.
Refrigerant Metering Device
4SCU16/18LS units are designed for use with TXV
systems. Refer to the appropriate following section for
information on installing the chosen refrigerant metering
device.