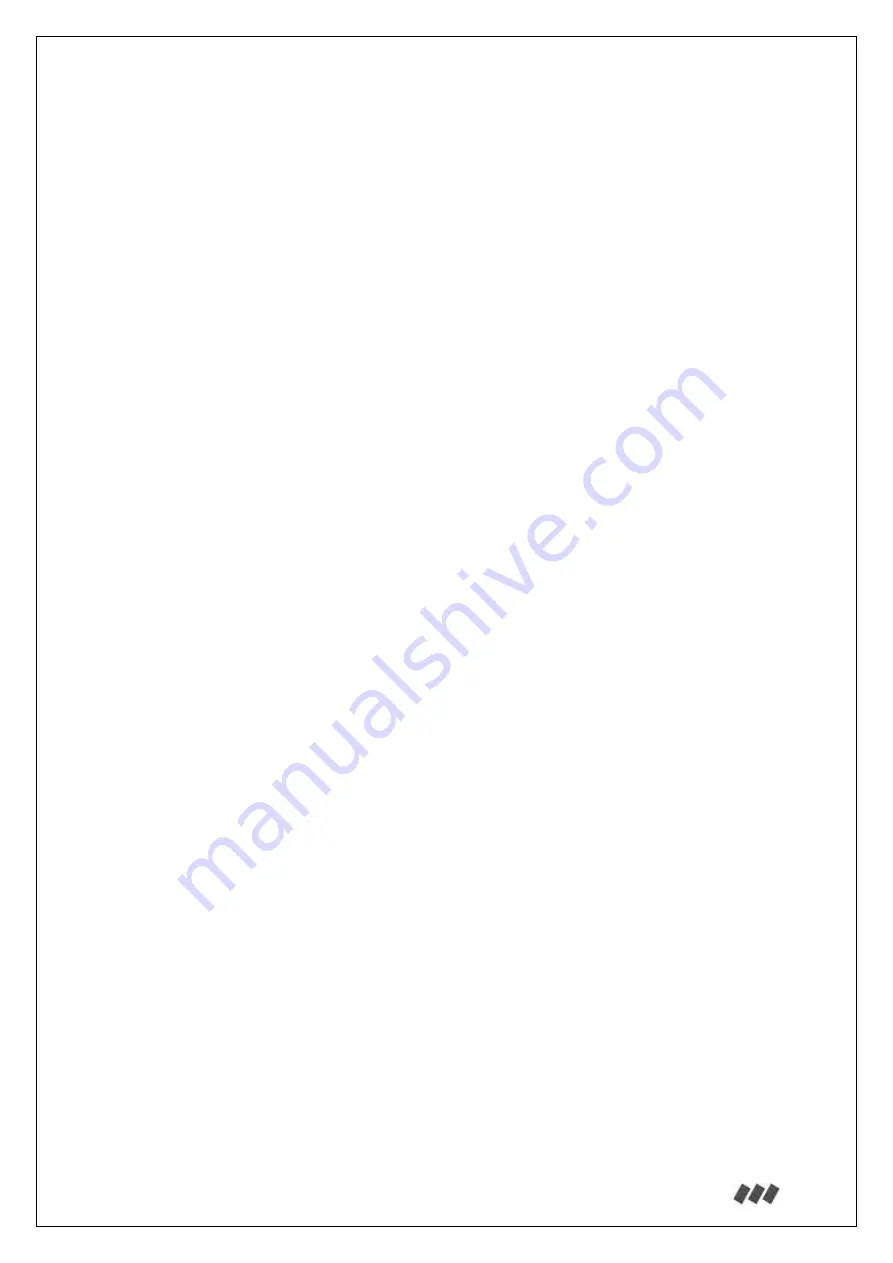
ARKEL Elektrik Elektronik Ltd.
Ş
ti. www.arkel.com.tr
08.2012
ADrive
71
20. DRIVING SYNCHRONOUS MACHINES with ADrive
20.1. Encoder connection
To be able to communicate with absolute encoders which have to be used with synchronous
motors, an additional ENCABIT-Plus communication board is necessary. The encoder wirings to
this board must be done as explained in section
13.2.4
.
20.2. Motor parameters
The following values must be entered in the ADrive parameters menu:
2.0
-Motor Type: Synchronous
2.1
-Nominal Speed: Nominal speed of the car (for example: if the motor speed is 2 m/s and
the gear ratio is ½, the value of 1 m/s must be entered)
2.2
-Nominal Speed RPM: RPM value indicated on the motor name plate
2.5
-Motor Voltage: Motor voltage
2.6
-Motor Current: Motor current
2.19
- Number of poles: Number of motor poles
20.3. Autotuning:
a)
If possible, a dynamic autotuning should be performed before hoisting the car (without
load). If this is not possible during dynamic autotuning, an amount of weight which will
balance the total car weight and the counterweight should be added into the car. The
balance of the counterweight and the car may be checked by manually releasing the brakes
and making sure that the car does not move with released brakes.
During dynamic autotuning, the motor will turn one revolution in each direction. So please
make sure that the car has enough distance to the top and bottom of the shaft before starting
the autotuning.
In cases where dynamic auto-tuning is not possible, auto-tuning may be performed statically.
For static auto-tuning, “9.1-AUTO TUNE” parameter must be set to “ENABLE_STATIC”.
The most precise way to determine the motor offset angle is to perform a dynamic auto-
tuning with ropes disconnected from the rotor (without load). With static auto-tuning, an
error of up to +/- 12 degrees may be introduced and this error will cause the travel currents
to be %3-%4 higher than ideal.
b)
To start autotuning, set the “
9.1-Autotune
” parameter to
“Enabled”
and exit the menu.
ADrive will display “
Waits Autotune
” on its screen. At this point, turn the switch on the
recall terminal to “
Rev
” position and press either up or down button. Keep the button
pressed until you see the message “
Autotune End
” on the ADrive screen.
If the message “
Wrong direction
” is displayed, either toggle the parameter “
2.18-Encoder
direction
” or swap any two of the 3 motor power lines (U, V, W).
If the message “
Auto tune fails
” is displayed during autotuning, please check the motor
and encoder connections.