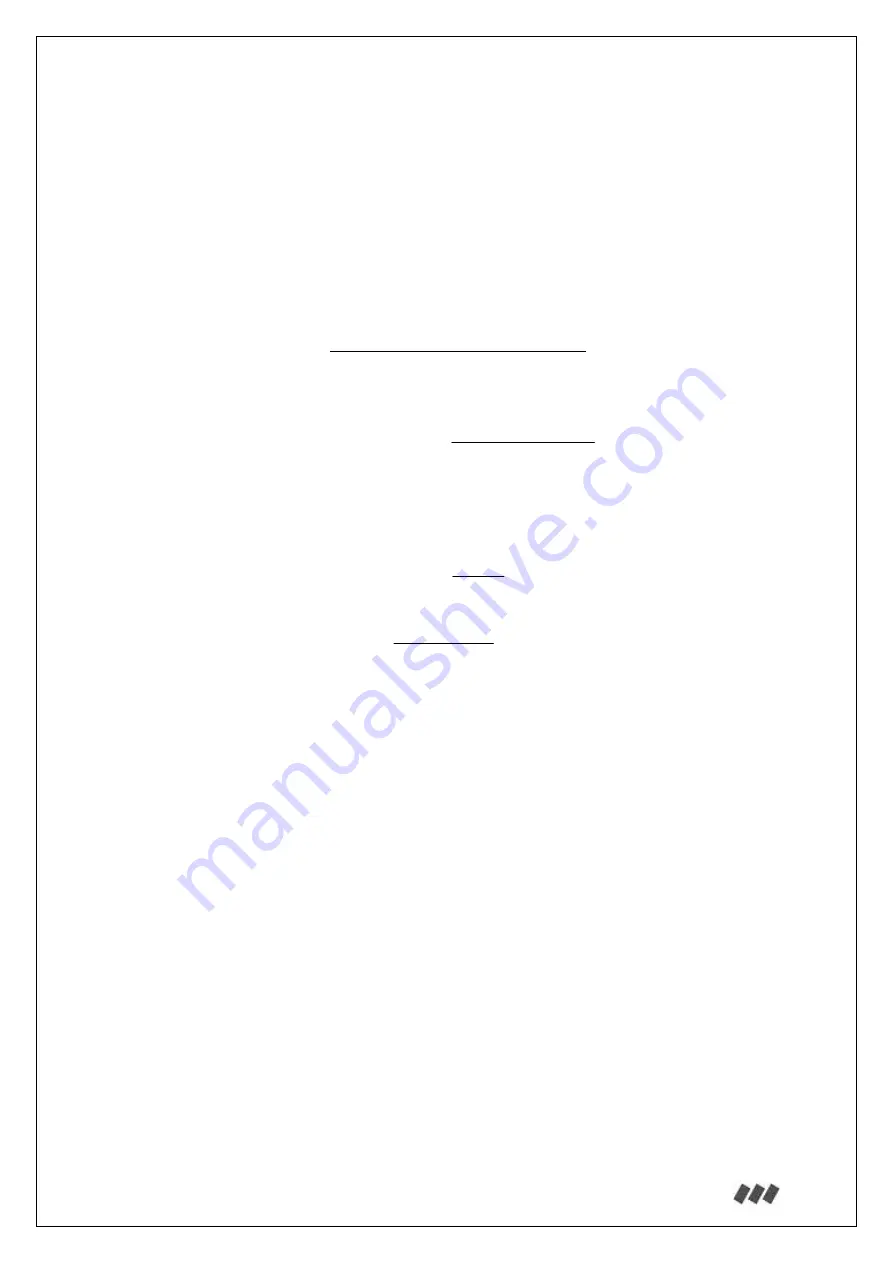
ARKEL Elektrik Elektronik Ltd.
Ş
ti. www.arkel.com.tr
08.2012
ADrive
57
2.8-Motor Power Factor
(COS Q: 0.1 – 1.0)
Motor power factor. This value is specified on the motor plate by the motor manufacturer.
2.9-Rotor Slip
(R_slip: 1.0 – 9.0 Hz)
Asynchronous
motors have a slip between rotor and electrical rotating field applied to stator.
The value of this slip is entered by this parameter. Too small slip value causes over current and
heating of motor. Too high slip causes unstable motor current and vibration. It is adviced not to
change this parameter’s default value if there is no need. Slip frequency may be calculated by the
formula below:
Fnom
pm
StatorNomR
m
MotorNomRp
pm
StatorNomR
Fslip
*
)
(
)
(
)
2
/
(
60
*
les
numberofpo
Fnom
pm
StatorNomR
For example : The slip for a 50Hz , 1440 rpm , 4 poles motor is like below:
1500
2
60
*
50
pm
StatorNomR
Rpm
2
50
*
)
1500
(
)
1440
1500
(
Fslip
Hz
2.10-No Load Motor Current
(Inoload: %20 - %80)
Ratio of no load current to nominal current. Too high value causes high motor current.
Consequently motor heat rises and more power consumed. Too low value causes torque loss
which shows itself as a vibration. Values of parameters 2.9 and 2.10 are very critical values for
the motor drive performance. Optimum value is where minimum motor current is obtained
without vibration. For getting to this optimum values the elevator must run a few times and the
motor current should be monitored.
2.11-Rotor Time Constant
(T_rotor: 1- 999 ms)
Time constant for motor rotor. Dependence of the inverter to this parameter is reduced, do
not change this parameter if not necessary. This value may be get from the motor manufacturer.
This parameter is needed for vector control.