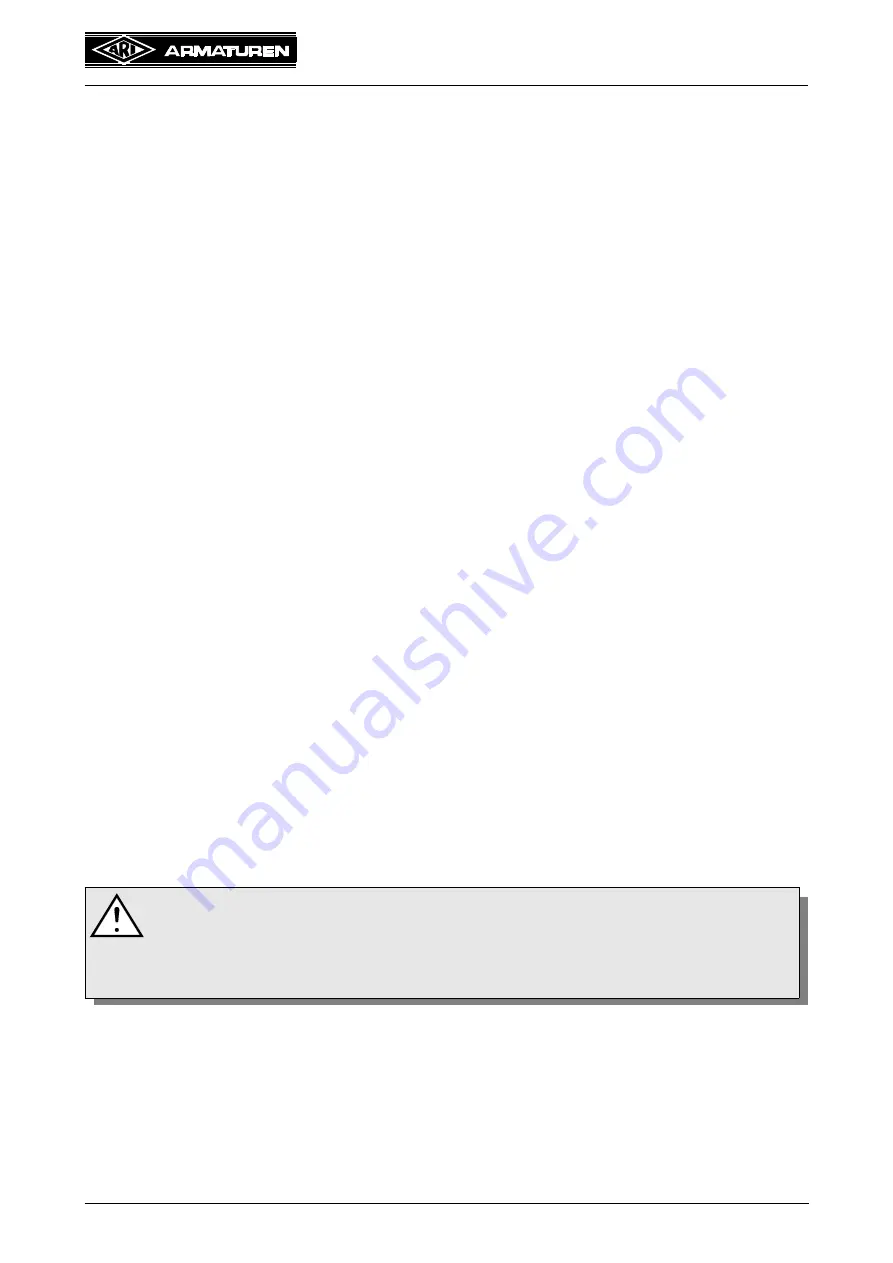
0040506004 0919
Page 2-5
Operating and installation instructions
Thrust actuator ARI-PACO
®
2G 1,6D/Y
4.0 Description
4.1 Field of application
Actuating or shut-off valves are operated with the ARI-PACO
®
2G linear actuators which have a
linear nominal path of up to 40 mm and require a thrust force of 1,6 kN. The linear actuators are
adjusted to the thrust forces denoted in the technical data. When delivered with the valve the linear
actuator travel has been adjusted to the control path of the valves. The plant planner is responsible
for the professional selection of the drive variant for the respective armature and the employment of
the linear actuators according to the current technical data. Any use of the linear actuators in ways
other than described in the technical data as well as inappropriate usage is hence not in accordance
with the regulations. The environment must conform to the currently-valid EMV regulations. Annual
inspection is required in order to sustain electromagnetic compatibility. Furthermore, the level of the
electromagnetic load in the environment should be monitored if electrical or electronic components
have been mounted in the surroundings.
4.2 Method of functioning
The thrust actuator must be mounted to a control or a isolation valve.
The transfer of force is carried out by means of a coupling protected from torque.
The torque protection also functions as the travel display.
The lift settings can be read off between the 2-ear clamps mounted to the column.
The electrical modules are separated from the transmission and are located in the sealed housing,
protected against operating and environmental conditions.
After removing the housing, the switching and notification assemblies are easily accessible.
The twisting movement of the motors is transferred to cylindrical gears on the stem nut.
The drive stem, secured against torque, screws itself into the stem nut and thus, depending on the
direction, a pulling or pushing movement is created. In the end positions of the valve, the stem nut is
pressed against a spring assembly and generates a closing force.
The motor is switched off by means of a force-dependent or electronic switch. The force-dependent
switch will also switch off the motor if a foreign body has come between the valve seat and cone.
The switch protects the valve and the linear actuator from damage.
4.2.1 D Version
The thrust actuators are equipped with a load-dependent travel switch for the retracting direction
(S1), a load-dependent travel switch for the extending direction (S2) and a stroke-dependent travel
switch for the retracting direction (S3).
The load-dependent travel switches (S1, S2) switch-off the motor as soon as the factory-set thrust
force is attained.
The stroke-dependent travel switch (S3) switches off the motor as soon as the lift or stroke is
attained. If the thrust actuator is supplied on a straight through valve, the stroke-dependent travel
switch S3 is set in such a way that the motor of the thrust actuator is switched off as soon as the
maximum valve-lift is attained.
If the thrust actuator is supplied on a three-way valve, the trip cam belonging to travel
switch S3 is set in the retracting direction in the trip slide to such a downward extent that the upper
final position of the valve is attained prior to travel switch S3 being reached, thus causing the load-
dependent travel switch S2 to switch-off the motor.
For this function, all three switches reveal interlock-controlled circuitry on the board.
ATTENTION !
- The settings of the load-dependent travel switches must on no account whatsoever be
changed!
- For the function of the stroke-dependent travel switch (S3), an optionally available trip
slide is necessary.