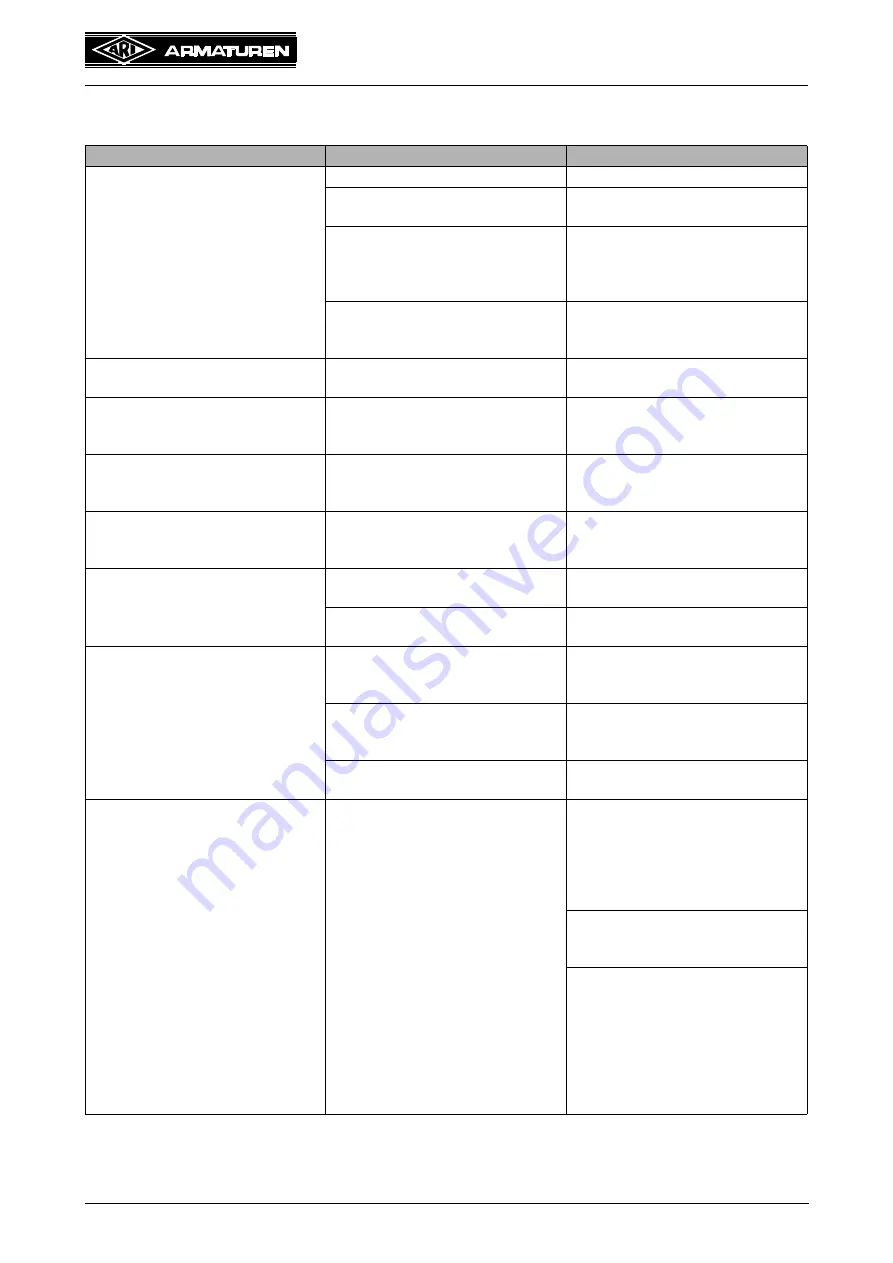
0040506004 0919
Page 2-37
Operating and installation instructions
Thrust actuator ARI-PACO
®
2G 1,6D/Y
9.2 ARI-PACO
®
2G 1,6Y
Fault
Possible Causes
Remedy
Green LED does not lit
Power failure
Check the mains power supply
Operating voltage is incorrect
Connect the operating voltage
indicated on the rating plate
Elektronics have burnt out
Make sure the mains voltage
coincides with the value indicated
on the rating plate. Replace the
electronics.
Terminal not connected correctly
or cable does not make proper
contact inside terminal
Insert the terminal securely and
check the connecting cable
Actuator starts briefly, then stops
and starts again briefly
CDF management is active due
to internal overheating
Protect against radiated heat, lag
the pipes
Actuator stops for 45 s or does
not respond to control signals for
45 s
Actuator has detected a
handwheel movement
The motor is not started for
another 45 s for safety reasons
Initialization cancelled; red and
yellow LEDs lit
Outside the valid travel range
Possible causes: Incorrect fitting
projection, incorrect column
length, valve missing
Red LED lit
Actuator not initialized yet.
Start an initialization run after
mounting the actuator on a valve
and connecting the control signal
No values or incorrect values at
analogue output
Parameter settings are incorrect
Set the parameters as described
in 5.5.2.3 Switch functions
Analogue output card missing or
defective
Replace the analogue output
card
Actuator oscillates continuously
about a point
Proportional action Xp setting on
controller is too low
Increase the Xp value (refer to
the controller Operating
Instructions)
Dead band setting on controller is
too low
Increase the dead band value
(refer to the controller Operating
Instructions)
Dirty slide
Clean surface with Greycode
(black/white)
Actuator cannot be controlled
with analogue control signal
Actuator is set to 3-point
operation or is currently
controlled by a 3-point signal
(indicated by lit LED above
3-point connector)
By withdrawing the connector for
the 3-point signal, you can
determine whether the actuator is
set to 3-point operation or
whether it is simply being
controlled by a 3-point signal
If the LED goes out, a 3-point
signal is present, e.g. from an
anti-freezing contact
If the LED is still lit, the actuator is
set to 3-point operation. An
analogue control signal must be
present during the initialization
run in order to control the
actuator with an analogue signal!
Repeat the initialization with an
analogue control signal applied