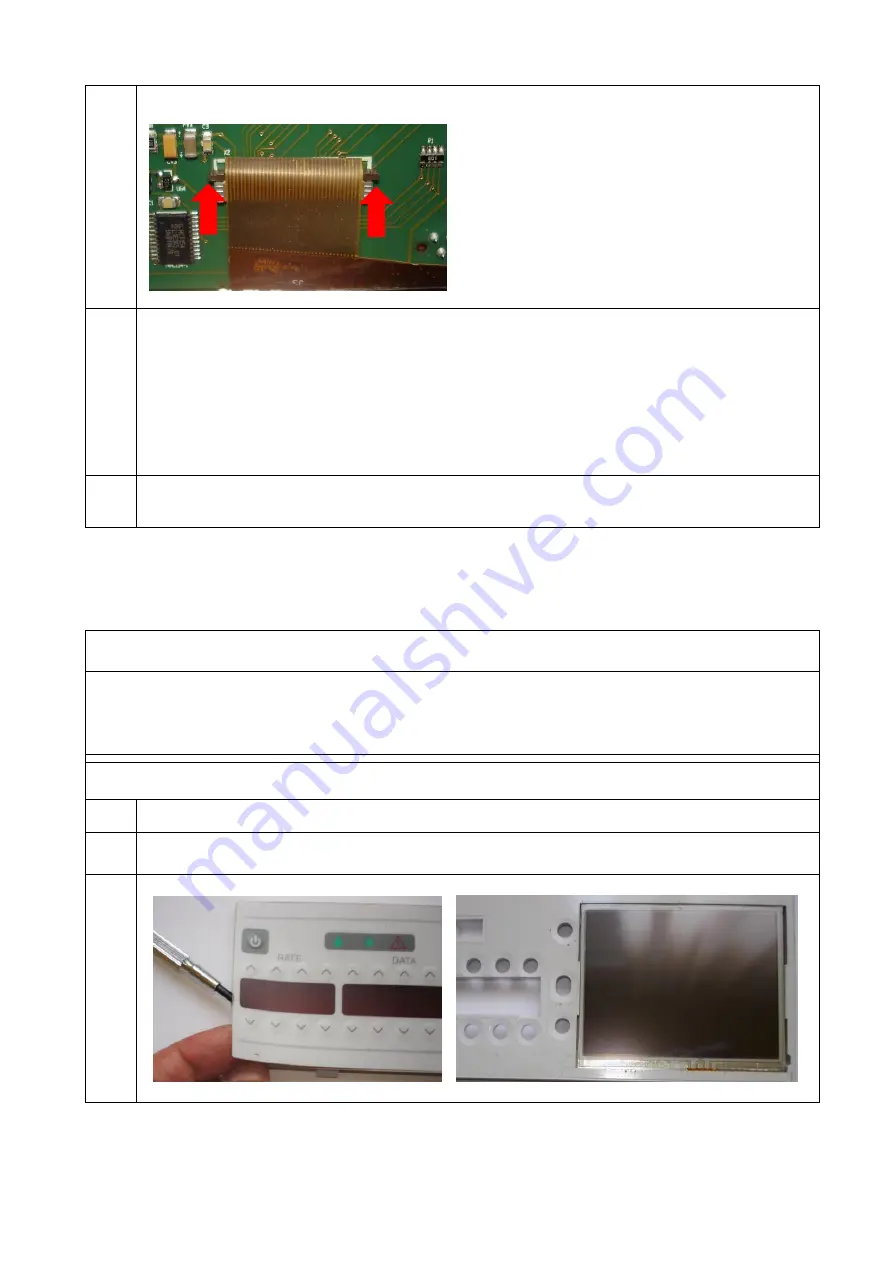
SH-7000-Chroma-EN-04/17
31
4.
Carefully detach the Touch screen cable
5.
Connect the Touch screen cable on the new Display pcb
Solder the AIL sensor cables
Install the Display pcb
Insert three screws
Connect the Flat cable
When reassembling the rear door cover, the order of the screws must be observed
The shortest screw must be used at the indicated position
Seal the new Door side sticker
6.
To update the Display pcb, follow the procedure described on 6.3
5.12
Replacement of the Touch Screen and Front Foil
Tools & recommended spare parts:
- Antistatic work place
- Phillips screw driver No.1
- LCD (73167)
- Foil (76167)
Procedure:
1.
Dismantle door (5.9)
2.
Remove Display pcb (5.10)
3.
Remove Front foil.
Summary of Contents for Volumed nVP7000 Chroma
Page 1: ...Edition 4 17 ...
Page 47: ...SH 7000 Chroma EN 04 17 47 ...
Page 48: ...SH 7000 Chroma EN 04 17 48 ...