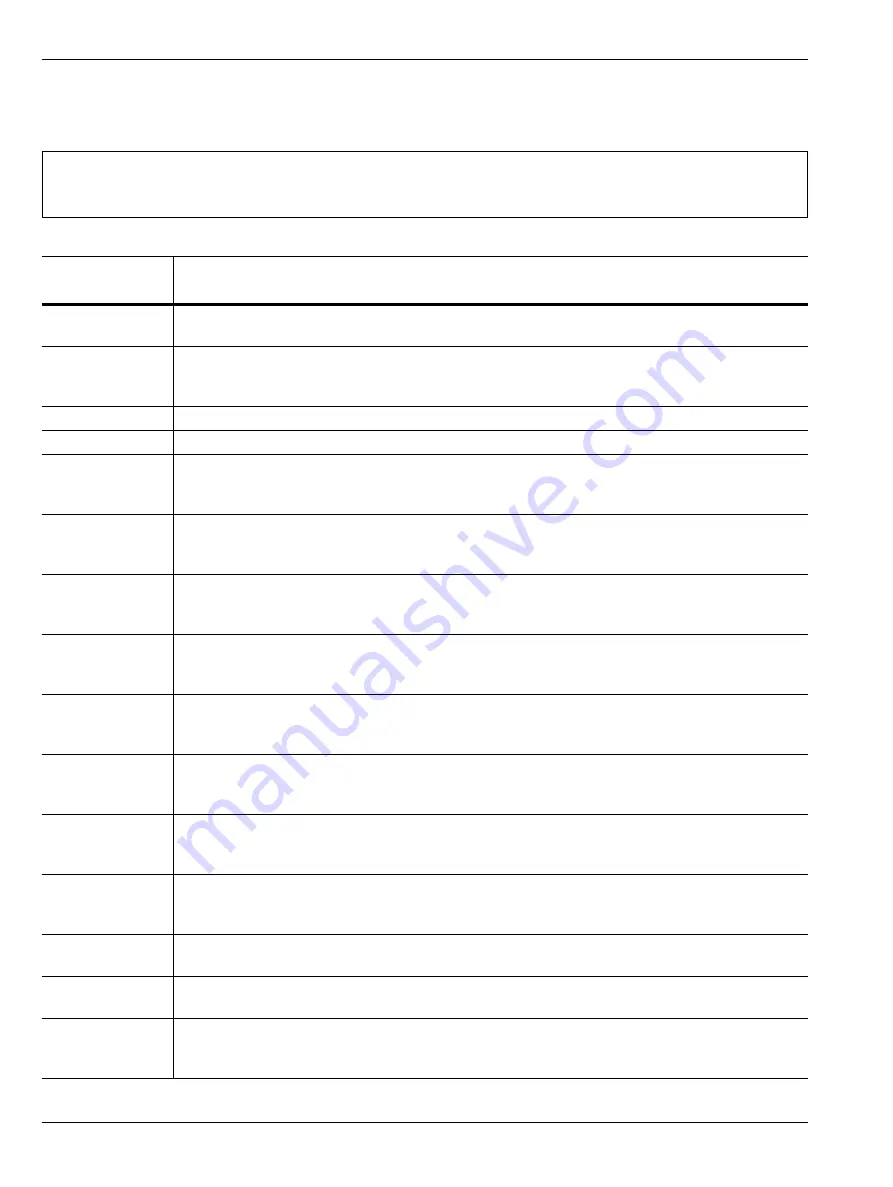
2-5 3739C Test Set Replaceable Subassemblies and Parts
Replaceable Parts
2-6
PN: 10410-00306 Rev. F
VectorStar ME7838 Series MM
2-5
3739C Test Set Replaceable Subassemblies and Parts
Replaceable parts of 3739C Test Set are listed in
below.
Note
Instruments shipped to European Union countries after 22nd July, 2017 are compliant with the
requirements in the RoHS Directive, officially known as Directive 2011/65/EU. RoHS compliant
replacement parts must be used to repair RoHS compliant instruments
Table 2-4.
3739C Broadband Test Set Replaceable Parts List (1 of 2)
Replacement
Part Number
Description
3-40-183
Power Supply; RoHS Compliant
• Does not include cable harnesses, see ND73168 below
3-ND73168
Power Supply Cable Harness
• 3-71918; RoHS Compliant
• Does not include Power Supply, see 3-40-183 above
ND80352<R>
A1 Bias Control PCB Assembly – 3-80120-3
3-ND80352<R>
A1 Bias Control PCB Assembly – 3-80120-3; RoHS Compliant
ND75883<R>
A100, A101 Doubler Module
• 74094
• Does not include 3-803-104 Bias/Control ribbon cable
3-ND75883<R>
A100, A101 Doubler Module
• 3-74094; RoHS Compliant
• Does not include 3-803-104 Bias/Control ribbon cable
ND75884<R>
A103 RF Amplifier Module, consists of:
• 3-71907-1 – soldered-on cable harness, to A1 PCB Connector P1.
• 73619 – 8 GHz to 40 GHz Amplifier
3-ND75884<R>
A103 RF Amplifier Module, consists of:
• 3-71907-1 – soldered-on cable harness, to A1 PCB Connector P1.
• 3-73619 – 8 GHz to 40 GHz Amplifier; RoHS Compliant
ND75885<R>
A105 RF Amplifier Module, Port 1, consists of:
• 3-71907-2 – Soldered-on cable harness, to A1 PCB Connector P2.
• 73619 – 8 GHz to 40 GHz Amplifier
3-ND75885<R>
A105 RF Amplifier Module, Port 1, consists of:
• 3-71907-2 – Soldered-on cable harness, to A1 PCB Connector P2.
• 3-73619 – 8 GHz to 40 GHz Amplifier; RoHS Compliant
ND75886<R>
A106 RF Amplifier Module, Port 2, consists of:
• 3-71907-3 – Soldered-on cable harness, to A1 PCB Connector P3.
• 73619 – 8 GHz to 40 GHz Amplifier
3-ND75886<R>
A106 RF Amplifier Module, Port 2, consists of:
• 3-71907-3 – Soldered-on cable harness, to A1 PCB Connector P3.
• 3-73619 – 8 GHz to 40 GHz Amplifier; RoHS Compliant
70242<R>
A104, SPDT Switch, 0.04 to 40 GHz
• Does not include SPDT Switch Control PCB Assembly – ND70926 – 64951-3 (below)
3-70242<R>
A104, SPDT Switch, 0.04 to 40 GHz; RoHS Compliant
• Does not include SPDT Switch Control PCB Assembly – 3-ND70926 – 3-80736-3 (below)
ND70926<R>
SPDT Switch Control PCB Assembly – 64951-3
• Does not include M-M ribbon cable for connection to A1 PCB Connector P5
• Mounts on top of A104 SPDT Switch – 70242 (above)
Summary of Contents for VectorStar ME7838 Series
Page 2: ......
Page 94: ...5 3 ALC Level Calibration Adjustment 5 18 PN 10410 00306 Rev F VectorStar ME7838 Series MM ...
Page 177: ......