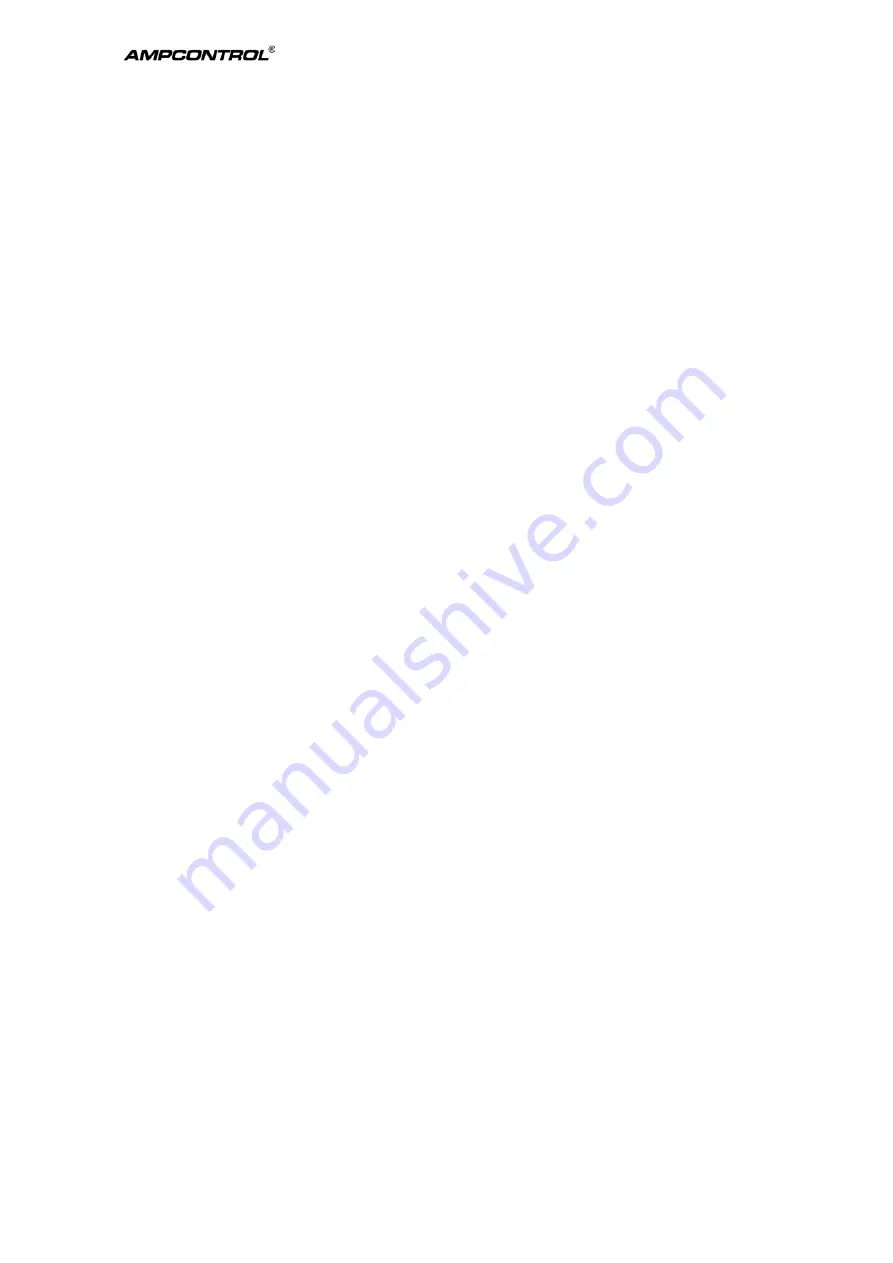
GASGUARD IS CONTROLLER Issue: R2, Date: 26/09/2011, CRN: 7502
Page 36
6.2.2
Checking Controller Functionality
Once the configuration setting has been made, the overall Controller functionality must be verified across all of its
expected operating conditions. This will typically consist of driving each active Controller input channel from a zero
input signal all the way up to and beyond the channel’s full scale value. During the time each channel is driven,
observations, checks and measurements must be made of alarm points, relays, current repeater outputs and display
values. A record of Controller test results should be recorded on the test form.
A channel may be driven either by its connected sensor, or by a device that simulates the signal from that sensor. If
the sensor itself is used, then some means of stimulating it will be needed. In the case of a gas detector, this would
be a cylinder of calibration gas. For other sensor types such as pressure, temperature, flow and humidity, it may be
difficult to create the conditions required to drive the connected controller channel over the required range to allow
proper testing. It is more convenient to simulate the output of a sensor using a device such as a loop
calibrator/simulator. This device (signal simulator) provides accurately adjustable levels of voltage or current that can
be injected into the Controller’s input channels.
Assuming a signal simulator is used to provide channel input signals, a typical test sequence would be:-
•
Connect the signal simulator to the input channel to be tested
•
Set the simulator to provide zero input signal (0V or 0mA)
•
Observe the display value for that channel – is it reading correctly ?
•
Observe the alarm and Fault LEDs – are they correctly illuminated for the given configuration settings ?
•
Measure the relay contacts with a continuity meter – are the appropriate contacts in the correct state per the
configuration settings ?
•
Measure the current follower outputs – are the outputs correct per the configuration settings ?
•
Increase the input signal and continue the same checks as above as the signal passes through each
configured alarm trip-points.
•
Check for correct operation of any configured alarm delays.
•
Check that latched alarms remain when the input is reduced below the alarm trigger point.
•
Ensure that when powered down and back up again, the latched alarm states are re-instated.
•
Ensure that following an alarm reset from the front panel (if this is enabled in the controller configuration), all
alarms clear and relays reset to non-alarm state (input signal set below all alarm set-points).
•
Ensure that following an alarm reset from the remote reset input, all alarms clear and relays reset to non-
alarm state (input signal set below all alarm set-points).
•
Check that any digital communications to other devices is working correctly (check Modbus settings and
operation).
When all Controller operations have been checked and verified as working, the test record should be signed off and
stored in a secure place for future reference.
Summary of Contents for gasguard
Page 47: ...GASGUARD IS CONTROLLER Issue R2 Date 26 09 2011 CRN 7502 Page 46 ...
Page 62: ...GASGUARD IS CONTROLLER Issue R2 Date 26 09 2011 CRN 7502 Page 61 B2 Main Menu Flowchart ...
Page 63: ...GASGUARD IS CONTROLLER Issue R2 Date 26 09 2011 CRN 7502 Page 62 B3 Calibration Flowchart ...
Page 64: ...GASGUARD IS CONTROLLER Issue R2 Date 26 09 2011 CRN 7502 Page 63 B4 Configuration Flowchart ...
Page 74: ...GASGUARD IS CONTROLLER Issue R2 Date 26 09 2011 CRN 7502 Page 73 Appendix C Approvals ...
Page 75: ...GASGUARD IS CONTROLLER Issue R2 Date 26 09 2011 CRN 7502 Page 74 ...
Page 76: ...GASGUARD IS CONTROLLER Issue R2 Date 26 09 2011 CRN 7502 Page 75 ...
Page 77: ...GASGUARD IS CONTROLLER Issue R2 Date 26 09 2011 CRN 7502 Page 76 ...
Page 78: ...GASGUARD IS CONTROLLER Issue R2 Date 26 09 2011 CRN 7502 Page 77 ...
Page 79: ...GASGUARD IS CONTROLLER Issue R2 Date 26 09 2011 CRN 7502 Page 78 ...