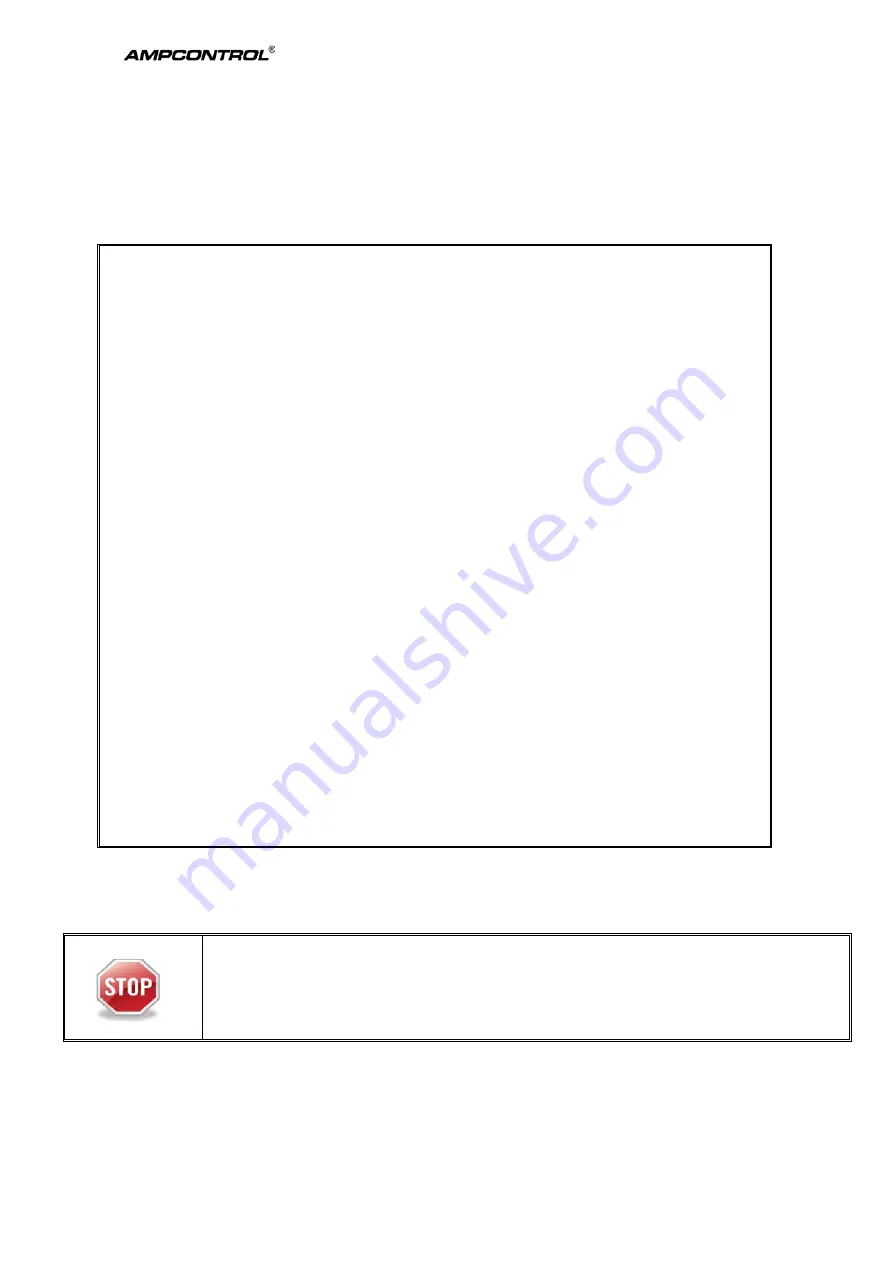
GASGUARD IS CONTROLLER Issue: R2, Date: 26/09/2011, CRN: 7502
Page 9
2.3
Operational Restrictions and Limitations
The operational restrictions listed below must be understood before considering using the Gasguard controller within
systems designed to ensure the safety of personnel. Using the Controller in a manner that exceeds its electrical,
functional or physical specifications, or in a way that is contrary to its operating restrictions, may create risks to
personnel and/or equipment resulting in injury or death.
2.4
Conditions of Conformity – Ex ia
The Gasguard Controller is designed to operate as part of a Safety Instrumented System, alongside other
equipment that collectively form the means to minimise the risk of injury or death to personnel.
•
The selection, installation, commissioning and use of this protective device should only be undertaken
following the application of a detailed risk assessment that is consistent with the methodology
outlined in AS/NZS ISO 31000 risk management. Additionally, identified risk control measures
identified within the risk assessment additional to safety controls and/or directions contained within
the products operating manual must be validated as effective before use of the product in any
capacity.
•
The Gasguard controller is NOT designed to be used as the sole means of ensuring safety to
personnel or equipment.
•
The Gasguard controller does NOT have an associated Safe Failure Fraction (SFF).
•
The Gasguard controller is NOT certified for use in Group II hazardous area applications
•
The Gasguard controller is NOT to be considered as a PLC since the device does not support full logic
decoding of input alarm conditions and output relay actions.
•
The Gasguard controller is NOT water resistant and must be mounted within a suitably IP rated
enclosure for use where the overall system is to be rated water resistant
•
The Gasguard controller is NOT on-site repairable and contains no user serviceable parts.
•
The Gasguard controller must NOT be modified in any way. A controller that differs in any way from
its ‘as-certified’ condition must not be used.
•
A Gasguard controller showing any visible signs of damage must not be used.
•
Sensors and Power Supply connected to the Gasguard controller must comply with the requirement
of I.S. configuration.
•
Cleaning the controller may create an electrostatic hazard. Anti-static cleaning media must be used.
WARNING!
To comply with the Conditions of Certification, ensure full serviceable life of the product, and avoid
nullifying the warranty, it is essential to exercise great care with the installation, use and storage of the
System components. Failure to comply with the Conditions of Certification (
Appendix C – Approvals
) may
seriously compromise the integrity of the system and/or its components, and the consequence could be
fatal. The user must ensure that the “Conditions of Safe Use” outlined in the certificate are met or the
certificate (and the IS rating) will not be valid.
Summary of Contents for gasguard
Page 47: ...GASGUARD IS CONTROLLER Issue R2 Date 26 09 2011 CRN 7502 Page 46 ...
Page 62: ...GASGUARD IS CONTROLLER Issue R2 Date 26 09 2011 CRN 7502 Page 61 B2 Main Menu Flowchart ...
Page 63: ...GASGUARD IS CONTROLLER Issue R2 Date 26 09 2011 CRN 7502 Page 62 B3 Calibration Flowchart ...
Page 64: ...GASGUARD IS CONTROLLER Issue R2 Date 26 09 2011 CRN 7502 Page 63 B4 Configuration Flowchart ...
Page 74: ...GASGUARD IS CONTROLLER Issue R2 Date 26 09 2011 CRN 7502 Page 73 Appendix C Approvals ...
Page 75: ...GASGUARD IS CONTROLLER Issue R2 Date 26 09 2011 CRN 7502 Page 74 ...
Page 76: ...GASGUARD IS CONTROLLER Issue R2 Date 26 09 2011 CRN 7502 Page 75 ...
Page 77: ...GASGUARD IS CONTROLLER Issue R2 Date 26 09 2011 CRN 7502 Page 76 ...
Page 78: ...GASGUARD IS CONTROLLER Issue R2 Date 26 09 2011 CRN 7502 Page 77 ...
Page 79: ...GASGUARD IS CONTROLLER Issue R2 Date 26 09 2011 CRN 7502 Page 78 ...