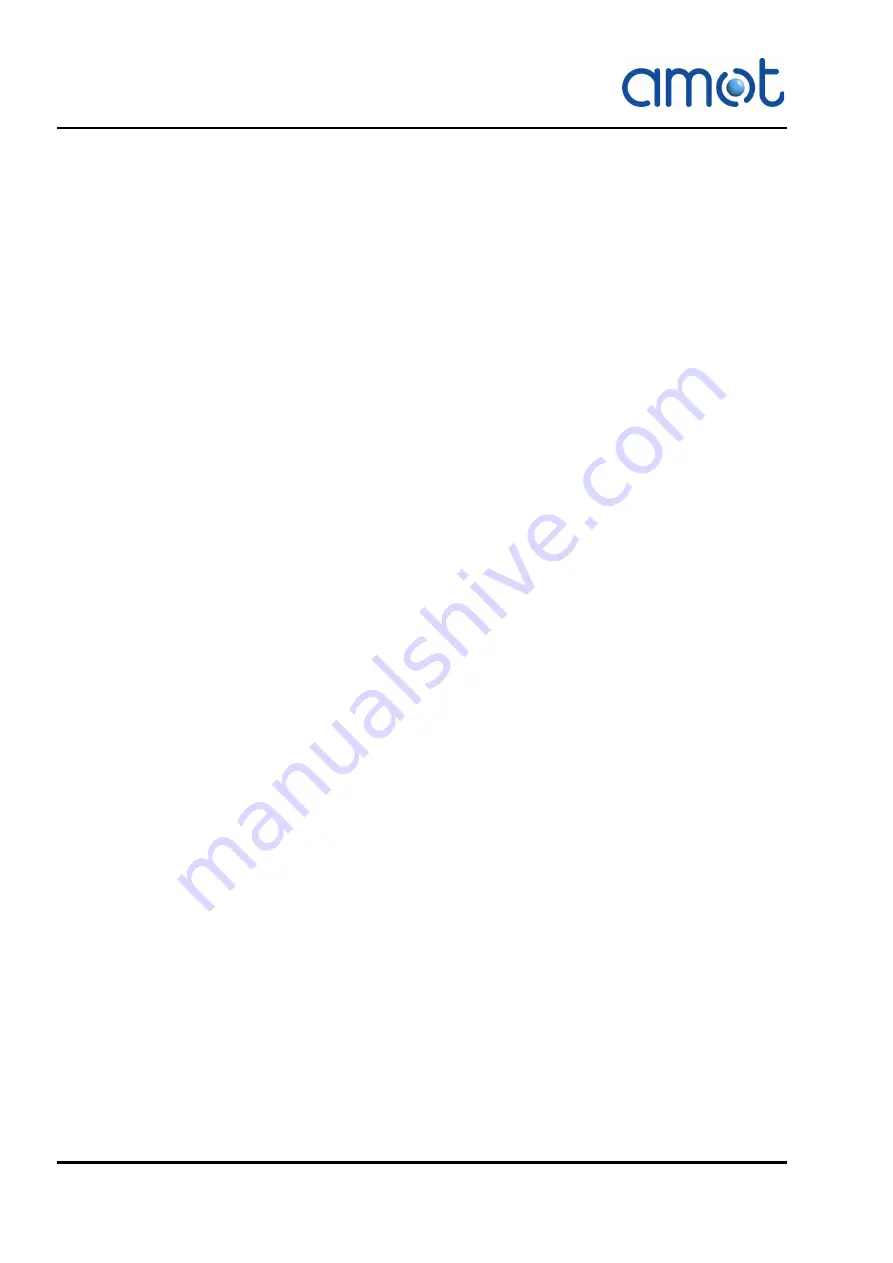
32
Electric Actuator
Rev 12 – NOV 2019
OMMG00012
4.5
Electrical Installation
The following precautions and limitations must be observed before electrical
connection of the actuator.
CAUTION
Electrical power must not be supplied to both the open and close
motor windings at the same time or overheating will occur. When
power is applied to either the open or close windings, the other must
be isolated.
If multiple actuators are controlled from the same DPDT control
switch, it is possible that the first actuator to reach end of travel will
reverse direction due to the supply being available from the common
control switch. When several actuators need to be controlled in
parallel with one 3 position control switch, each actuator must have
separate contacts.
•
Power supply must be free from excessive voltage transients (spikes).
•
The power supply must be fused at 1.5 to 2 times the rated current.
•
Check the motor nameplate and ensure the actuator voltage is correct for
the local power supply.
•
Use wire with the correct gauge and insulation (Follow standards
prescribed by the relevant electrical regulations).
•
The actuator chassis must be correctly grounded.
•
Use the appropriate cable glands for weather proof or explosion proof
environments.
•
All unused electrical entries must be blanked off with the appropriate
plug.
•
Make all splices or connections using the correct pin connector of terminal
strip.
•
Ensure the connections comply with the system wiring diagram (Section
•
Control lines must be correctly shielded.
•
Keep the motor compartment clean and dry at all times.
•
Cable must be routed inside the actuator as illustrated in Fig 10 to avoid
the possibility of interfering with moving parts.
•
When the 4-20mA input and output signals are used, it is recommended
that these signals are protected with 50mA quick blow fuses.
Summary of Contents for 10GEF
Page 2: ......
Page 14: ...14 System Overview Rev 12 NOV 2019 OMMG00012...
Page 52: ...52 Electric Actuator Rev 12 NOV 2019 OMMG00012...
Page 54: ...54 PID Controller Rev 12 NOV 2019 OMMG00012...
Page 64: ...64 System Integration Rev 12 NOV 2019 OMMG00012 Fig 22 System Wiring Diagram 8072D Controller...
Page 67: ...67 System Integration OMMG00012 Rev 12 NOV 2019...
Page 68: ...68 System Integration Rev 12 NOV 2019 OMMG00012...
Page 74: ...74 Technical Data Rev 12 NOV 2019 OMMG00012 9 1 1 Valve Bore Fig 25 Valve Selection Curve...