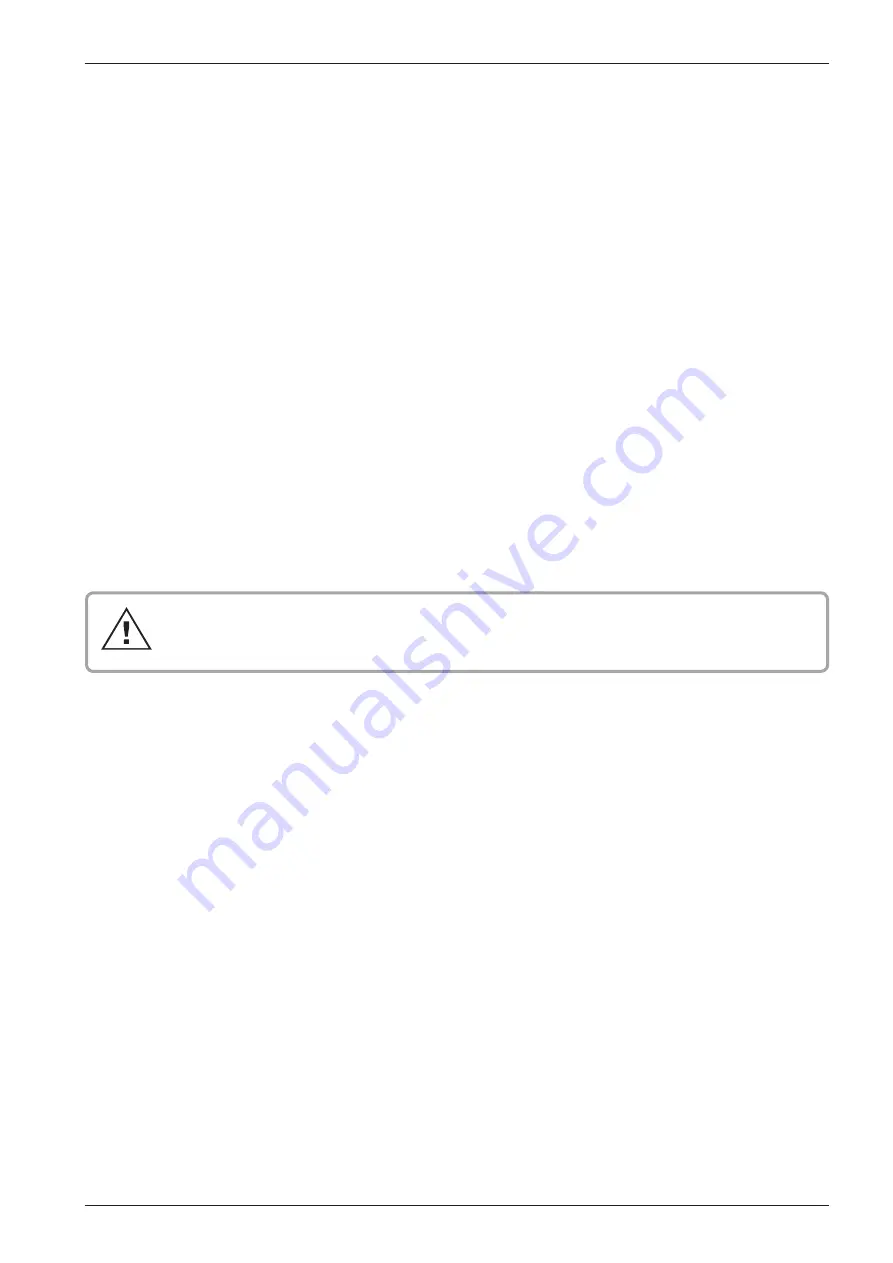
69
AV 70 X
OPERATION MANUAL
Travel in CRAB mode
This function is used to adjust extended track during Machine travel.
Use potentiometer (2) to adjust travel speed, and use travel controls (1) to adjust its direction.
Press pushbuttons (5) and (6) on travel controls (1) to control the Machine in CRAB mode, and at the same you may turn the Machine.
Shift the travel controls (1) to opposite position via (0) and then return to (0) position within the interval of 1 second to stop the Ma-
chine – the engine will continue to run.
By deflecting the travel controllers (1) from the position (0), the machine drives off.
Turning ON:
Press button (5) to deflect the front drum to the right and press button (6) to deflect to the left, the indicator lamp on cluster (26) will
light up to signal this function.
Max deflection of the front drum to both sides is 180 mm.
Turning OFF:
Press switch (4) to cancel CRAB mode of front drum.
Indicator lamp on cluster (26) will go OFF to signal CRAB mode has been reset.
Note
In the event that the control lamp on the combined instrument (26) is flashing, hold the switch and turn the steering wheel (to the left/
right) until the control lamp goes out.
If the Machine is equipped with cutter and final compactor, then pushbuttons (5) and (6) on travel control (1) on the same side where
it has been mounted, are used to control it. Then pushbuttons (5) and (6) on the second travel control (1)) are used to control the Ma-
chine in CRAB mode.
Take special care when Machine travels in CRAB mode near constructed facilities so to avoid their dam-
age due to any collision (hitting)!
If necessary, fold the external mirrors!
Summary of Contents for AV 70 X
Page 1: ...Book ID 4 P06406CU AV 70 X Cummins EN Operating manual...
Page 2: ......
Page 4: ......
Page 5: ...M sto a datum vyd n Place and date of issue Ort und Datum der Ausgabe...
Page 6: ......
Page 14: ...8 AV 70 X...
Page 15: ...9 AV 70 X SPECIFICATION MANUAL 1 SPECIFICATION MANUAL AV 70 X Cummins Tier 3...
Page 19: ...13 AV 70 X O W1 W2 H3 H2 W3 406003 SPECIFICATION MANUAL...
Page 23: ...17 AV 70 X SPECIFICATION MANUAL Notes...
Page 24: ...18 AV 70 X...
Page 25: ...19 AV 70 X OPERATION MANUAL 2 OPERATION MANUAL AV 70 X Cummins Tier 3...
Page 26: ...20 AV 70 X...
Page 40: ...34 AV 70 X...
Page 56: ...50 AV 70 X 400501A 26 2 6 Machine basic functions control...
Page 68: ...62 AV 70 X 12V 0 406005 0 1 V 2 2 3 4 1 2 7 Machine basic functions control...
Page 70: ...64 AV 70 X 1 2 MAN AUT 0 kg 0 13 400272E 26 1 2 3 1 0 N 1 2 7 Machine basic functions control...
Page 82: ...76 AV 70 X 1 2 MAN AUT 0 kg 0 10 400272J 26 9 11 2 7 Machine basic functions control...
Page 91: ...85 AV 70 X OPERATION MANUAL Notes...
Page 92: ...86 AV 70 X...
Page 93: ...87 AV 70 X MAINTENANCE MANUAL 3 MAINTENANCE MANUAL AV 70 X Cummins Tier 3...
Page 94: ...88 AV 70 X...
Page 152: ...146 AV 70 X...
Page 160: ...154 AV 70 X Notes...
Page 161: ......